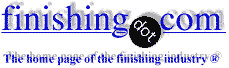
-----
Corrosion Resistance of Ag plated Zn metal
June 16, 2009
We have two different plating thickness with the below layers construction:
Product: Electronic component for automotive
Base material: Zn die casting (Zamak 3)
Layers construction 1:
Cu : 7-10 micron, Ni: 1-3 micron, Ag:8~10 micron
Layers construction 2:
Cu : 7-10 micron, Ni: 8-12 micron, Ag:1~2 micron
Layer construction 1 passed the acetic acid
⇦ on
eBay
or
Amazon [affil link] vapour test and no. 2 failed the test which has heavy corrosion on the Zn.
We thought that thick Ni will help to prevent the Zn from corrosion however looks like thick Ag actually plays a role in corrosion resistance. Not sure if anyone can suggest any theory behind or is it highly recommended to plate Ag as thick as possible in order to pass the test (of course, cost will be an issue).
product designer - Penang, Malaysia
Zinc Die casting are difficult to protect from corrosion. Porosity in the casting will defeat efforts to protect. I suggest looking at the casting quality, take steps to minimize porosity. also increase the nickel thickness not the silver thickness.
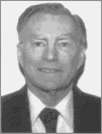
Don Baudrand
Consultant - Poulsbo, Washington
(Don is co-author of "Plating on Plastics" [on Amazon or AbeBooks affil links]
and "Plating ABS Plastics" [on Amazon or eBay or AbeBooks affil links])
June 19, 2009
I agree with Don. Just a note though, Ni Sulphamate has better corrosion resistance than Ni Sulphate. You didn't mention which Ni bath you were using.
Mark BakerFellow Plater - Syracuse, NY, USA
June 25, 2009
Q, A, or Comment on THIS thread -or- Start a NEW Thread