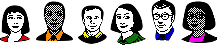
Metal finishing Q&As since 1989
-----
Coatings & Treatments For Aluminum Concrete Forms
Current question and answers:
January 27, 2021Q. Hello,
Looking for a recommended coating material, combination of finishes, or process to apply to galvanized HRPO steel and cast aluminum parts that would provide the following:
Durability (abrasion resistant): This product will be used in a construction environment and often abused and/or drug into place against a concrete surface. Chip resistance is desired as well.
UV resistance: This is a durable product meant to be used and stored outdoors when not in use.
Low Surface Energy: The desire here would be for a low-surface energy coating that would reduce adhesion between the surface and spilled fresh concrete for ease of cleaning once the concrete has partially cured and the product is no longer in use.
Chemical / PH resistance: The coating may be subject to highly alkaline materials, solvents, and other chemicals associated with the casting of concrete. Preclude contact between concrete and aluminum to avoid potential reaction between these materials
Galvanic isolation: electrically isolate the two dissimilar materials to preclude the concern for galvanic action.
Low maintenance: We would like a coating that would be relatively hands-off under normal use.
Please let me know if you have any suggested coatings or processes that you think would make sense for either of these materials that would be appreciated. I have been looking at a number of powder coats, ceramic coatings, and/or hydrophobic coatings as a start. For the aluminum components I was also looking at anodizing but unsure how it would perform on all the objectives above. Thanks in advance for your responses!
- Des Moines Iowa
A. I suggest to look at such spray applied heat cured polmers as "Plascoat PPA571" or perhaps "Abcite" (parts of the Axalta range - I'm not associated with them). These are thermoplastic coatings. You can download data sheets from the Axalta website and see if this meets the needs you describe.
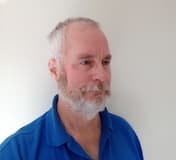
Geoff Crowley
Crithwood Ltd.

Bathgate, Scotland, UK
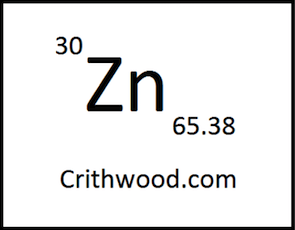
January 29, 2021
⇩ Closely related postings, oldest first ⇩
Q. I am a consultant working on behalf of a significant U.S. manufacturer of aluminum forms for pouring concrete walls (residential construction)for basement structures. Customers ask that the face of the aluminum forms be etched (or treated )so that, on the first use of the form, the hydration reaction of the curing concrete will not react with the aluminum form to cause bubble marks and bubble paths up the face of the concrete wall. The first few walls poured with a new set of forms have surface flaws caused by the concrete / aluminum reaction. We are seeking a surface treatment to use during production of the forms which will eliminate this initial reaction. The present method of treatment is to roll lime slurry onto the surface of the forms. This treatment looks terrible and is sometimes ineffective.
We would prefer a treatment whereby the face of the completed form could be dipped (not the entire form)into a solution which would react with the face and then could be washed and neuturalized in an automated line process. The forms are hand mopped with lime, one at a time, in the existing process.
Thank you in advance for your reply/replies.
Wendall KitchensAluminum Forms for concrete - Atlanta, Georgia, USA
2004
A. The bare aluminum is probably oxidizing and generating Hydrogen gas when contacted by the wet concrete. Once a natural oxide layer is formed, the reaction slows down or stops. Anodizing is a forced, controlled oxidation of the aluminum. Hardcoat anodizing is a thicker, denser version of anodizing. Hardcoating would also control the oxidation process and extent the wear life of your forms.
Chris Jurey, Past-President IHAALuke Engineering & Mfg. Co. Inc.

Wadsworth, Ohio
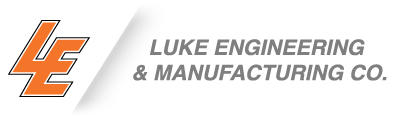
2004
Q. We are a manufacture of Aluminum Forms for concrete construction. There has always been a problem with reaction to wet cement to the aluminum forms. Along with this reaction (witch produces a nasty looking wall for the 1 few uses until the aluminum is etched and there is a barrier formed on the surface of the aluminum) is a sticking problem. The cement likes to adhere itself to the surface of the aluminum and needs to be scraped of prior to reusing the forms. There are many things that can be done to minimize this which include using a dehydrated lime solution as a pretreat. There have been hundreds of other things tried but nothing so far has proven to be reliable. Oils are used at the time of pouring the cement and that does help. Do you have any recommendations?
Dan DuggerProduct designer - Bates City, Missouri, USA
June 1, 2009
A. My suggestion is to investigate epoxy powder coating or if available State side epoxy phenolic PC. The epoxy film is very resistant to the alkali environment produced by cement and plaster and it will also resist most oils. Just make sure the substrate is properly pretreated prior to the application of the powder. Should last years.
Terry HicklingBirmingham, United Kingdom
June 3, 2009
A. Any alkali including lime, including city water with a pH of 8, or anything above pH 7 will attack (1) all aluminum alloys, (2) aluminum oxide (anodizing) (3) hydrated aluminum oxide (sealed anodizing). The epoxy mentioned above will work if you can afford it. Nickel electroplate or electroless nickel will also work if you can afford it.
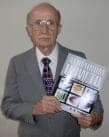
Robert H Probert
Robert H Probert Technical Services

Garner, North Carolina
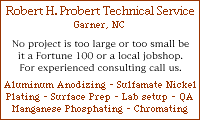
June 4, 2009
A. I have used aluminum extrusions for mold side rails. They had standard anodizing. I was distressed at the first usages as the concrete stuck horribly, although it was a weaker lightweight concrete so not possessed of regular tensile strength.
It ended up taking about six pours of the mold to finally stop the reaction and get a clean release. After that point they behaved fine, but only by using a secret ingredient (very common) as the release.
One attempted solution was to use a sodium hydroxide solution to pre-react the extrusions. It might have helped reduce the number of bum mold usages, but still required multiple pours to finally stop the sticking.
- Roberts Creek, British Columbia
March 30, 2011
Treatment for Concrete Release on Forms
Q. Looking for a coating to be applied to carbon steel molds which we use for a concrete composite mixture.
Right now we have glossy finish powder coated molds which we spray a thin layer of soy oil on for easy release; problem is the oil makes a terrible mess of things.
Any coating advise would be great!
Thanks for your time!
- waverly Iowa, usa
April 16, 2018
Q, A, or Comment on THIS thread -or- Start a NEW Thread