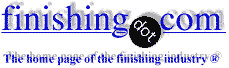
-----
Does hot dip galvanizing weaken steel?
Q. Does HDG affect Mechanical Properties of Steel?
If so how & how much ?
Can anybody help guide?
- Lahore, Punjab, Pakistan
June 12, 2021
A. Generally, HDG does not change the mechanical properties of steel. I did some research on this for the process of re-galvanizing motorway barrier, and we did extensive mechanical testing before and after. The results showed a slight increase in tensile strength of the steel, but not statistically significant. In other words, no effect.
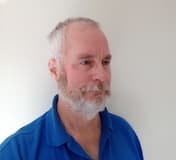
Geoff Crowley, galvanizing consultant
Crithwood Ltd.

Bathgate, Scotland, UK
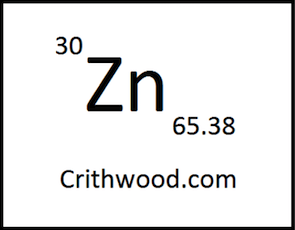
June 23, 2021
⇩ Related postings, oldest first ⇩
Q. Sir
We have a component manufactured for the Wind Mill Tower, which is a mounting bracket (10 mm Thick) used to mount the Platforms at the various levels of the tower. This bracket is material grade S355 equivalent Indian Standard IS-2062. It is a mild carbon steel. This bracket has a 90 degree bend and gets clamped at both ends at a right angle. This material is Hot Dip Galvanized.
We are finding cracks at the assembly stage from the bending line (Bending is at a radius of R16. We have done testing at our end by loading the component as done at the ass'y stage: the pieces without galvanizing did not fail, but the pieces after galvanizing tested after 3 days of galvanizing failed from the radius. Is the galvanization process playing the key roll for the failure?
Regards,
Fabrication - Hyderabad, Andhra Pradesh, INDIA
April 30, 2009
? Is the actual steel failing or just appears to be cracked because the galvanize cracked.
If the part went into the zinc vertically, I can not see a good reason for it to crack.
Dr. Cook will probably have technical reasons in a day or so.
- Navarre, Florida
May 1, 2009
May 5, 2009
A. Hi Benny,
I infer that you are doing the bend cold (less than around 600 °C), otherwise your problem wouldn't occur. The hot dip galvanizing is causing your problem, because the bend radius is too tight for a cold bend.
Onesteel Australia have published an FAQs document dealing with concrete reinforcing bar, including the galvanizing of cold-bent bar. Here is the relevant FAQ cut from the document (which does not carry a copyright note):
"A. Bent rebars that are subsequently galvanized can be affected in a number of ways. Heating of the steel to 450 degrees C will induce some degree of strain aging into the cold worked section of the steel. Immersion in a pickle bath to clean the steel may induce some hydrogen embrittlement in the steel. Immersion of steel in a molten metal zinc bath can cause liquid metal embrittlement due to absorption of zinc into the steel grain boundaries.
"For these reasons bars should not be bent around pins of less than 5 db for bars up to 16 mm and 8 db for bars greater than 16 mm. It is preferable to bend bars after galvanizing in order to overcome any potential for small surface folds, that may be formed in the bar surface during bending around small pins, to become a surface cracking problem in bent and galvanized rebars. We do not recommend that pre-bent and galvanized bars be re-bent on site."
If we apply the Onesteel radius limit for bar, to your plate, you would have a limit of R25. Maybe the limit should be higher than that because of the different geometry of plate vs bar. Either way your R15 is too tight.
Assuming that you need the R15, and assuming that you don't need the additional strength at the bend brought about by the cold work, you could do the bend then temper at around 650 degrees C then go to hot dip galvanizing. The temper would remove the effects of the cold work.
Or you could heat the strip to around 900 °C with a torch and bend it hot then let it cool naturally, which would give you no cold-work effects at all since you would not be doing any cold work.
Or you could hot dip galvanize the strip first, then bend it cold. Obviously you would need to run some test pieces first to check how tight the bend could be without the zinc being damaged. A matter of absolutely major importance is the silicon content of the steel, because certain silicon contents in the steel can lead to brittle zinc coatings which would crack on a tight bend (although their corrosion resistance is normal). This post is already quite long enough without going into the silicon question in detail, but we can deal with it if you wish.
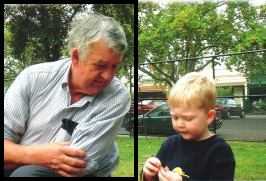
Bill Reynolds [deceased]
consultant metallurgist - Ballarat, Victoria, Australia
We sadly relate the news that Bill passed away on Jan. 29, 2010.
A Guide to process Selection & Galvanizing Practice"
by M. J. Hornsby
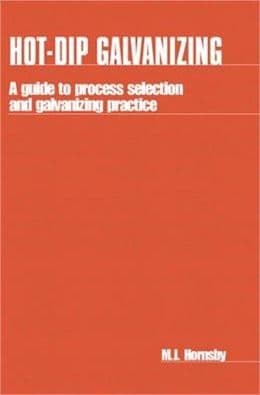
on eBay or Amazon
or AbeBooks
(affil link)
A. Sir:
I take a different point of view about your problem. Since the non-galvanized bracket does not break, I believe that is proof enough that the galvanizing caused the problem. If you post publicly, or e-mail me privately the composition of the galvanizing bath in which these brackets were galvanized, I would be happy to comment.
Regards,
Galvanizing Consultant - Hot Springs, South Dakota, USA
That's what I said in my first paragraph: "The hot dip galvanizing is causing your problem...". Dr Cook, what are you disagreeing with?
If an amount of cold-work exceeding some threshold level is done prior to galvanizing, then the subsequent galvanizing will cause a problem in that cold-worked material.
Possible solutions are (1) reduce the amount of cold work if the application permits (that is, use a larger bend radius), or (2) bend hot so that no cold-working is done - subsequent galvanizing will then not damage the bend zone.
Or (3) galvanize first then bend, but be aware that the silicon content of the steel is important, to avoid a brittle zinc layer that might crack when bent.
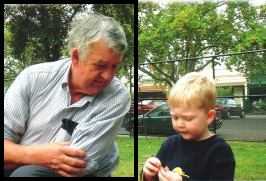
Bill Reynolds [deceased]
consultant metallurgist - Ballarat, Victoria, Australia
We sadly relate the news that Bill passed away on Jan. 29, 2010.
May 18, 2009
May 22, 2009
Bill,
I found your technology on bending quite interesting and this may well be exactly what is causing the problem.
I was thinking that the galvanizer of these brackets may be using more than 0.3% tin (Sn) in his zinc which has caused many, many cracking problems in Europe and North America. Unfortunately I could not get information about the zinc in the kettle to verify my thinking.
Galvanizers have found that tin in their zinc reduces zinc usage, perhaps by lowing the freezing point of the zinc allowing better zinc drainage back into the kettle. Unfortunately this tin content, above about 0.3% causes cracks in stressed steel and MANY failures have been reported including:
1)Hanging wires breaking in galvanizing plants in the zinc.
2)Overhead highway signs cracking.
3)Stressed steel bridges failing.
4)Pipe pilings splitting sometimes like a banana being peeled.
5)A stadium roof structure cracking and needing braces.
6)Rectangular welded structures cracking and breaking.
7)Scaffolding cracking and failing.
One company in a patent recommended 0.5% tin and since has lowered this recommendation to 0.2%. Another company recommended above 1% tin and is contained in their patent. The second company has been successfully sued.
Tin causing the cracking has been carefully studied and PROVEN to be the problem. In any case of failure the failed galvanized product can be tested tin can be proven to be the cause.
About eight years ago I became aware of the problem and sent two letters to ASTM recommending a limit on the use of tin in hot dip galvanizing. My understanding is that no action was taken by ASTM because "Cook lacked sufficient proof." I have both dated letters and I have the full scientific paper which proves that tin is the problem.
Regards,
Galvanizing Consultant - Hot Springs, South Dakota, USA
May 22, 2009
Dr Cook, thanks for your extra information.
I agree entirely with you that tin in the zinc would be damaging. Steel and molten tin make a very unhappy partnership. Even when the tin is in dilute solution in another molten metal, intergranular penetration by the tin can effectively form microcracks in the steel surface which can then easily propagate when lightly stressed. (The successful use of tinned steel sheet for cans is another story - highly polished steel, very soft steel, different steel microstructure, low service stress, etc etc - and tinplate was made by hot-dip tinning for very many years before electrolytic plating)
But surely the use of tin in the kettle would be unusual? It's not a constituent of zinc blocks from the zinc refinery, so would have to be a deliberate addition. Was it just for the purposes represented by the patents you mentioned?
The information that I quoted from Onesteel in fact deals primarily with the temperature cycle imposed on the steel by the galvanizing process, rather than details of the zinc itself. Similar degradation of the steel properties would occur if a furnace was used to impose the same temperature cycle as occurs in the kettle, on the same amount of work-hardening, in the complete absence of zinc or tin or any other metal.
So there are evidently two distinct paths, each of which leads to premature service failure - excessive cold work followed by galvanizing which imposes a damaging temperature cycle on the bulk steel, or excessive tin in the zinc which causes degradation of the steel surface.
I sympathize with your attempts to get something new into an ASTM spec - it's bad enough trying to get an editorial correction made of an obvious error!
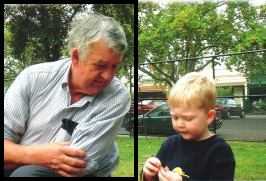
Bill Reynolds [deceased]
consultant metallurgist - Ballarat, Victoria, Australia
We sadly relate the news that Bill passed away on Jan. 29, 2010.
A. The use of tin added to the zinc melt started to be an increasingly common practice in some European countries 10 or so years ago. It has all but stopped I think, perhaps as a result of the problems mentioned above.
The purpose was to change the appearance of the coating, the thickness and the consumption of zinc as a result of that.
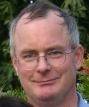
Geoff Crowley
Crithwood Ltd.
Westfield, Scotland, UK
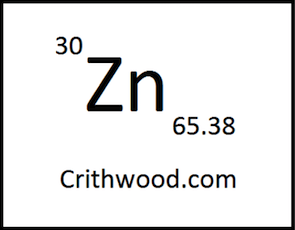
May 27, 2009
Mechanical strength decrease after galvanising
Q. Hi;
I know when a steel part like bolts are hot dip galvanized, they are heat treated and there might be some issues of brittleness id structure. Also I know there are other method of corrosion protection like Sherardizing and Dacromet which has less heating temperature which acts better in terms of hydrogen embrittlement compared with Hot Dip Galv.
Now my question is in case of high strength bolts:
is there any standard or guideline which specifies applying less tightening torque on the structural bolts which are already Hot Dip Galvanized or Sherardized (because of weakening of the bolts after heat induced during mentioned corrosion protection procedures)?
Please refer to a document or a credible source! Thanks.
- Iran
September 7, 2016
A. There's a few statements here that need clarification.
In galvanizing there is not usually any "heat treatment". You might mean that bolts get hot in HDG, that's true, typically 450 °C.
In HDG any risk of hydrogen embrittlement is more often attributed to the acid cleaning than the immersion in zinc.
There are many sources of answers to the question of what torque to apply to HDG bolts, and a search engine will lead you to many of them. Generally higher initial torque is set with HDG than without. For example, see http://www.portlandbolt.com/technical/bolt-torque-chart/
I have not heard of any source of information that suggests bolts are weakened by HDG.
In some research commissioned in Scotland there is evidence that steel strength is very slightly increased by HDG than decreased, but that was not high strength bolts, but in mild carbon steel plate.
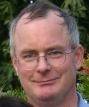
Geoff Crowley
Crithwood Ltd.
Westfield, Scotland, UK
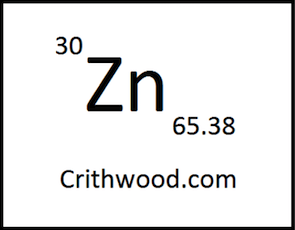
September 9, 2016
Q. Hi Geoff
You are right. I used wrong term. I meant heat transferred during dipping in the molten zinc. (I am non-metallurgist :D)
But for weakening the strength of bolt after HDG, you can check this link:
http://www.portlandbolt.com/technical/faqs/corrosion-resistant-options-for-high-strength-bolts/
As far as I am concerned, the higher coefficient for tightening HDG bolts is due to its surface friction which must be compensated during bolt tightening.
Still I am not worried about my bolts.
- Tehran, Iran
September 13, 2016
A. According to Salim Brahimi, one of the world's leading experts in hydrogen embrittlement, failures of hot dip galvanized fasteners have been attributed to (among other sources) thermal up-quenching .
Brahimi cites primary references (some of his own) as well.
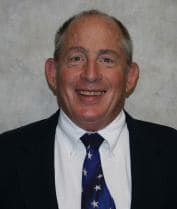
Tom Rochester
CTO - Jackson, Michigan, USA
Plating Systems & Technologies, Inc.

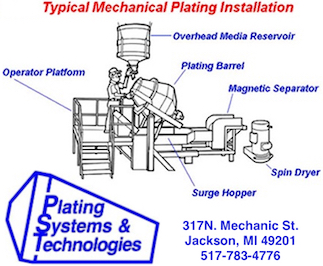
September 28, 2016
Q, A, or Comment on THIS thread -or- Start a NEW Thread