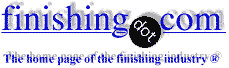
-----
Acid copper plating bath reaction with PMMA
April 2, 2009
Hi there,
As part of my research I am trying to plate single crystal FCC metal nanowires. I started with gold and have no moved on to copper. I use a template based synthesis where I spin PMMA resist on a gold substrate, bake, expose, and develop. I have made features from 25 nm to 25 µm using this lithography method.
To plate single crystal copper, I mixed up a bare bones acid copper plating bath (125 g/L cupric sulphate and 200 g/L sulfuric acid). I use an insoluble Pt anode, a current density between 15 mA/cm2 and 35 mA/cm2 and mechanical stir my solution (roughly 1L in volume).
I have had great plating success with this bath and my set up at room temperature. I have repeatedly plated vertically oriented nanowires with a diameter of 25 nm, 50 nm, 100nm ... etc.
Despite this success, the nanowires are still polycrystalline
(irrespective of current density). The literature suggests running the bath at 60 deg C to achieve single crystal nanowire deposits. So I tried this.
At 60oC the plating did not work, and only features larger than 2.5 µm were plated. I must emphasis, I used identically processed chips for plating at RT and 60 deg C. Features smaller than 2.5 µm which were plated at RT were not plated at 60 deg C.
I expect PMMA is leaching in the solution and insulating my cathode causing the missing features. I know PMMA is susceptible to sulfuric acid only at concentrations greater than 200 g/L, and I expect that with the increased temperature this phenomenon is more pronounced.
What I am wondering: Can I reduce the sulfuric acid concentration in my plating solution and still have enough conductivity? How far could/should I reduce my solution?
Any advice would be greatly appreciated.
Thanks!
-Michael
Researcher - Pasadena, California
Your sulfuric acid concentration seems a bit high to me. I would use a bath comprising about 200-250g/l cupric sulphate and 25-30 ml/l sulfuric acid. Since you are using insoluble anodes, I would not add any chloride ions. This bath can operate at about 30 C, so there shouldn't be any issues with heat. Have you also considered using ABS, PP, PE or MIPS as your template? These are all resilient to sulfuric acid. Also try using a pulsed current - you could get some really good results for nanostructures
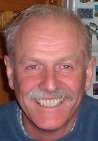
Trevor Crichton
R&D practical scientist
Chesham, Bucks, UK
April 9, 2009
Hi again,
Thanks for the advice, I did just what you said and decreased my acid concentration to 30mL/L (50g/L). In doing so I drastically increased the grain size of my deposits and generated single crystal pillars from 25nm to 750nm, all at RT and 15mA/cm^2. I am looking in to pulse plating right now to increase plating uniformity across the chip and robustness of the process.
I know there are a bunch of other polymers available for templating which are resistant to sulfuric acid, but non will work with electron beam lithography at the resolution that PMMA operates. However, my issue was solved so no need to look into this.
One more question: Why would a lower acid concentration lead to larger grain growth? My best guess is that with a high acid concentration ion motion is dominated by migration through the electric field, but at lower acid concentrations the ion motion is a mix of migration and diffusion. Having the processes slightly diffusion controlled will generate larger grain structures I believe, but I don't know why. Any insights? Any textbooks about this I can read to understand more?
Thanks again!
- Pasadena, California
April 15, 2009
Q, A, or Comment on THIS thread -or- Start a NEW Thread