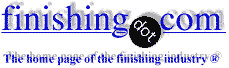
-----
Zinc-nickel on Al diecastings (including Enviralloy Ni)
April 3, 2009
Hello all,
Working in speciality connectors we occasionally have customers who would like to specify an "oddball" finish.
I have a customer that requires a zinc-nickel plate on our diecast electrical connector bodies, with a black chromate finish. The bodies are diecast aluminium with typically fairly high silicon content (LM4 levels, say around 10-12% or so).
Does anyone out there have experience of zinc-nickel on this kind of substrate? Any potential pitfalls with the plating or chromate? What might be possible undercoats? Does an SAE or other spec exist for zinc-nickel? I have come across MacDermid Enviralloy Ni as a possible treatment - can anyone recommend this or a similar process/treatment?
Many questions, but hope you may be able to help.
Thanks very much in advance,
Dan Bird
London UK
Design engineer - London UK
April 20, 2009
Hi Don,
Essentially it shouldn't be difficult. The only problem seems a base metal. It happens high silicon aluminum casts are difficult to plate. It must be treated with a mix of concentrated nitric and fluoride acids. It is necessary to remove silicon from the surface thoroughly, but without over-etching. After successful pretreatment
Macdermid Bondal could be applied as typical undercoat. If the starting over-potential was too high (too much hydrogen in the beginning, but the deposition develops very slow), maybe it would be useful to make Wood nickel strike before Zn-Ni deposit. Good luck.
- WARSAW, POLAND
A little known process for starting electroplating on aluminum involves using an alkaline zinc, or zinc-cobalt, or zinc nickel.Clean the casting with NO ALKALINE ETCHING (as you do not want to decrease aluminum and increase silicon), deox in 50% Nitric Acid with one pound per gallon ammonium bifluoride, place the part in the alkaline zinc-nickel electrolyte (the matrix is a "zincate"). After 45 seconds, then gradually ramp up the current and slowly start plating, then turn up to the recommended current density for hte particular process. If zinc-nickel or zinc-cobalt, the single product version of olive drab chromate comes out jet black.
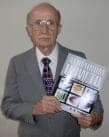
Robert H Probert
Robert H Probert Technical Services

Garner, North Carolina
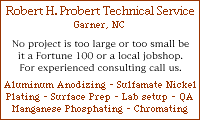
April 20, 2009

Q, A, or Comment on THIS thread -or- Start a NEW Thread