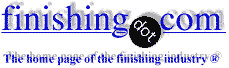
-----
Post Heat Treat of 416 SS to Avoid Surface Corrosion
March 19, 2009
Hello all...
I need to consult with you on this issue...We a Medical Device manufacturer, I have a product that is made out of 416 SS which is Heat Treated to approx. 40 HRc post machining. It is then brought back to the shop for grinding and then it is passivated before it goes to stock. My issue is that I have been developing surface corrosion between the time that I Heat Treat and that I grind and passivate!
How can I avoid this? The HT Vendor suggested oil coating the parts before he send them to me, but I'm concerned about the type of oils used etc...Any suggestions?
Thank you in advance for your help.
Product Designer - Jupiter, FL, (USA)
First you need to make sure that it is really corrosion that is occurring. The sulfides can come to the surface of 416ss when it is exposed to humidity, and look almost identical to rust. If it is sulfides you normally can remove it with NaOH solution.
416 "corrosion resistant iron" is not very corrosion resistant, so until you passivate it you can have some rust. Oil on the surface can help prevent this. You can use vegetable oil or other medically safe oil, but this can also grow bacteria.
Hermetically sealing the parts until you can finish grinding and passivation will help, but this is hard to do. Can you use 410ss instead of 416? This is harder to grind, etc., but will not usually give you the corrosion problem or the sulfur bloom.
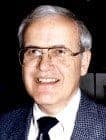

Lee Kremer
Stellar Solutions, Inc.

McHenry, Illinois
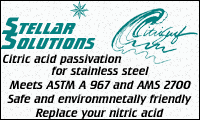
April 15, 2009
Thank you for the reply....
We had the parts tested:
Samples were analyzed by scanning electron microscope (SEM) and Energy dispersive spectroscopy (EDS). The SEM images were consistent with Rust. Also consistent with water drops (possibly salt water?) on the parts. EDS indicated presence of Chlorine, sodium, and excess oxygen.
We think that this was caused by lack of controls at the passivation process, does that make sense?
Thank you in advance for your assistance.
- Florida
April 22, 2009
You might try VPI paper or use of silica gel packets that do not touch the parts. If the parts are small, you might use a plastic box with separators and then use a plastic bag that you can pull a vacuum on. A slight back fill with dry nitrogen will help a lot. Think of those bags that they sell for storage of clothes and bedding to reduce the storage space.
James Watts- Navarre, Florida
April 23, 2009
You say that your SEM and EDS results indicate contact with salt water. So you have simply confirmed that 416 has no particular resistance to salt water. Surely your course of action now should be simply to take steps to prevent the contact with salt water.
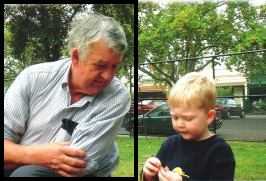
Bill Reynolds [deceased]
consultant metallurgist - Ballarat, Victoria, Australia
We sadly relate the news that Bill passed away on Jan. 29, 2010.
April 24, 2009
Q, A, or Comment on THIS thread -or- Start a NEW Thread