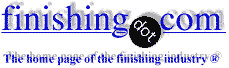
-----
Anodizing thickness is greater at bottom of rack than at top
Q. I work for an anodizing company that does type II and III sulfuric anodizing. We sometimes come across a variation in coating from the top of our racking(less) to the bottom(more). I was wondering what could cause this and if there is a way to avoid it in the future
Chris Jonesanodizing technician - Calgary, Alberta, Canada
March 16, 2009
First of two simultaneous responses --
A. One possibility is that some of the "electricity" is bouncing off the bottom of the tank, so you have a higher current available there. Anodize is only somewhat self leveling. Try shorter cathodes.
James Watts- Navarre, Florida
March 19, 2009
Second of two simultaneous responses --
A. Depending on the air agitation pattern, small bubbles hit at the bottom, larger bubbles wipe the top and displace more solution. If your analog ammeter is flickering - that is the problem. Move the air spargers so that the air moves solution and does not hit the parts.
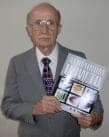
Robert H Probert
Robert H Probert Technical Services

Garner, North Carolina
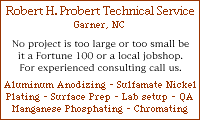
March 19, 2009
A. Chris
I have not seen the phenomena in Type II processing- only in Type III. Variation never exceeded .0002" thickness when comparing top to bottom (36" racks). Anode to cathode ratios did not seem to effect results. We did not play with JW's suggestion of cathode length- ours were 6" off the bottom of a 4' deep tank
- Colorado Springs, Colorado
March 20, 2009
March 24, 2009
A. Hi
Check for uniformity..
1. Is the temperature uniform?
2.Is the air agitation uniform throughout the bath?
3. Are the contact points uniform?
Check for tightly held components.
Check for mixed loads, different shapes/surface area etc...
good luck,
- Chennai, India
A. Dear Chris
There are many reasons for this to happen, some of which have been mentioned. To troubleshoot you need to answer several questions starting with the type and length of the cathode material, the type of rack being used, the temperature uniformity of the bath and isolation of information as to what parts are giving you the problem. Quick guesses on causes only lead to inaccurate responses/solutions.
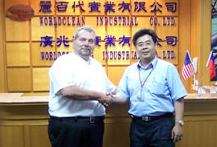
Drew Nosti, CEF
Anodize USA

Ladson, South Carolina
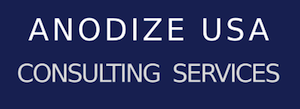
April 25, 2009

Q, A, or Comment on THIS thread -or- Start a NEW Thread