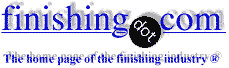
-----
Electropolishing of Aluminum vs Bright-dip
Current question and answers:
Q. Hi there. My question is does anybody currently use electropolishing as a pretreatment to the type 2 anodising process? My competitors are using a bright dipping solution but I'm not interested in doing so because of hazardous fumes generated from such process. The alloys that I would like to electropolish are mainly 5000, 6000 series. Who are the best contacts to help assist me in setting up this process? And also: is pitting a by-product with this process or is it when the chemistry/ parameters are out of specifications? Any help would be much appreciated. Thanks, Rob
Robert benk- Smithfield Australia
April 11, 2021
9th Edition, Vol. 5
"Surface Cleaning, Finishing & Coating"
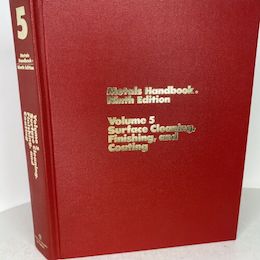
on eBay or Amazon
or AbeBooks
(affil link)
A. Hi Rob. We moved your posting from where you had put it to this thread because of the great answer below from Harry Parkes where he explains why so few shops do electropolishing even when it can be fine for the purpose. You might also wish to see topic 1243 for 2nd and 3rd opinions and discussion of appropriate alloys, and consult ASM Metals Handbook Vol.5, which has great coverage on the interrelationship issues related to alloy composition, bright dipping, electropolishing, and anodizing.
Luck & Regards,
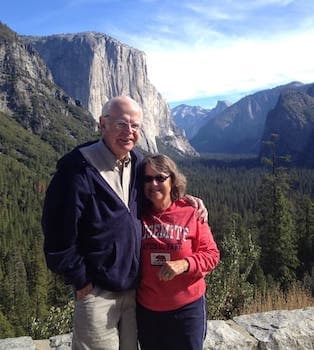
Ted Mooney, P.E. RET
Striving to live Aloha
(Ted can offer longterm or instant help)
finishing.com - Pine Beach, New Jersey
⇩ Related postings, oldest first ⇩
Q. My question is how different for aluminum electropolishing and Bright-dip finish
Which process will bring brighter finish if parts going to be clear anodized after it.
Product designer - Hayward, California
February 26, 2009
March 12, 2009
A. Hi,
I haven't been on this site for a couple of weeks and so didn't see your question until now. Are you still monitoring for replies?
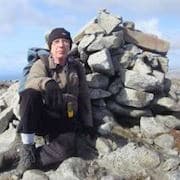
Harry Parkes
- Birmingham, UK
Ed. note: Welcome back Harry! We'll remind Paul that he has a reply, but please note that in addition to this forum running interactively, we're also trying to make it a permanent information resource. Hundreds of people read the postings for each one who posts, so anything you offer will be very helpful to many readers in any event :-)
March 27, 2009
A. Hi,
Comparing good chemical brightening with good electropolishing, electropolishing generally gives a brighter, smoother finish. However on alloys of less than 99.8% purity the loss of brightness with even modest anodic films of 3 µm, the benefit is slight when compared to the loss in brightness due to the anodic film. Even on 99.8-99.85 based alloys (car trim/cosmetic containers) the gain is relatively small. The exception here is when the alloy does not contain the 0.03-0.08% copper added to enhance chemical brightening (on phosphoric acid based baths). The main benefit is on super-pure aluminium (99.99) especially lighting reflectors where maximum reflectivity is required and brightness loss on anodising is small.
The choice of which to use is not simply down to current versus no current. The cost of electropolishing is considerably higher than chemical. This is partly due to higher chemical cost and electrical power. But, of great importance is the amount of work that can be processed and racking requirements.
Dealing with racking first. With chemical brightening the cross sectional area of racks and number of contact points is largely dependent on the anodising current (~ 12 asf).
The current density for electropolishing is 5 to 10 times greater. As heating is proportional to the square of the current the impact on burning at contact points and rack size is significant. The use of aluminium racks rather than titanium help here.
A very important feature of anodising is that the throwing power is exceptionally good. Parts can be tightly packed in a way that would be disastrous if used in electroplating. Current distribution in electropolishing is much closer to that of electroplating. Consequently parts have to be much more widely spaced: this means that the throughput of work is considerably lower than that of a plant of comparable size that is using chemical brightening.
All the electrical power use in electropolishing is dissipated as heat and cooling is needed on all but the most lightly used of plants.
One advantage of electropolishing is that it does not use nitric acid and so the emissions of nitric acid vapor and oxides of nitrogen are avoided. If you operate in a restricted zone consider using the services of a specialist anodiser rather than install uncompetitive plant.
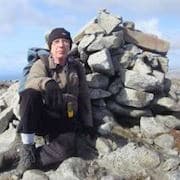
Harry Parkes
- Birmingham, UK
Q. Dear Sir,
I am using 6063 alloy. Can you please tell me which will give me high gloss electro brightening or chemical brightening. I am targeting reflectors for light.
Thanks
- Pune, Maharashtra, India
August 5, 2013
A. Hi,
Ted has attached your email to a reply I gave in 2009. Dealing specifically with extrusions, I suggest that you consider using 6463 alloy which is designed for maximum brightness.
Harry
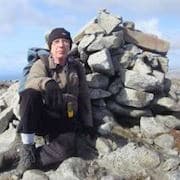
Harry Parkes
- Birmingham, UK
August 11, 2013
August 13, 2013
Dear Mr. Harry,
Thanks a lot for the reply. I will go for 6463 alloy.
Once again thanks for your reply and also a great thanks to Mr. Ted and finishing.com
Regards
- Pune, Maharashtra, India
Specular Gloss Levels
Q. Please could anyone advise what the highest specular gloss level is that can be achieved on a AA6563-T5 extrusion and the steps to follow to achieve this.
Nigel Do- London, UK
January 26, 2014
A. Hi Nigel,
It's been a long time since I measured specular gloss and can't quote a value. Your choice of alloy looks good. This is the procedure I would try:
Mechanically polish the significant surface/s. The aim is to produce a compact, homogeneous layer of aluminium.
Chemically or electrolytically polish the aluminium to remove fine scratches and produce a bright, clean surface.
Anodize for the minimum time needed to get the required corrosion resistance: the anodizing stage will lower the total and specular reflectivity.
Harry
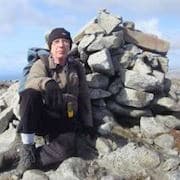
Harry Parkes
- Birmingham, UK
January 30, 2014
Q, A, or Comment on THIS thread -or- Start a NEW Thread