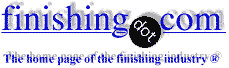
-----
Polishing SS starting with 2B (2D?) finish - initial step
I am a hobbyist. I am polishing flat 1/2" wide 304 stainless stock. When you look closely at the initial piece, there are tiny round pits in the surface (and the surface, at least on one side, is not exactly flat. There are two ridges on the outside that are higher than the middle - by a tiny bit, but enough to cause problems when sanding. It is a huge pain to remove those pits. Right now, the only thing I found that works is Dremel
⇦ on
eBay or
Amazon [affil link] 1/2" sand drums with 30-40 grit sandpaper, high speed, and MULTIPLE passes - very labor-intensive - and even then I miss some of these pits. If I don't remove all those pits, and continue with the finishing passes, in the end I will get my mirror finish, but the little pits will be scattered here and there.
So - is there some reasonably efficient way to do that first pass to remove those pits? They seem to be part of the regular mill finish for stainless, since I ordered the metal from three of different places, and they are present in the bars from all three.
hobbyist - Columbia, Maryland, USA
February 25, 2009
February 26, 2009
You probably are looking at a hot rolled finish.
You could take it to a machine shop and have them mill off about
0.005". You could use the
Dremel
⇦ on
eBay or
Amazon [affil link] with a coarser grit and a slower speed to remove the bulk of the pitted layer and then resume the regular grits. Notice, for the coarser grit work, most grinding shops would use cutting fluid which could be soapy water.
- Navarre, Florida
Yes, I presume it is hot-rolled. I think all bar stock is. Does anyone know if there is a way to get bars 1/2"x1/8" that are cold rolled?
Mike Medved- Columbia, Maryland, USA
February 28, 2009
I believe than any major steel supply house will have cold finished steel in this size.
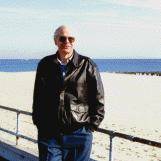
Ted Mooney, P.E.
Striving to live Aloha
(Ted is available for instant or longterm help)
finishing.com - Pine Beach, New Jersey
March 4, 2009
I'm having the same problem, I've been looking into e-polishing these. Have not found a system yet.
Shawn Michaels- Kingman, Arizona, U.S.A.
April 3, 2009
Electropolishing works better on rough surfaces, not pits. Have one part done commercially to see if you get suitable results. My guess is no, unless it is grit blasted with progressively finer grit and then electropolished. I could be very wrong as my experience is limited to 400 series SS.
James Watts- Navarre, Florida
April 6, 2009
April 9, 2009
You need to start with a belt sander and a course enough grit to get rid of surface scale and roughness. You will have to grind it until all you see are the belt lines from the belt you are using. If you leave something in it and figure you can get it out with your next step down grit you will fail. If you have not had experience in this type of work it is going to be difficult in spotting imperfections in your course grit passes.
Lets say you start with an 80 grit belt. You must grind until all you see are 80 grit lines. You will most likely have to make your passes at about a 30 degree angle from the longitude of the part and then straighten them out to the longitude of the part before you step down to your next grit belt. I would step down to a 120 grit and cross them at about 30 degrees (Some people suggest 90 degrees, I find that this causes waffling in the metal) then straighten the line out . Make sure that you get all of the 80 grit marks out, keeping an eye out for the surface imperfection you saw in the original surface. If you have left any of them in , you will have to go back to the 80 grit and work some more. The next belt will be a 220 grit doing it the same way as the previous belts. As you use the finer grits you will be able to see any surface flaws you may have missed earlier. If you see any you must go back to the 80 grit and start all over. Once you are sure that you have a pure 220 grit finish you will use a 320 belt in the same manner as the previous belts. Once are sure you have a pure 320 grit finish you will be ready for a tight sown sisal buff. You will use a stainless steel polishing compound on this buff. Start with you 30 degree cut, make sure you put compound on the buff after every pass. Once you have buffed out all the 320 grit marks straighten your buffing lines out as before. Now you will use a big tightly sown cotton buff with a white chrome buffing compound. Cutting 30 degrees and finishing with a straight cut. During each grinding and buffing process the part is going to get very hot. You will need thick welding gloves when doing this job.
It is very important to get out the previous grinding marks before you step down to the finer grit. You won't be able to make up for it with an even finer grit.
It is a lot of work, but it is the only way to do it properly.
- St. Louis, Missouri, USA
Q, A, or Comment on THIS thread -or- Start a NEW Thread