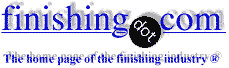
-----
Flash rust after drying in oven
February 17, 2009
I have a small metal cabinet manufacturing company in which we are having flash rust appearing on our cold rolled sheet steel after we dry it off in our ovens.
We are using a four stage dip tank system. First stage is kept at 140 deg. using a high alkaline degreaser--2nd stage is fresh water rinse with constant overflow--3rd stage is an iron phosphate at 3-4 oz per gallon of water--immersed for approx. 3-5 minutes. Our tanks are 300 gal capacity.
Fourth stage is room temp. tap water rinse with constant overflow.
The dip tanks are approx. 60 years old made of 1/2" steel plates. They are very heavily coated w/ paint, etc..... on the outside and they do have a coating of "something" on the inside of the tanks that cannot be scraped off--I have been told that the quality of these tanks may be the problem. Now we have to rub or wipe all parts down after they come out of the oven to remove the flash rust--very time consuming, Any help?
plant mgr. - Kansas City, Missouri
![]() |
Talk to your phosphate vendor. They should sell a rust inhibitor for your final rinse tank that will solve your problem. It will also dry quicker if you use about 5% to 10% commercial isopropyl alcohol ⇦ on eBay or Amazon [affil link] (IPA) in the final rinse in your waste water system can stand the change in BOD/COD. It is not a fire haz at this strength! Also look into using an air knife to knock off the bulk of the water as soon as it comes out of the last tank. High pressure air works well, but OSHA will have a cow. Get it into the oven quicker will also help. James Watts- Navarre, Florida Gregg, in general, you may deal with two types of rusts without detail information. 1) if the drying temperature is higher behind 350 °F, you may see the yellowish head rust on CRS. 2) if your phosphate tank was not operated properly, you may see induced flash rust by phosphating chemical, which could be seen anywhere from right out of bath to initial oven dry due to moisture level. - Cincinnati, Ohio This is a common problem. - Pittsburgh, Pennsylvania Is this a new problem? It looks like your Phosphate concentration is too high and your immersion is too long. Try 2.0 to 2.5 and about a minute to a minute and a half, keep the pH at about 5.5 to 6.0 range and see if that helps. You didn't say whether or not the phosphate stage is heated, if it is keep the temp under 110 degrees. The ppm of the final rinse should be as low as possible, in the less than 50 range. I doubt the condition of the tanks is a factor unless they are rusting on the inside. ![]() Sheldon Taylor supply chain electronics Wake Forest, North Carolina Hi Gregg, - Naperville, Illinois |
March 4, 2009
Sir:
I have zero experience in phosphating. However I have done many rinsing experiments. My experience is that the steel product must not be allowed to dry between rinsings and a pH lower than 5 prevents rusting. Also the hotter the steel the faster it rusts.
Regards,
Galvanizing Consultant - Hot Springs, South Dakota, USA
March 5, 2009
Sir:
In my previous response I left out two things. (1) Not only does a pH below 5 prevent rusting of pickled steel, but also a pH above about 8 also prevents rusting. (2) A certain surfactant at between 1 part and 3 parts per 10,000 prevents rusting of pickled steel.
Regards,
Galvanizing Consultant - Hot Springs, South Dakota, USA
what temperature need for drying phosphate in oven?
Verya Rezaei- Bandar Abbas, Iran
May 21, 2011
Hi, Verya
Is this a question for Gregg, to which you need the answer in order to help him? Or do you have a problem of your own with flash rusting of a phosphate coating on your parts? Or are you misunderstanding this thread, thinking that we are talking about the preparation of phosphate-based bulk supplies? Please spend at least several sentences describing your situation. Thanks.
Regards,
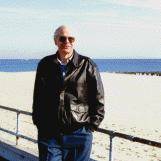
Ted Mooney, P.E.
Striving to live Aloha
(Ted can offer longterm or instant help)
finishing.com - Pine Beach, New Jersey
May 22, 2011
Q, A, or Comment on THIS thread -or- Start a NEW Thread