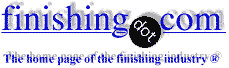
-----
Turning copper sulphate into copper and sulfuric acid
hi. we currently use sulfuric acid and oxygen to move copper plating into solution off ceramic material.. then dehydrate the spent solution for disposal and send off salts. I was wondering if there could be a way to recycle the solution by just plating out the salts and convert the solution back to an acid again. could just use a copper or steel plate to get the metal out, but the anode is the question. Any metal anode plate I could think of would most likely convert the solution to that salt right. But I want hydrogen.. voltage has to be low and amps high for plating, what about raising the voltage enough to actually spark into the solution with the cathode at the bottom of the solution? I have been looking for this answer over a year.. thanks
James Dinsdaleprototyping - Alamogordo, NM, USA
February 12, 2009
Electrolytic recovery of copper from sulfuric acid is fairly easy. It is most often done with Iridium Oxide coated Titanium anodes. While expensive, these anodes are stable and can last for years. At the anode, oxygen gas and H+ ions are generated. At the cathode, copper is plated out, and if done correctly, only a little hydrogen gas and OH- ions are created.
In order to plate the copper down to a low concentration, it's necessary to use a high surface area cathode. There are several suppliers with standard product offerings.
LK
consultant - Cleveland Heights, Ohio
February 16, 2009
Thanks for the response, I came across a platinum coated titanium anode.. so far it it seems to have no wear. do you think these type would have the same wear results as iridium coated? what about just lead anodes? would they wear since there will be oxides in the solution?
using a low voltage 2.3 v and getting out copper to plate to a copper plate.. if I decrease the voltage to 1.6 v, I get some black powder could that be silver residue from some silver removal. or could it just be an oxide of copper. we have traces of nickel and iron in the solution, hoping to be able to plate it out with the copper too or it would theoretically build up making the solution inactive..
- Alamogordo, New Mexico
March 1, 2009
Q, A, or Comment on THIS thread -or- Start a NEW Thread