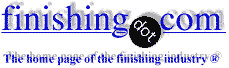
-----
Conductivity of bare Aluminum vs. Chemical Conversion Coating
Our Engineering group thinks it's necessary to chemical convert (chromate) Al 6061-T6 prior to anodizing machined parts in order to have uniform electrical grounding over the life of the product. So typically, they chemical convert the part and then mask any blind threaded holes that may provide grounding paths. I say they are wasting money and bare Al will provide a hundreds of years good electrical grounding since the instruments are used in clean room environment or pharma applications. Your thoughts?
Brad [last name deleted for privacy by Editor]Operations - Boulder, Colorado, USA
February 11, 2009
![]() |
Either of you may be correct. The prints may call for electrical connection points to be chem-filmed where the bolt head contacts the part. Past practice can have the effect of a contract unless the contract specifies otherwise. - Navarre, Florida February 12, 2009 I would agree that the only reason to chromate the contact area is corrosion resistance. Leo Herringon consultant - Grand Rapids, Michigan, USFebruary 12, 2009 February 12, 2009 Brad - Colorado Springs, Colorado |
February 18, 2009
Thanks for the responses. Let me clarify a little.
I understand the need for chromating between bare Al surfaces especially if the parts are conducting electricity. This is for bare Al in pure contact with another Al surface. What if hardware (male threads to female threads) is used between the parts for the electrical connection?
We are using the contact for grounding purposes only. Also, the bolt head is not providing the ground since the mating part is anodized. The threads of the bolt are proving the grounding path. Since, we are using Type III chromate (Type III is a thin layer) I argue that the SS bolt is removing most of the chromate in the thread so why bother chromating. I doubt that an oxide layer could build up between the SS bolt threads and the female blind threads.
Thoughts?
Operations - Boulder, Colorado, USA
Q, A, or Comment on THIS thread -or- Start a NEW Thread