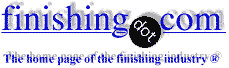
-----
Plating on Plastic was cracked
Dear all,
We plating ABS with 20 microns of Copper, 6 microns of semi-brightNi,7 microns of Bright Ni, 0.20 microns of Cr coating. After 16 hours of CASS test the plating becomes crack or store about once month the plating was corroded and cracked
Could you please give me yours ideas
Thanks and Best regards
HOP
PLATING SUPERVISOR - VIETNAM
February 7, 2009
February 11, 2009
Vo,
The bright nickel deposit contains more stress than the semi-bright, especially at the thickness of 7 microns. When you say semi-bright Ni I take that to be a sulphamate bath?
Your best bet is to monitor and or add stress reducer to the bright Ni bath. Another option would be to lay down more semi-bright Ni than bright Ni. Because the Cr finish thickness is rather low, I don't suspect the problem lies with that finish. Hope this helps you.
Fellow Plater - Syracuse, N.Y.
Just an after thought..... You could back strip the chrome on the rejected parts to make sure the cracking is on the Ni surface. I think you will find that it is.
Mark BakerFellow Plater - Syracuse, N.Y.
February 11, 2009
March 26, 2009
Hi Ms.Hop,
I think the problem of the crack lies at the Bright Nickel layer. Normally Bright Nickel layer will give the brightness while balancing on ductility. Often there is organic contamination that will co-deposit with the Ni and causing the ductility to be worse.
As suggested by a previous post, I think using higher SB Ni will help.
Good luck!
- Singapore
Q, A, or Comment on THIS thread -or- Start a NEW Thread