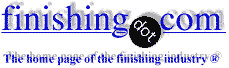
-----
Sandblast/shotblast/beadblast Hardened Steel & Aluminum
Q. I'm the newly appointed coating line engineer for my company, and I'm taking on some process issues that have been with us for a good decade or more. I'm sure someone else has solved the problem before, and I hope he or she visits this site.
In order to prepare parts for manganese phosphate coating, we clean and roughen the surface by blast abrasion. We often find it challenging to achieve necessary coating weights on our heat-treated 4140 steel parts, and we believe the reason to be that it is more difficult to abrade the surface adequately. We use steel shot in an airless tumbler blaster. Can anyone suggest a better media, equipment, and/or procedure combination for increasing the abrasion we achieve on our hardened steels? Thank you.
Plating Engineer - Grand Junction, Colorado
February 4, 2009
A. I will find a number of people that will disagree with this statement, but steel shot tends to peen the surface rather than expose new surface. The higher energy shot blast systems will do a better job of cleaning and exposing fresh iron (steel) than your tumbler will.
There are a number of abrasives that will work in most tumblers, some need it to be wet, but many will work dry and do a better prep job than shot.
We used a pressure blast cabinet with aluminum oxide grit and had good speed and active metal. Coating weight was never a problem, even hard 4340.
- Navarre, Florida
A. Michael, James is correct in that shot will peen the surface. I'd like to know more information. Does the tumbleblast have an abrasive wheel throwing the media at the parts? How hard, Rc, are the hardened 4140 parts being blasted? Either way, a good method to achieve coating weight profile is to use a mix of media (shot + grit). Also, the media should be harder than the parts. Another type of media which works well is "as cut", carbon cut wire shot. The advantage of cut wire shot is higher hardness, extended media life and ability to just add "as cut", carbon cut wire media to the working mix to maintain consistent performance. Hope this helps
Tim DeakinNorth Tonawanda, New York
A. Jim has a good point in his answer; however, I'd like to know what happens to this part after prep. Is it painted? If so what kind of a coating?

AF Kenton
retired business owner - Hatboro, Pennsylvania
Q. Thank you all for your responses. In answer to the requests for clarification, we are coating 4140 steel in the HRC 47 - 52 range. After coating with manganese phosphate, we immerse the parts in oil. This is for a military application.
I tried using SiC in an air blaster, and got puzzling results. At 5 minutes blast time, we had pretty good coating, but the part surface didn't look to be phased. But blasting for 20, 40, and 60 minutes led to a drop off in coating weight of almost 20%. Under the microscope, it looked like we were polishing rather than rouging up the surface, but we were using a coarse (46 grit) SiC.
We observed the opposite trend with the steel shot blaster--the longer we blasted, the more coating weight increased. Any idea what's happening?
- Grand Junction, Colorado
February 16, 2009
A. Your 46 grit SiC is a good material with decent use life. AlO3 (white) would lose half of its grit size on each pass thru the blast cabinet. Therefore, it did not cut as fast as time passed, and as you say, it looked more polished as the grit lost size and bulk. It fractured fairly well, but 200 or 400 grit size does not cut fast. It does remove the scale, but much slower than fresh 46 grit. Notice on my original post that we used a pressure cabinet, not a siphon cabinet, which operates several times faster. This meant that we added fresh grit about every hour or two and changed it out daily when we were doing heavy blasting all day.
I personally think that 46 grit is a bit rough for most parts.
With your long run time, I think that you were actually embedding the heat treat scale back into the part. That is a thought, but at a minimum, the heat scale will not perform as well as the SiC and will rapidly have a small size which will slow down your rate of cut until it gets small enough to go to the dust collector.
You might want to try the cut wire. If it will work, it will probably be cheaper in the long run, but will not have an indefinite life by any means.
Gee, isn't having a metal finishing shop fun? Always problems to be solved.
- Navarre, Florida
I agree with Jim W that maybe you should go to a different grit size and replace more frequently. You might want to also tilt your part or gun a little more. I'm also concerned with the use of oil after processing; however, if that is spec. stay with it.

AF Kenton
retired business owner - Hatboro, Pennsylvania
A. Mr Kenton,
He is using oil AFTER phosphate, not after blasting.
Jim
- Navarre, Florida
February 25, 2009
Blast Aluminum and Steel in the same system with spherical iron S230 shot
Q. We produce aluminum light poles and clean in a continuous blast system with S230 cast iron shot. We have a good dust collection system that is well maintained. We have a need to run some mild steel poles through the system as well.
Do you foresee any hazards? Down stream operations are powder coat and wrap. All fabrication and welding is performed previous to blasting.
Fabricator - Light Poles - Abingdon Virginia USA
February 23, 2011
A. Hi Greg,
This may be a little over the top, but certainly in the aerospace industry we try to avoid blasting ferrous and non-ferrous materials in the same cabinet.
If you blast your mild steel the hazard you will have will be the possibility of imbedding steel particles into the aluminum poles that you blast later.
Personally, after blasting the mild steel poles I would then change the media and get the cabinet cleaned to ensure the steel has been removed from the cabinet. Well, that's what I'd do anyway.
Aerospace - Yeovil, Somerset, UK
Q, A, or Comment on THIS thread -or- Start a NEW Thread