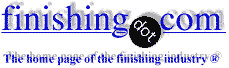
-----
Alodine, Iridite, Chem-film not sticking / rubbing off

Quickstart:
Aluminum is often 'chromate conversion coated' as a corrosion resistant final finish or as a pretreatment for painting or powder coating. The process actually involves many steps, usually including alkaline cleaning, etching, deox/desmut, the chromate conversion step per se, and water rinses between each step.
MIL-C-5541 / MIL-DTL-5541 / MIL PRF-5541 is the most commonly cited spec. "Alodine" and "Iridite" are proprietary trade names from two suppliers of the process chemistry. "Chem film" is a slang term for the process often used in the USA.
Q. We have issues with 3 mm diameter threaded blind holes that are around 6 mm deep that are not getting coated (Alocrom 1200) throughout the depth (Average coated depth about half the depth) usual process:
1) acetone
⇦ on
eBay
or
Amazon
[affil links] Warning! Flammable!
clean and dry.
2) Alkaline immersion (10 min)
3) Water immerse (6 min)
4) Deox immersion (10 min)
5) Water immerse (3 min)
6) Alocrom 1200 immersion (3 min)
7) Water immerse (2 min)
8) Water immerse (2 min)
The only issues are the blind holes?
Regards,
Brandon
Employee - Stalybridge, Manchester, England
June 7, 2022
A. Hi Brandon. The only thing you can do with blind holes that is compatible with simple high production is to rack them with the opening between dead horizontal and very very slightly upward. If air can't get out, process solutions can't get in. But if a process solution can't drain out, the next one won't get in, and 3 mm dia x 6 mm deep sounds like a major problem.
Your best option may be to promise a clean but not chem-filmed blind thread. Realistically, corrosion in the bottom of the hole is probably not an issue, whereas corrosion near the top is probably a major issue despite the chem-film. Having had to grind an aluminum hose nozzle off of a garden hose with brass fittings just yesterday, I'm tending to think practically, rather than about how a component that was not designed with finishing in mind can comply with a spec that may not be realistic either :-)
Luck & Regards,
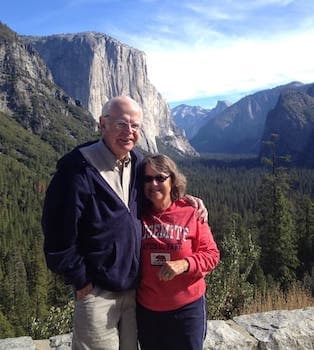
Ted Mooney, P.E. RET
Striving to live Aloha
finishing.com - Pine Beach, New Jersey
Thank you.
- Stalybridge, Manchester, England
June 8, 2022
A. First, go up/down/in/out, completely in/out several times in the cleaner, you must get the tenacious cutting oil out of the bottom threads, whatever ever it takes. Maybe soaking in solvent before racking.
Then, right on down the line, in every rinse, every chemical, and especially the chromate, go completely in/out to keep flushing the deep bottom of the threads.
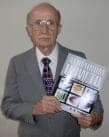
Robert H Probert
Robert H Probert Technical Services

Garner, North Carolina
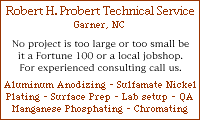
Thank you.
- Stalybridge, Manchester, England
June 9, 2022
Q. We're experiencing the same problem with our 6061 aluminum cans. The "rub-off" is mostly around the edges and holes. We tested a can prior to cutting various sized holes and deburr, the chem film did not rub off. We also tested other parts with no problem.
Malay S. Mooreshop employee - Salt Lake City, Utah
February 7, 2025
? Hi Malay.
What technology are you using to put those holes in the cans?
Luck & Regards,
Ted Mooney, P.E. RET
Striving to live Aloha
finishing.com - Pine Beach, New Jersey
Q. We're using HAAS automation system to mill this particular job. We tried it with fresh new coolant, with RO water, and without any cooling system. The Rub-off persists in all testing conditions. The worst rub-off occurs in the test sample with no coolant. All tested units showed rub-off wear mostly on the outer surfaces. Only compressed air was used on all test specimens.
Chemist - Salt lake City Utah
February 11, 2025
A. Hi again,
Your answer seems to imply that the machining of the holes is neither changing the metallurgy in any way, not leaving any sort of contaminant on the surface; the conclusion being that the mere presence of holes, is effecting the cleaning, chromating, or curing of the parts in some way.
Is there a possibility that the presence of holes is allowing the part to heat up too much or two fast, especially near the holes? Can you tell us anything about the drying/curing procedure?
Luck & Regards,
Ted Mooney, P.E. RET
Striving to live Aloha
finishing.com - Pine Beach, New Jersey
Q. Test sample was rinsed in ambient water prior to hot rinse as the final step then blow dry. Curing time was not even considered. We tested the trouble areas shortly after chem film.
Malay S. Moore [returning]Chemist - Salt Lake City Utah
February 12, 2025
⇩ Related postings, oldest first ⇩
for Shops, Specifiers & Engineers
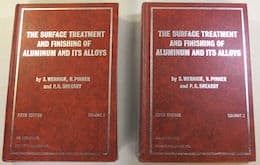
avail from eBay, AbeBooks, or Amazon
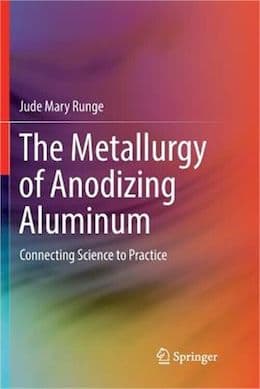
avail from eBay, AbeBooks, or Amazon
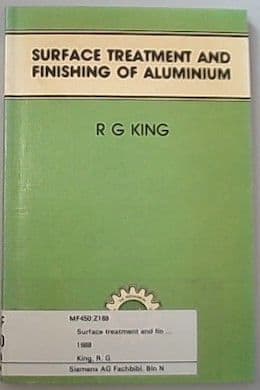
avail from eBay, AbeBooks, or Amazon
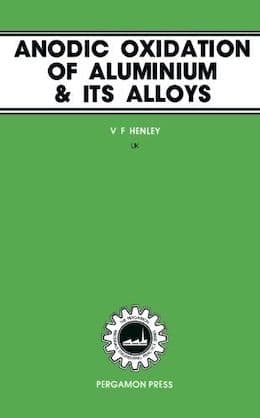
avail from eBay, AbeBooks, or Amazon
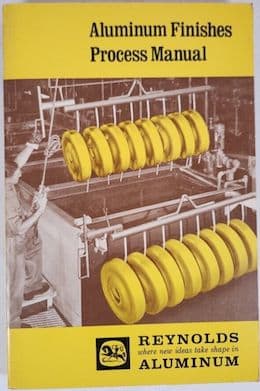
avail from eBay, AbeBooks or Amazon
(as an Amazon Associate & eBay Partner, we earn from qualifying purchases)
Q. Greetings to all! I'd like some advice regarding chem-film finishes for die-cast aluminum parts. Our company's products often use small aluminum housings that are machined from 6061-T6 alloy and chem-filmed per MIL-C-5541. We're now investigating the feasibility of producing some of these parts via die casting.
Recently we received some sample parts that were die cast from alloy A380 aluminum and were chem filmed per MIL-C-5541, Class 1A. Unlike the machined parts (which have colors that are uniform and range from pale to golden yellow), some of the cast parts possess a mottled green appearance that can be easily rubbed off. This is unacceptable.
Also a few other samples I received have a brownish color, and I noticed that heating them to about 125-150 °F causes their color to darken to a deep bronze. The texture of the finish also becomes flatter, almost chalky.
Some individuals have indicated that this result is typical of chem-filmed die cast aluminum parts, especially when using the A360 or A380 alloys. However, I'd like to hear additional, detailed opinions on this topic.
Also, if the chem-film finish is inadequate for this application, what is an economical alternative? Keep in mind that the electrical conductivity that the chem-film finish offers is a very desirable feature.
- Whippany, New Jersey, USA
2000
A. 360 and 380 both have about 9% silicon in the alloy which makes life quite difficult vs 6061. It will require an acidic deox/desmut that contains a goodly amount of fluoride. Tri acid-sulfuric/nitric/HF being a common one that is extremely strong. If that is the only alloy being run in that chem-film tank, then it could be tweaked with the help of the vendor for optimum performance on the cast alloy. Color changes, minor ones,are moderately common. It should not have major ones and certainly should not be chalky or rub off.
140 °F is the maximum that a chromate coating should be heated to , in most cases.Alternatives would be return to the wrought alloy, change the casting alloy to one that was more amenable and find better vendors for the casting and chem-film. You might have to bring the chem-film "in house" . This may cause more problems than it solves. There may be vapor deposition processes that would give satisfactory tradeoffs, but The price would very probably be higher.
It is worth looking into from some of the folks that advertise here.
- Navarre, Florida
A. Hi Keith,
You're pretty much right on the button with your thoughts and what others have been telling you. Die casted chromated parts are nowhere near as uniform as a machined finish because of the porous structure of the casting, you can limit this by polishing down the casting to a smooth surface, but you eliminate the cost savings of going with a casted instead of a machined surface by doing this.
The finish probably appeared rather patchy in areas, but as far as rubbing off, it shouldn't do that no matter what class of chromate you use Class 1/3 whatever. It won't last as long corrosion wise on the casting material as it will on a machined surface. I want to say off the top of my head that 336 is of course the machined surface salt spray requirement in hours and casting material (dependent on the type, I think 380 is the called out material in the ASTM spec) its around 58 hours or something incredibly low like that. Which in my opinion is proof enough to signify the difference! s, the governing bodies already
realized and noted that you will not have good salt spray resistance, and if not mistaken, your electrical requirements also drop down as far as the conductivity goes in regards to the casting material. Are there other options along these lines, maybe, but I don't know of one myself. Good Luck to you, if you have any further questions, feel free to let them fly, I don't have an reference material in front of me to consult and all of this is coming off the top of my head so it might not be 100% accurate, but it does give you a solid A to B starting point to acknowledge.
- Toledo, Ohio
Multiple threads merged: please forgive chronology errors and repetition 🙂
Alocrom 1200 finish coming off
Q. We have a customer who is experiencing problems with an Alocrom 1200 finish [Chromate conversion coating]. Please could you tell me if the colour should be coming off in:
a) General transportation in cardboard boxes.
b) When rubbed lightly with your finger or a damp cloth.
I have spoken to a couple of our metalwork suppliers who give conflicting answers.
i.e., Once the process has been sealed properly no colour should come off & another who says yes the colour does come off, be very careful what you clean it with.
We have been using this finish for over 12 years & never had a problem before.
If you need to clean the metal after handling it in a production environment, what should be used? Have been told white spirit is ok?
Would very much appreciate your help.
- Peterborough, Cambridgeshire, UK
2005
A. Rubbing lightly with a damp cloth - should not remove the coating.
Shipping in cardboard boxes. In humid conditions the sulfur in the brown cardboard will slowly degrade the chromate but that is unlikely your main problem.
If the applicator puts the coating on too fast, it will wipe off. Temperature, concentration, and pH affect the speed of the gel formation. 99/100 of the time, the applicator does not measure pH properly in that low range, his pH is too low, the coating forms too fast, the coating wipes off. If he would throw away the pH meter probe which is probably eaten up by the fluoride in the chromate, then dip out a 5 gallon bucket and raise the pH in increments of 0.3 pH with ammonium hydroxide until the coating forms over a period of 1.8 minutes, then it will not wipe off.
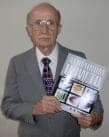
Robert H Probert
Robert H Probert Technical Services

Garner, North Carolina
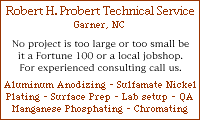
A. Years ago we ran into the exact same problem with one of the major vendors in the USA. Possibly the same one. We chased the problem for days and did testing in the lab and could not get a suitable coating in optimal conditions. When we bitched long enough, they replaced the can with another from the same lot. This failed also. They checked with the retained QC sample and agreed that there was a problem and promised to send a can from a different lot #. The same lot # showed a few days later. They only had 4 cans in stock and were all from the same lot#. The problem material just did not look the same, like it was not properly milled or properly mixed. Solution, we switched to Iridite and had no problems. Sometimes the problem is not in your shop.
James Watts- Navarre, Florida
![]() |
Q. Did you ever manage to find the root cause of this? I am also battling this issue currently. Scott Merritt- Fort Walton Beach, Florida, USA July 30, 2013 A. Hi Scott. Alistair actually posted long ago and checks in rarely if at all. But hexavalent chromate was the usual finish in 2005, and trivalent is more common these days, so please feel free to offer some info about your situation and ask the readers for updated opinions. Thanks! Good luck. Regards, ![]() Ted Mooney, P.E. Striving to live Aloha finishing.com - Pine Beach, New Jersey
- Fort Walton Beach, Florida, USA |
Multiple threads merged: please forgive chronology errors and repetition 🙂
Is it common for Iridite not to stick to aluminum?
Q. Have a situation where we are able to physically rub off the coating created from the Iridite process.
R. CarneyEngineer - Pataskala, Ohio
February 8, 2008
![]() |
A. Time out -- It is time for definition of terms. - Navarre, Florida A. Assuming you solution is not contaminated, and that you have a workable surface preparation cycle, then "rub-off" happens when the coating forms too fast. The coating forms too fast with (1) too low pH, (2) too high concentration, (3) too high temperature. so dip some out in a bucket, raise the pH in 0.2 increments with ammonium hydroxide (NOT CAUSTIC) until you slow it down enough that, after curing 24 hours, it will not rub off. ![]() Robert H Probert Robert H Probert Technical Services ![]() Garner, North Carolina ![]() |
Multiple threads merged: please forgive chronology errors and repetition 🙂
Q. I've just finished the manufacturing of some aluminum (7075-T6) pieces that needed to receive the Alodine 1200 but it is not fixing on the pieces. Is there anything that can avoid the Alodine to fix the aluminum (or this kind of). I've already worked with 7075 previously and it has worked, but not this time.
Pedro AlmeidaEngineer - São Jos ã DOS CAMPOS, São Paulo, Brazil
March 10, 2011
? Tell us about the cleaning and especially the deoxidizer (concentration, chemicals, age, etc.)
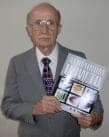
Robert H Probert
Robert H Probert Technical Services

Garner, North Carolina
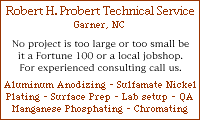
A. Hi Pedro,
You need to give us more details about your process before we can advise you. Can you tell us what your operating parameters are for the precleaning, etching and Alodine processes?
My initial reaction is that the pre-cleaning and etching has not been effective and that is causing your adhesion problems.
Aerospace - Yeovil, Somerset, UK
A. Important are the conditions of the chromating bath.
Too low pH, too high fluorides, too high CrVI content and a too long treatment time can all cause powdery, badly adhering chromate coatings.
chemicals - Heijningen, Zuid Holland, The Netherlands
Aluminum chem film problem parts
Q. HELLO,
We are having a problem getting chem film to stick to some parts. Material 7075-T651.
Small parts that our customer machines and tumbles and then rinses the cleaner off. We have tried all different variations on our tanks. Different times, you name it we have tried. They end up looking blotchy and when you rub on the part the chem film comes off.
Something is blocking the process.
Our line consist of a cleaner, mild oxidizer/etch and chem film. At this point I do not know what to do.
I suggested to the customer that perhaps their cleaner is not being washed off properly, but we are running them through an aluminum cleaner @ 160 °F.
Any suggestion would be welcomed.
- Rincon, Georgia USA
May 3, 2015
A. Have you tried running it without an etch? Some parts tend to not take chem film if it has been etched prior hand.
Daniel Harris- Fort Walton Beach, Florida
A. "tumbles" <= there is the magic word. I suspect the tumble media has been used on iron parts and is embedding fine iron particles into the soft "Kleenex-like" aluminum. Go back and tell them that the tumble media must be designated "aluminum only". While waiting for new media, try a heavier etch to remove and dislodge the embedded iron particles.
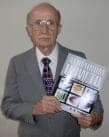
Robert H Probert
Robert H Probert Technical Services

Garner, North Carolina
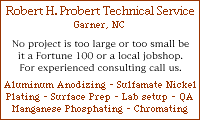
A. Micheline
Adding on to Robert's suggestions, see if you can get a part that has not been tumbled and see how it processes. Baring that, take a tumbled part and mechanically clean it with scotchbrite, then process. If you still have problems, alter your rack material. Some heavily alloyed materials react unfavorably on certain (rack) materials.
I would avoid etching, but rather go longer in your (de)oxidizer. Some soaps/cleaner will leave a residue after drying that cause problems.
- Colorado Springs, Colorado
Q. We have some Al7075 parts Alodined by a company. When I rubbed my finger firmly on the Alodined surface, I noticed that the coating was removed from the surface. Is this normal? If this is abnormal, what is the reason behind it?
H Sharifi- Tehran, Iran
December 25, 2018
A. Hi Mr Sharifi,
To your question, 'is this normal?'- yes and no. Yes, in that it is not uncommon to see, but no, in that it's not supposed to come off significantly. Alodine needs some time to cure after processing, a couple days is plenty, before you start handling it normally. If by 'the coating comes off the surface' you mean a white cotton glove shows some slight discoloration, I wouldn't worry too much. If the surface is becoming visibly less golden where you rubbed, the possibility and severity of an issue are far greater.
Having seen this issue in the course of doing a LOT of chromate on 7xxx, I can tell you some things that could cause the coating to rub off more easily:
-That alloy isn't ever going to chromate as reliably as 6061. The best possibility for a good coating is going to depend on the pre-cleaning they are doing. They need to be sure their soap doesn't have a bunch of greasy contamination. And regardless as to whether or not they etch (under normal circumstances, they wouldn't for regular chromate, unless you're requiring a mask and anodize step too), it is IMPERATIVE that the deox/desmut tank be working well. That means good sparging, fresh solution, adequate acid and redox potential, some process in place to ensure that silicon is never allowed to build up past 30ppm in the tank. Deox results should be confirmed with a white cotton glove or lab wipe before going to chromate- parts coming out of that tank should never be smudgy, and the glove must be squeaky clean. If not, put the parts back in. Failure to fully desmut WILL result in a poor, powdery finish that doesn't protect as it should.
Obviously running the alodine tank to manufacturer's specs is important- but 90%+ of times I've seen troubles with chromate, it's the deox step to blame.
That being said... We've done a decent amount of destructive testing at our shop and troubleshooting trying to pin down the point of failure vs aesthetics, and parts that APPEARED to have coating rub off and become lighter actually passed 168 hour salt spray in one case!
I guess I would approach this like, 1) is it a functional or aesthetic problem; do these parts pass destructive testing? If aesthetics matter as well, is that clearly stated on your PO? I say this because most shops process to spec, which is a functional spec, and allows for some pretty serious variation in color. You MAY have a functional coating even after rubbing the surface residue off- so you need to ask if that is enough, and if you can test that and prove that it is. 2) is there a way you can confirm tank maintenance and processing best practices with your vendor?
All that being said, you definitely need to address this issue with your vendor and make sure they are giving you the coating you are paying for, whether you care about appearance, performance, or both- Good luck!
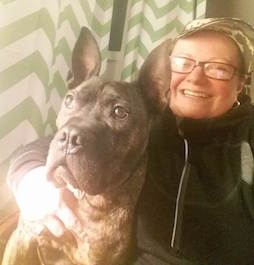
Rachel Mackintosh
lab rat - Greenfield, Vermont
Iridite rubbing off
Q. I have multiple 6061 Aluminum parts that get Iridited at a plater. When the parts come back they look fine, however on some of the parts the iridite comes off right when you rub them. It is even more evident when they come back from the welder and get tested. (And yes, we know that Iridited parts shouldn't be exposed to >140 °F).
If the parts are being handled the same way pre and post iridite, what could be the reason behind the iridite rubbing off on only a few of the parts? Does the Iridite color rubbing off mean that the corrosion resistant coating has been rubbed off?
Aulla Hamdeh- Springfield Township, New Jersey, USA
March 5, 2019
A. It should not "rub" off. Non-adherence can be dues to: (1) pH too low, (2) concentration too high, (3) temperature to low OR too high, (4) surface preparation inadequate,(5) floating soil and other contamination, (6) not "cured" for 24 hours before wrapping in a dry low humidity environment, and other reasons.
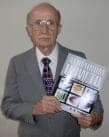
Robert H Probert
Robert H Probert Technical Services

Garner, North Carolina
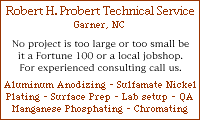
Q. Hello all, we are an aerospace and defense machine shop. We are having issue with a plater and their chem film process. I've had to return multiple jobs due to the chem film rubbing off. Either with your finger or by using Q-tips
⇦ on
eBay or
Amazon [affil links] . No solvents, alcohol, acetone. Just a dry q-tip. I've provided video to them and I'm told that I'm rubbing too hard. That the "gel will be removed if I rub the q-tip too hard". My customer will not accept these parts in this condition. I've been issued a SCAR because of this. Because of that we are extra cautious and check all parts. This company has submitted their response to us and we in turn submitted it to our customer which was approved. However we're seeing it again. This tells me they did not reach the root cause.
We tumble parts, buff them with scotch brite, some parts we don't touch at all after machining. We've seen the issue across the board with them. I have other parts from them that the chem film does not come off no matter how aggressively we use the q-tip.
Aside from finding another plater does anyone have any ideas as to why this is occurring? I'd like to have some thoughts if we see this again in the future. Thank you everyone so much.
- Odessa, Florida
September 15, 2021
A. Hi Bobby. We appended your inquiry to a thread which already covers the issue quite well and offers some ideas that I found insightful. The only additional possible cause of poor adhesion that I can add is drying at too high a temperature. This usually causes the chromate coating to get flake-y, so you would probably notice gold colored dustiness in the shipping container.
Luck & Regards,
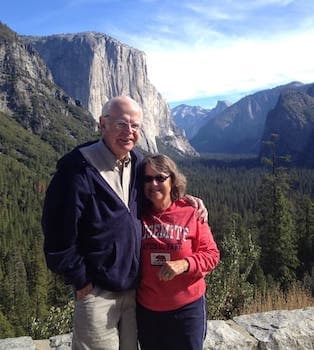
Ted Mooney, P.E. RET
Striving to live Aloha
finishing.com - Pine Beach, New Jersey
A. Has the tumble media been used on anything else so that you are imbedding iron particles into the soft Kleenex-like aluminum? Ahead of chromate the tumble media must be designated "for aluminum only'.
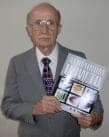
Robert H Probert
Robert H Probert Technical Services

Garner, North Carolina
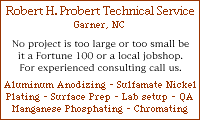
Q. I don't think the tumbling media plays a role in this. We've had failures without tumbling. There are parts that come off the machine and are already fully deburred. Straight to plating and returned to us with this defect. It's not just the "powdery" substance. Sometimes the parts look great. Take a q-tip to it and the plating comes off to where you will see bare aluminum.
Bobby B. [returning]- ODESSA, Florida
September 27, 2021
A. Hi Bobby!
First, questions!
How long after conversion coating are you or your customer going after it with a Q-tip? Hours, days, or weeks? (The only correct answer is a minimum of 2-3 days)
What color is your scotchbrite? Better be red! The grey stuff is no bueno prior to CC. AlOx only!
Is your plater running a whole mess of cast alloys in the same deox/desmut bath, and what controls do they use to determine a dump schedule? (The correct answer is either no shared bath with cast alloys, or a tightly controlled dump schedule based on ICP analysis of the bath for total Si, dumping at 20ppm buildup, preferably BOTH)
How is the plater determining complete cleaning coming out of deox? Is a smear test being done? Seriously, just a white lab wipe to check for residue.
Is the plater maintaining the acidity of the conversion bath correctly in relation to its concentration? Don't fixate on this question, but be aware of it. Also, an aging hexavalent conversion bath may become depleted of the activators necessary for the reaction to proceed.
Weird one... if the tank is steam heated, how well do the coils pass a pressure test? Even a pinhole can introduce iron and kill a tank. Rare, but it happens. The plater's monthly performance specimen results (assuming they are accredited) will catch that quick- ask for them.
Last, and actually do this first... send out some customer-rejected parts for salt fog testing. I use a lab in Justin Texas who I ADORE for one-off jobs on top of my giant monthly suite. The spec says nothing i can recall about yellow residue on Q-tips. If you don't get pits, you've fulfilled the purchase order and the customer needs to understand that. Aesthetics vs functionality. If they want it to be pretty, too... that's a re-quote ;)
If you want to know how I learned all this mess... you bring the beer (IPA, please); I'll bring the NDA and a pen. I swear I'm still suffering ptsd from the first of many go-rounds on this exact topic with this one particular customer and their ever rotating stable of OV wrangler 'engineers'... it never ends. Passing lab results are your ticket to rejecting an incoming SCAR upon receipt.
When in doubt, send it out.
Best of luck!
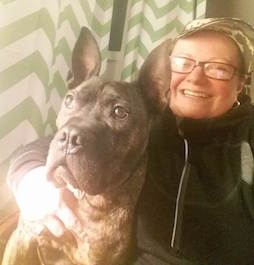
Rachel Mackintosh
lab rat - Greenfield, Vermont
Q, A, or Comment on THIS thread -or- Start a NEW Thread