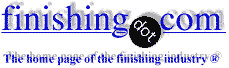
-----
Zinc Phosphating: Ideal Process Sequence?
Q. I want to implement an immersion-type phosphating plant. How many tanks are required, and explain to me the step by step process required. Say the products are from low weight (5 kgs) to high weight (1500 kgs).
Sathesh Pandianexecutive engineer - Navimumbai, Maharastra, India
January 10, 2009
A. Hi, Sathesh. One variation of the 7-step process is: Alkaline clean, rinse, rinse, zinc phosphatize, rinse, rinse, chrome-free post-dip rust preventative. But the reason there are whole books on the subject is that there are countless variations on this process and things to consider. The fastest path to a solution is probably to contact a vendor of zinc phosphating processes or a consultant, who can sit down with you and develop a good solution to your situation. Good luck.
Regards,
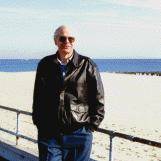
Ted Mooney, P.E.
Striving to live Aloha
(Ted is available for instant or longterm help)
finishing.com - Pine Beach, New Jersey
A. I foresee a problem with quality work. The secret is to have the phosphate tank loaded whenever it is at working temp. A few 5 kg pieces will be a tiny load for the tank and the 1500 kg load will be a problem to keep the tank at operating temperature. A load that large will require a massive heating system or very large quantity of liquid or both. The large quantity of liquid is a problem with tiny loads trying to keep the acid ratio in balance.
It is difficult to overwork a phosphate tank if you can maintain the temperature and have a reasonable amount of liquid per part surface. Conversely, when you under load a tank, it tends to get sick in a short period of time.
- Navarre, Florida
A. Go for a proper 7-stage Zinc phosphating process. You shall never find a better process than this.
This process is claimed to be the most suitable one, with a history of success!
The process is:
Tank 1) Degreasing
Tank 2) Water wash
Tank 3) Derusting
Tank 4) Water wash
Tank 5) Surface Activation
Tank 6) Cold/hot Zinc Phosphating
Tank 7) Passivation.
There are parameters for all tanks. For phosphating in a cold process the parameter is that the total acid should be 36 points for a 10 ml solution titrated with n/10 NaOH, with phenolphthalein as indicator until a Pale permanent pink colour is achieved, and free acid should be between 1.5 to 2, titrated with bromocresol green
⇦ on
eBay &
Amazon [affil link]
as the indicator.
- Coimbatore, TAMILNADU, INDIA
It is our sad duty to pass along the information that the knowledgeable Mr.Shankar was lost to Covid/Corona.
He was awarded with honorable medal by then Indian president Ms. Pratibha Patil. R.I.P.
Q, A, or Comment on THIS thread -or- Start a NEW Thread