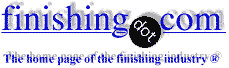
-----
Corrosion of GA or Zinc plating without passivation
December 17, 2008
we are facing a problem of glass run channel rusting in doors of our vehicle.
reasons are as follows 1) No CED between two adjacent panel 2) water accumulation due to capillary action 3) Edge rusting.
there are three potions we are trying
1) Zn coating with passivation
2) Zn coating without passivation
3) GA coating
out of this
(1) trial failed due to difficulty in spot welding due to presence of chromium
(2) some found ok some failed - reason don't know
(3) will it give a rust protection at edge?
product engineer - Nasik, Maharashtra, India
Hi, Sunil. It sounds like you are describing a piece of sheet metal that has been formed into a small U-channel shape, which then sits inside an auto door in the same orientation as the letter 'U' , with the bottom edge of the window glass inserted into it. Am I understanding?
When you speak of the galvanized coating and edge rusting, I presume that this is preplated material that is then sheared to width such that it has no galvanizing on the edge? I think the right way to make this component (from a corrosion resistance perspective) is with a rolled edge so unplated steel is not presented in such a vulnerable position. Good luck.
Regards,
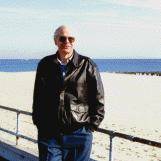
Ted Mooney, P.E.
Striving to live Aloha
(Ted can offer longterm or instant help)
finishing.com - Pine Beach, New Jersey
December 17, 2008
Dear Mr Deshmukh,
Your difficulty in Welding may be on account of parts being Hexavalent Yellow, if you switch to Trivalent Blue, the welding problem will disappear. Look for consistent voltage on the projection/spot welder, Voltage fluctuation may be the reason for failure and not the Chromium if you are already using Trivalent Blue.
It may be a good idea to plate the entire assembly after welding, and still touch up the bleed out area with paint as is with the weld spots.
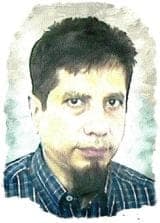
Khozem Vahaanwala
Saify Ind

Bengaluru, Karnataka, India
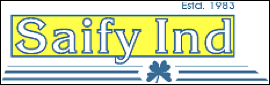
January 15, 2009
February 19, 2009
Dear Deshmukh,
Spot welding problem can be solved by using Copper-Chromium-Zirconium spot welding tips. In the absence of zirconium, Zinc coated sheets are difficult to spot weld (or any resistance welding)
You can try hot dip galvanized channels instead of channels. That will provide better protection.
- Lahore, Pakistan
Q, A, or Comment on THIS thread -or- Start a NEW Thread