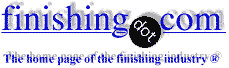
-----
HARD ANODIZING COATING THICKNESS NOT BUILDING UP
November 21, 2008
Dear All,
I am Hard Anodizing 6061-T6 Aluminium as per MIL-A-8625,TYPE 3,CLASS
1-Nickel Acetate Seal after Anodize ( Drawing Specifies Seal )-we try to achieve 80 microns anodizing layer(customer request).
We use only DI water for all solutions in our plant.
My bath is anodizing 35000 sq.in. per day and hence is in a state of constant usage.
The latest Lab report has given following values
Al-Content: 5.81 g/l
Oxalic Acid Content: 10.08 g/l
H2SO4: 151.743 g/l
I have added 200 kgs H2SO4 since the report to try and bring the Sulfuric Acid content up to around 230 g/l-lab report is awaited after new acid addition.
However for the last One month ( both before acid addition as well as after)-the coating thickness refuses to move from an average of 55 microns-sporadically some parts do build up to 70 microns but cannot find any firm reason for the same either.
Air Agitation is vigorous and uniform.
Operating Temperature is between -9 deg cel to -2 deg cel-consistently for all our Lots.
Current Density is 24 asf -- unable to go higher due to Power restrictions in LT installation.
Nickel Acetate Seal tank pH is between 5.5-6.5 and is maintained at
70-75 deg cel before putting jobs in for sealing.
Color of jobs is beautifully black and everything looks perfect-except that I am simply unable to bring the coating back to the 80-100 microns range, which we so effortlessly were able to achieve, in just the recent past!Although 55 microns and above is still accepted by the MIL-8625 std I am not satisfied due to the
'UNKNOWN' nature of the problem.
URGENTLY,Please Help.What am I doing wrong? If any of the experts can suggest any improvements to my process in any stages-you are welcome,I shall appreciate it.
What concentration of Oxalic Acid is ideal for our process?At what level of Oxalic, will the coating become brittle?
Thanks in Advance.
Hard Anodising Facility Owner-Mechanical Engineer - Belgaum, India
Ravi
If you were achieving 80-100 micron thickness before, and now you can not, something has changed. If nothing has changed in your shop, look for a change outside your shop, i.e. your customer's material. Make sure there is no change in your shop before you suggest to your customer that they have changed the process.
- Colorado Springs, Colorado
November 24, 2008
Your anodizing condition is a little bit tough, especially there is Oxalic acid.
my suggestion is that changing your Oxalic concentration to 4--6g/l and your bath temperature to -4 to -2 degree C while keeping your sulfuric acid the same.
- Singapore
November 28, 2008
December 2, 2008
Dear Willie and John,
Thanks for yr kind response.
The material is certified 6061-T6 made by Reputed Leading Indian Company.Have also tried with Alcoa 6061-T6 which is our regular material-even that is giving similar thickness.
Presently getting solution analysed by another lab to rule out error in lab report.
After that we will be more sure of the Oxalic Acid and H2SO4 content.
Has anybody heard of Free Sulphate Ions in solution affecting Hard Anodizing?If yes,pls enlighten me.
Is it different from normal gm/ltr H2SO4? I am trying to maintain
225-250 gms/ltr-is it too high?
Have also cleaned out lead cathode sheets, emery brushed and put back.
Have purchased new coating thickness measurement instrument-which is giving same result.
Maybe some of the experts on this site can throw some light as well?
Thanks for yr support.
- Belgaum, India
Ravi
Not all aluminum is created equal. Expect to see variations in anodize results between heat lots of aluminum. Were you able to get good results one day, and not the next?
Too much dissolved aluminum will effect your ability to achieve the greater thicknesses.
225-250 g/l is towards the high end, but would tend to help achieve the greater thickness.
Look at the terminal voltage when you were achieving 100 µm thickness. Are you at the same now as when you get to 50-75 um? A remote possibility would be your rectifier... is it running on all three(?) legs of phase? No blown diodes?
Also consider having your competitor friend run some parts to see if he gets the same results.
- Colorado Springs CO
December 2, 2008
Q, A, or Comment on THIS thread -or- Start a NEW Thread