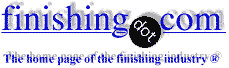
-----
Corrosion on sharp edges metal parts with polyester powder coating
The metal part was zinc phosphated and electro-powder coated. The sharp edges of the parts couldn't be properly covered up if compared to the flat surfaces.
What should be the right way or process in order to solve this problem?
End User - Penang, Malaysia
November 18, 2008
To cover the sharp edges you should have to put a 2-layer powdercoating system:
Epoxy-powder-primer / IR-oven / Topcoat (polyester, acrylat, ...) / curing oven.
- Zoersel, Antwerp, Belgium
November 25, 2008
I'll probably get some static with this response, but this particular problem is unusual with powder due to the "wrap around" nature of the static charge. Powder wraps around the edge and onto the opposite side as the part is being coated, effectively coating the edge twice and creating a heavy bead which is a typical complaint in itself. Wet paint is different in that it doesn't wrap around, leaving edges lacking in paint thickness. Do you know for a fact that you are getting the paint process that you are paying for?
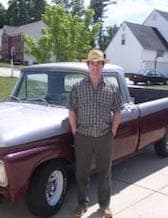
Sheldon Taylor
supply chain electronics
Wake Forest, North Carolina
November 26, 2008
For aesthetics and corrosion protection, this is a common problem with powder and paint. During curing the coating pulls away from sharp edges e.g. guillotine or NC turret punch cuts. Maybe look at the design of the item and the material used. See for further information: www.duluxprotectivecoatings.com.au/technotespdf/1.1.5%20Perforated%20metal.pdf
Chris Sweetnam- Melbourne, Vic, Australia.
January 7, 2009
February 11, 2009
To solve the problem, try the following:
- rounding sharp edges.
- deburr edges and clean them off manually.
- apply 2 layers.
It's common that edges don't get covered well because of lower surface tension. During the curing, the coating will flow away from the edge. Make sure no burrs occur on the edge. The burrs can stick through the coating, causing corrosion problems.
- Beijing, China
Edges do need to be rounded off and deburred prior to coating. I would also agree that a two coat system would be best.
Tony Williams- Wolverhampton, West Midlands, UK
February 16, 2009
Q, A, or Comment on THIS thread -or- Start a NEW Thread