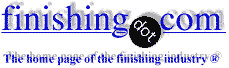
-----
Trouble shooting for electroplating
November 3, 2008
I face in my experiment some troubles and I can't solve it, I use Nickel sulphamate solution, the percentage of electrolyte is 300 g/l Nickel sulphamate, 5 g/l Nickel chloride and 30 g/l Boric acid - the operation conditions is temp. is 40 c, cathode current density 2 A/dm2,PH 4.5 and the current is 0.08 amp.
the problems:
1- the pH decrease during the experiment reach to 2, how can I modify it?
2- the bubbles deposit on the surface, how can I remove it?
3- the coating layer not good adherence, what can I do to improve it?
take in your information, I clean the nickel and substrate before experiment and I use stirring machine to make a homogenious surface.
please reply to me urgently, because I repeat the experiment for many times and the same problems will happen.
student - Malaysia
First of three simultaneous responses --
1. You are using an insoluble anode. You need to use sulfur depolarized nickel for the best operation.
2. You need an anti pit agent (wetting agent) and should have good agitation, either mechanical or pumped or oil free air. I used pumped and air.
3. Your part is not clean enough and you may need to go to a nickel strike before the plate on some metals.
You really need a book on plating.
- Navarre, Florida
November 5, 2008
Second of three simultaneous responses --
First, the bubble are caused by gassing. In order to eliminate the pitting that results from these gas bubbles adhering to the surface during plating, you need to use a surfactant/surfactant blend also known as a wetting agent or anti-pit. Second, the pH will always increase during the operation of the plating bath since hydrogen gas is evolved - the hydroxyl ion raises pH. This is adjusted using dilute reagent grade sulfuric acid.
Third and most importantly peeling from base metal is generally due to surface prep. You need to alkaline clean (soak), electro clean and acid dip (to activate and remove cleaning smuts). One to three rinse steps is taken between each of these processes.
process supplier - Great Neck, New York
November 5, 2008
Third of three simultaneous responses --
Hi Mohamed,
1) The pH of a sulfamate bath when correctly operated should rise slowly. If it falls then there is either insufficient anode area or the anode material is unsuitable. Pure nickel such as electrolytic nickel or thin sheet from laboratory suppliers will not dissolve properly. There is a lowering of nickel concentration in the bath accompanied by a fall in pH. Apart from the pH problem there will be chemical decomposition of the sulfamate. This will yield compounds which will cause compressive stress, a significant rise in hardness and brightness of the deposit. You should use an anode material designed for the purpose. Durvanic and "S" nickel are suitable.
2) The stirring should help in removing bubbles but the addition of a surfactant (wetting agent) will help greatly. The surfactant should be intended for nickel plating. The use of the wrong type can have serious consequences. Do not use air agitation and choose a type which gives a low surface tension. Lowering of surface tension will give a bath bath which will foam excessively if air is bubbled through it. Consult your local supply house. Ask for a sodium lauryl sulphate type.
If is difficult to answer question (3) because you do not say what the substrate is. It is neccessary to know this in order to advise what surface preparation is require.
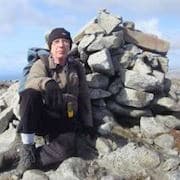
Harry Parkes
- Birmingham, UK
November 6, 2008
The substrate is FeCrAl
Mohamed Gomaa- Malaysia
November 10, 2008
Hi Mohamed,
An actual composition would have been helpful. The catch-all treatment is hydrochloric acid dip followed by Wood's Nickel Strike. This comprises 250 g/l nickel chloride and 50 ml/l hydrochloric acid (1.16 SG). Use cold at 100 asf (10 amp/dm2) for one minute. Ideally the work would be transferred to the plating bath without rinsing. But this practice results in excessive carry over of chloride so rinse and start plating quickly.
Did you find any of the previous submissions of any help? What are your conclusions?
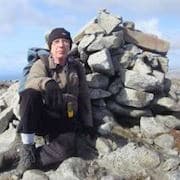
Harry Parkes
- Birmingham, UK
November 12, 2008
Just an observation, Mr. Gomaa. Should you need to lower your pH, use diluted sulfamic acid, not sulfuric. Sulfuric will raise sulphates and cause stress problems. Good luck!
Guillermo MarrufoMonterrey, NL, Mexico
November 13, 2008
Hi Mr.Harry Parkes
what is the percentage of sodium lauryl sulphate can I add it to electrolyte?
- Malaysia
November 23, 2008
Mohamed, you do not say how you are preparing your FeCrAl substrate, nor what the actual composition is. Your poor adhesion is due to poor surface treatments, so you need to make sure your substrate is correctly prepared. This will involve a good alkali wash followed by an acid etch. The exact process will depend on your substrate composition. It will also be dependent on what you have available, so you will need to talk with the chemical supplier about the availability of processes.
I would also recommend you use either a nickel strike, such as Woods nickel, or even use a copper interlayer. Either one will improve adhesion to your substrate.
You mention gassing - this tells me that you are probably using inert anodes - you should use sulfur depolarised nickel as these will dissolve in your nickel sulphamate bath. You should also use a good wetting agent to remove gas bubbles from your workpiece. Also make sure the anode:cathode ratio of area is about 2:1 - this is not critical, but should be as near as reasonably possible. Harry suggests you use sodium lauryl sulphate, but this will foam in the presence of air agitation and you will have a bath covered in a blanket of foam. I would suggest you use a non-foaming surfactant, but again their availability will limit your selection. If you can only get SLS or other foaming wetting agents, do not use air agitation, but mechanical agitation or eductors. The concentration of wetting agent will depend on the type being used, but in general it is 0.2-0.5ml/litre.
You also mention that the bath pH is 4.5 - this is a bit high even for nickel sulphamate, so I would recommend you reduce it to 3.8-4.2. This can be done by adding sulfamic acid
⇦ on
eBay
or
Amazon [affil link] - do NOT add sulfuric acid as this is a totally different acid.
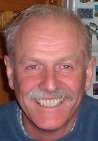
Trevor Crichton
R&D practical scientist
Chesham, Bucks, UK
December 14, 2008
Q, A, or Comment on THIS thread -or- Start a NEW Thread