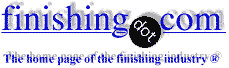
-----
Galvanic Action between Stainless Steel and Phosphate
Q. Hello - In restoring an antique 1967 Corvette I find that although the front sides of the wheel trim rings are in excellent shape, the back sides have separate captive rings that retain clips to hold the entire assembly to the wheel. The captive rings cannot be removed from the ring assembly for refinishing without adversely affecting the cosmetics that are identified with originality.
The trim rings are stainless steel that are flash chromed on the front side. The back side which is in contact with the separate captive rings is 'bare' stainless. The captive rings to which the retaining clips are spot welded to are made of a low carbon steel that already have significant rusting.
I am considering the use of a product containing phosphoric acid that will convert the iron oxide to iron phosphate to arrest the rust.
My question is: what is the potential for galvanic action between stainless steel and iron phosphate parts that will be in direct contact?
Thanks for any feedback!
hobbyist - Angier, North Carolina
October 13, 2008
A. Hi, Bob. Iron phosphate is not a metal, so it will not contribute to galvanic corrosion with stainless steel. Phosphating the steel component will not hurt, it will only help, but probably not much. Keeping the area salt-free, clean, and dry will be key to deterring further corrosion.
Regards,
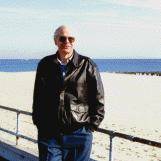
Ted Mooney, P.E.
Striving to live Aloha
(Ted can offer longterm or instant help)
finishing.com - Pine Beach, New Jersey
October 12, 2008
Q. Hi all,
As part of a complex system, we are currently needing to couple two dissimilar metallic parts. The first part is a carbon steel part that will be painted. However, on the interface, steel + zinc phosphating will be in contact with stainless steel. This particular galvanic interface is expected to be exposed to free weathering. Can anyone recommend me a way to counteract the galvanic effect, as I guess it might be very detrimental for the carbon steel? Is zinc plating on stainless steel an option? or should I do something on the carbon steel surface?
Many thanks in advance and best regards,
Angel
Product Development Engineer, Electronics - Swindon UK
March 17, 2017
A. Hi Angel. If the steel part is to be phosphated and painted, is it possible to paint it all over? Bare steel or phosphated steel will corrode fairly quickly whether in contact with stainless or not, whereas painted phosphated steel is much better off. Rainwater is not highly conducive to galvanic corrosion because it is not very conductive, but road salt, lawn fertilizer, cleaning agents and other things can make the water quite conductive.
It's hard to offer definitive answers (or even strong guesses) without knowledge of the details, starting with what the thing is :-)
Regards,
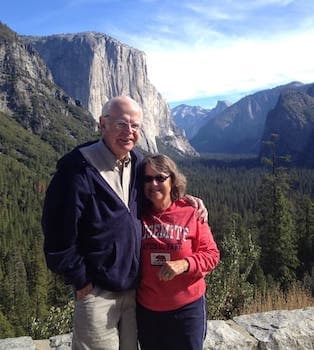
Ted Mooney, P.E. RET
Striving to live Aloha
(Ted can offer longterm or instant help)
finishing.com - Pine Beach, New Jersey
March 2017
Q. Hi Ted,
Thanks for your support. Two housing components will be fitted together (horizontally) with stainless steel laminated shims in between for dimensioning reasons. One housing component is steel+phosphate+paint and the other one is aluminum+chromate conversion coating+paint. However, neither of the components can be fully painted as electromagnetic characteristics inside require it this way.
My concern is then, in the minor regions where water can permeate through the interfaces and reach a non-painted surface (steel or aluminum) which will could be in contact with stainless steel and suffer from contact corrosion plus the self corrosion which we know will eventually occur in a surface like that. Is there any protecting method or a way to prevent premature corrosion on the non-painted surfaces?
Product Development Engineer, Electronics - Swindon UK
March 23, 2017
A. Hi again Angel. I'm not really understanding your description of the assembly process, or the exposure conditions, or the prohibition against painting, so I'm flying blind :-(
But wet steel in contact with stainless steel is a problem.
Are you sure the steel can't be electroplated with a conductive but corrosion-resistant metal instead of being phosphated?
Regards,
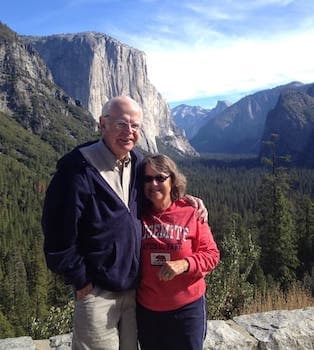
Ted Mooney, P.E. RET
Striving to live Aloha
(Ted can offer longterm or instant help)
finishing.com - Pine Beach, New Jersey
March 2017
Q. Hi Ted,
Thanks for your support. We are now planning on zinc plating the steel component before painting, as additional protection. However, is zinc phosphating still recommended for paint adhesion (on zinc-plating substrate now) or the zinc plating is good enough for paint application? Also, is electroplating better for relatively complex geometries or hot dip galvanizing? Thanks again for any input.
Best regards,
Angel
- Swindon, UK
March 27, 2017
A. Hi again. Zinc plating is almost never phosphated, probably because it's invariably chromate conversion coated, which can be a good pretreatment for subsequent painting. Galvanizing is heavy and may be inappropriate for joined parts. Zinc electroplating may not be consistent in thickness depending on the geometry, but it will be free of drips of metal and such.
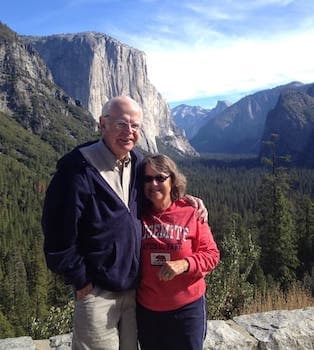
Ted Mooney, P.E. RET
Striving to live Aloha
(Ted can offer longterm or instant help)
finishing.com - Pine Beach, New Jersey
March 2017
Q. Thanks for your help Ted. Appreciate it. With regards to dissimilar material combination, I have found that varnishing or tinning with wax can be used as additional protection at "higher" corrosiveness conditions. However, I still can't understand what this implies. Do you have any input on this? Thanks in advance.
Angel Espinosa [returning]- Swindon, UK
March 30, 2017
A. I don't think I understand the question, and I am not familiar with "tinning with wax". Still, one of the reasons steel corrodes faster than most other metals is that the corrosion product (rust) is not tight, adherent, and glassy like the oxidation products of many other metals, tending to seal the substrate metal away from the environment ... rather, it's pretty much the opposite: rust is loose, fluffy, & hydroscopic and can leave the surface pitted. So almost any coating, probably even including dipping in chocolate, helps reduce rusting at least a little bit :-)
Regards,
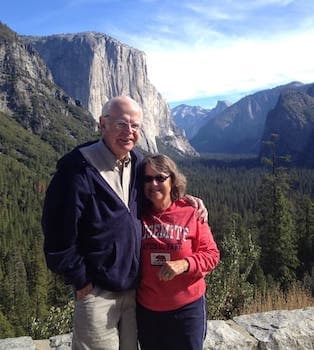
Ted Mooney, P.E. RET
Striving to live Aloha
(Ted can offer longterm or instant help)
finishing.com - Pine Beach, New Jersey
March 2017
Corrosion books and courses
Q. Dear Mr. Mooney. I have seen your answers and I would like to ask you kind of a personal question.
I write you from Spain and I work in the valve industry. I am looking for a good course or book related to corrosion basics (I have checked NACE standards, Compass corrosion and similar) Do you have any advise?
Thanks a lot in advance,
- Madrid, Spain
December 5, 2018
A. Hi Miriam. Although I curate this website, which has expanded to cover a lot of ground, my own experience has been in electroplating & electroplating equipment/plant design. Sorry, I don't have much experience in corrosion training courses or books. Hopefully another reader will have suggestions.
Regards,
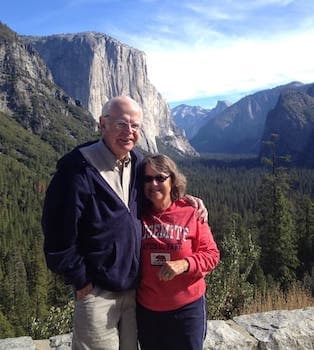
Ted Mooney, P.E. RET
Striving to live Aloha
(Ted can offer longterm or instant help)
finishing.com - Pine Beach, New Jersey
December 2018
A. Hi Miriam
It took me about three seconds to find:
https://www.google.com/search?q=corrosion&client=firefox-b&source=lnms&tbm=bks&sa=X&ved=0ahUKEwikq9quvIvfAhV8XRUIHWKIC7gQ_AUIESgE&biw=1366&bih=654
Geoff Smith
Hampshire, England
December 6, 2018
A. When I took a corrosion course in graduate school, the textbook used was "Principles and Prevention of Corrosion" by Denny A. Jones, published by Prentice Hall.
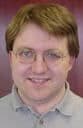
Ray Kremer
Stellar Solutions, Inc.

McHenry, Illinois
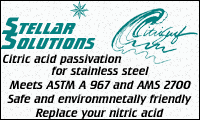
December 6, 2018
December 7, 2018
A. Hi Miriam,
Though it's a bit old, the reference I personally keep on my desk is 'Corrosion of Building Materials' by Dietbert Knofel, published originally in German in 1975 and then in English in 1978, by the Van Nostrand Reinhold Company. About half of the book is devoted to metallic materials and there is a section on testing. It also covers concrete and organic materials. It's not extraordinarily in-depth but definitely a good start. I'm certain it is out of print, but no doubt there are copies floating around the internet used-book vendors. It's a handy and quick read.
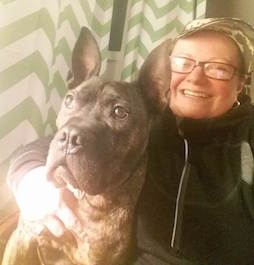
Rachel Mackintosh
lab rat - Greenfield, Vermont
Q, A, or Comment on THIS thread -or- Start a NEW Thread