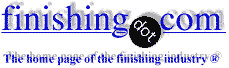
-----
Rough Plating in Nickel Sulphamate Plating
October 2, 2008
Greeting.
We're encountering rough plating in nickel sulphamate plating. The plating parameters: plating current at 40ASF & plating time = 20minutes, plating area = 0.047 sq. ft.
Cross-section photo as below:
Our normal plating time = 7-8 minutes at 40ASF to achieve nickel thickness 5-7um.
With ensure other plating parameters (chemical concentrations, temperature, agitation rate, etc) remain the same, only for this particular case, we need to plate at longer time to achieve nickel thickness 10-14 um, and hence encountered rough plating issue.
We tried to post the question to www.finishing.com, but failed to do so. And hence, write this mail to you.
Hope that you can for the solution to solve the rough plating issue
Thanks!
Regards,
Ivy Lim- Malaysia
![]() |
October 2, 2008 The cross section did not show with the posting. - Navarre, Florida You do not mention whether you use proprietary additives for grain refinement, anti pit, etc. You do need these type of additives. Further, filtration is critical when plating thickness increase. You must filter through a 20 micron or smaller media (you may need to go as low a 1 micron)and have anodes bagged with napped polypropylene material or similar. Make sure the bags protrude above the surface of the solution. Also look for outside sources of particulates i.e. flaking tank linings, particles dropping from overhead, etc. Gene Packmanprocess supplier - Great Neck, New York October 2, 2008 Drop the current density to 20 ASF. Be sure the agitation is uniform, not hitting then part, and is even on all sides of the part. Temperature at 120F. Be sure the boric acid is right: too low causes pitting, too high, precipitates and causes "shelf roughness". Check anode bags, are sulfur particles blowing thru the bags and circulating throughout the whole solution. Filter !. A slight leak in the filter causes a very small high pressure air bubble and this will cause roughness. ![]() Robert H Probert Robert H Probert Technical Services ![]() Garner, North Carolina ![]() October 2, 2008 |
October 4, 2008
Hi all,
Thanks for help!
Sorry for the incomplete information, please refer for the evaluation details as below:
1. adjusted nickel sulphamate bath temperature from 40 - 60 °C
2. Use 5 micron filter cartridge & PP anode bag.
3. Use Atotech proprietary additive:
A5 brightener 5 - 10 mL/L
NPA wetter 1 - 3 mL/L
4. adjusted current density from 10 - 40 ASF.
A series of evaluations had being conducted based on above parameters, but my rough nickel issue still didn't resolve.
please advise what should be further adjust to solve this rough nickel plating issue?
Thanks again!
- Malaysia
October 6, 2008 Hi, ![]() Harry Parkes - Birmingham, UK Talk to your Atotech service people. They are getting your business, so, they should help you. Guillermo MarrufoMonterrey, NL, Mexico October 6, 2008 |
The most common cause of rough deposits is poor filtration and a contaminated plating bath. I would recommend 1 micron filters and a filtration rate of 4-6 tank turnovers/hr. If you are electroforming, I would increase the filtration to 10 tto/hr. Give the tank a good filtration preferably overnight, before using it. Make sure there is no dust or other debris falling into the tank. Nickel sulphamate should operate at about pH 3.6-4.4 - outside this will cause other problems. If you can keep it to 3.8-4.2, even better.
Are you using sulfur depolarised nickel - if not, the anodes will not dissolve properly and this could cause problems in the tank, especially if your bath has ,ow or no chloride in it; make sure your anode bags are clean and not torn.
We can only speculate at what causes the problem, but if you can give all your process specification, maybe we can help you.
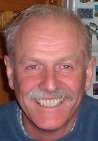
Trevor Crichton
R&D practical scientist
Chesham, Bucks, UK
October 7, 2008
Sorry that the pictures were late, folks, but here they are -- Ted
October 15, 2008
All the previous answers have merit and should be done.
An immediate cure is to pump the plating solution into a storage tank and filter it back into the cleaned and rinsed plating tank. Use a 5 micron or lower using a clean filter cartridge that has been soaked in hot water and rinsed. (to remove any sizing). Do the anode bags as suggested, be sure that the top of the bags are above the solution level and there is not vigorous agitation around the bagged anodes.
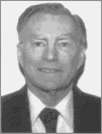
Don Baudrand
Consultant - Poulsbo, Washington
(Don is co-author of "Plating on Plastics" [on Amazon or AbeBooks affil links]
and "Plating ABS Plastics" [on Amazon or eBay or AbeBooks affil links])
October 14, 2008
Hi Ivy,
I hope this can help to your nickel roughness problem:
Roughness. Roughness is generally the result of particulate matter suspended in the solution and adhering to the work; especially on shelf areas. Gross roughness may be traced to improper cleaning, torn anode bags, airborne dirt, dropped parts, precipitated calcium sulphate, inadequate filtration or carbon and filter aid from an improperly packed filter. A very fine type of roughness may be caused by precipitation of metallic contaminants in the cathode film, where it may be confined to a particular current density region. Chromium, iron, and aluminum can precipitate as hydrates in the higher current density areas, where the film pH is normally higher than that of the body of the solution; a lower operating pH may be helpful in such cases. On occasion, high current density roughness has also been traced to a magnetic condition of the work. Another source of roughness can be the air blower used for air agitation. Inspection of the filter on the air blower may reveal that it could be defective or missing.
If an external cause of roughness is not apparent, the quickest remedy is to pump the solution to a spare tank and inspect the plating tank. The cause may be apparent: dropped parts and torn anode bags are the most common sources.
Pls check this out:
Maximum allowable concentration of metallic contaminants In nickel plating baths:
Contaminant Maximum Concentration, ppm
Aluminum 60
Chromium 10
Copper 30
Iron 50
Lead 2
Zinc 20
hh
Calcium pH dependent; will precipitate at the saturation point.
NOTE The limits may be different when several contaminants are present at the same time, and complexing agents are a part of the solution formulation.
regards and good luck
- Philippines
Hi all,
Really appreciate all the advises, they guide me to have a better control of our plating baths!
As mentioned earlier, encountered that high copper contamination in our nickel sulphamate bath (>60ppm). By doing continuous dummy plating in the bath, we reduced the contamination level to <10ppm. And it solved the nickel rough plating issue ^_^
Thanks!
Regards,
- Melaka, Malaysia
October 15, 2008
Q, A, or Comment on THIS thread -or- Start a NEW Thread