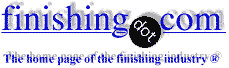
-----
Pitting in acid copper plating bath
Q. I found pitting on the plated copper layer (acid copper plating). I hope I can have a smooth copper surface, not the surface full of pitting. 60 ppm of chloride ion is in the plating bath.
I have tried to do the plating at both 1.9 ASD and 4 ASD current density However pitting on the plated Cu surface is still observed. I use photoresist as plating resist to plate the desired pattern. I would like to know how to minimize the pitting. Thanks.
- Hong Kong
2000
I like the chloride to be 75-90 ppm. You should be utilizing a proprietary additive, manufacturer makes chloride recommendation. The bath temperature should be 70-90 °F. 90-120 °F must have a proprietary brightener. If the acid copper bath has turned dark green, heavy organic contamination. The anode area should be 1:1 cathode/anode ratio for pattern plating. Hope this helps. Bill Hemp
tech svc. w/ chemical supplier - Grand Rapids, Michigan
by N. Kanani
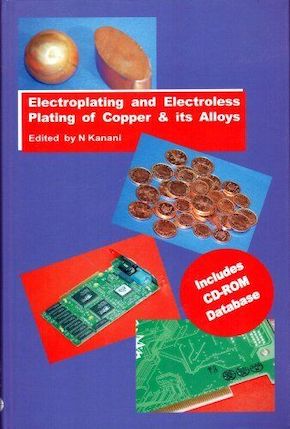
on eBay or Amazon
or AbeBooks
(affil link)
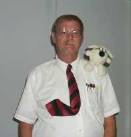
James Totter, CEF
- Tallahassee, Florida
2000
A. Kelvin
In our experience James Totter's remarks are on target. Often it can be of the greatest importance how you are pre-plate cleaning and what you are using. You must start with proper photo resist exposure and follow that with complete & clean development. Side wall attack usually is due to using the wrong pre-plate cleaning chemistry for the resist being used. Side wall attack will be seen at this point. You never stated your process, ie., are you putting your dry film over treated electroless, or are you striking the boards before applying the resist? You also did not say if you were using a microetch after the pre-plate cleaning chemistry and if so how much electroless or strike copper you are removing. Also if would be helpful to know if your pits show up on the pattern plated copper, or after they have been SnPb plated. If the pits are on the copper traces are they on the outer edges as little half-moon cutouts, or what we term "mouse- bites".
- Orange, California
A. Pitting in Acid Copper is due to lack of surfactant, so add wetting agent, or pitting is also due to organic impurities so carbon treat the bath or pitting is also due to imbalance of brighteners so add brighteners by conducting trials in Hull Cell ⇦ huh? using polished Brass panels.
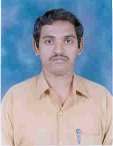
Panjala Mukesh
fashion jewelry mfgr.
Hyderabad, India
Q. Is there a UV spray or solution currently available that you can apply to the surface of a copper plated part that will show up pitting marks in the plating?
Mike SwibelBuyer - Illinois
March 31, 2011
A. Did you try PAM?
Tim Kovacik- Hillside, Illinois
January 18, 2012
adv.: Supplier of Copper Anodes, Nickel Anodes, Bismuth Metal, & Other Metal Products for Industry & The Arts
Q, A, or Comment on THIS thread -or- Start a NEW Thread