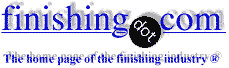
-----
How to increase the productivity of electroformed CD stamper
We are using a local made stamper; the maximum it can produce is 0.2-0.3 million CD's. If we use imported CD stamper from Sony, it is capable of producing 0.6 million CD's. We use nickel sulphamate (90 gms/L), boric acid (50 gms/L) and cathode current= 2.5 for 1 hour & 30 minutes. How can we improve the productivity of stamper. Please suggest.
Manoj BhardwajR & D - Noida, Uttar Pradesh, India
September 2, 2008
Hi, Manoj. If you are trying to reverse engineer Sony stampers, I would suggest starting with a patent search which may reveal how they do it, and tell you whether you are forbidden from doing the same. Then I would analyze their stamper to see if it was nickel-cobalt rather than straight nickel. Then I'd test the hardness and wear resistance and try to quantify what is different about it. Good luck.
Regards,
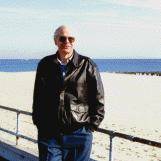
Ted Mooney, P.E.
Striving to live Aloha
(Ted can offer longterm or instant help)
finishing.com - Pine Beach, New Jersey
September 5, 2008
Manoj,
Ted is right about the illegality of reverse engineering Sony's technology to make CD's. However, if you want to run the risk of having your company taken to court and sued, so be it. Personally, I would support Sony in any court case.
That being said, I think your nickel bath is wrong. You are using
50g/l boric acid and 90g/l nickel sulphamate; the current is 2.5 ?. You need to be more precise in your conditions and bath composition.so please resubmit your details with all your bath's compositions and operating conditions. What is the nickel hardness and stress you are achieving. Please give a full analysis of your bath and the nickel deposit used to make your electroform, then you will get some sensible answers that may help you copy Sony's technology. You should also do a full analysis of the Sony nickel and look for cobalt.
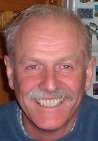
Trevor Crichton
R&D practical scientist
Chesham, Bucks, UK
September 5, 2008
October 1, 2008
Mr.Trevor Crichton,
Following are the bath composition & operating conditions
Nickel Sulfamate - 90 gram /lts
Boric Acid - 50 gram/ lts
Cathode current density- 2.5 A/dm2
pH of bath- 4±0.2
Temperature - 55 °C
Time - 1 hour & 30 minutes
Thickness of electroforming - 290 - 300 microns
Hardnes- 220 programmable
- 170-180 (back side)
we have done chemical analysis of the both CD stamper but there is no difference in composition & no cobalt present in competitor Cd stamper.
- India
October 6, 2008
Manoj
the parameters you are giving can not be correct, a concentration of
90 g/l Nickel sulfamate would mean that you have a Nickel concentration of only around 17 g/l which would be far to low. Also it is impossible to plate 300 microns of Nickel in 90 minutes using only 2,5 A/dm2.
Marcus
- Lucerne, Switzerland
90 g/l is Nickel concentration in nickel sulphamate solution.
Manoj Kumar Bhardwaj- India
October 14, 2008
October 15, 2008
Manoj,
There is something wrong with your figures. Using 2.5A/dm2 is equivalent to about 25mA/cm2. Nickel plates at 1 micron/min at 50ASF
(~55mA/cm2), so in 90 minutes, you will only get 43 microns of nickel deposited. Furthermore, this is the most efficient you will get and this would be at pH 3.8-4.2.
Regarding the hardness,one of the most common hardeners and brighteners used with nickel is sodium saccharin - this is very difficult to detect in the nickel, but using sensitive techniques it may be possible to detect sulfur of the relevant bonded structure in the nickel deposit. Simple chemical analysis of the nickel will not show whether sodium saccharin has been used, but it certainly will deliver a hard and low stress deposit. My guess would be they are using about 0.5-0.8g/l sodium saccharin and this will give a hardness of about 280-350Hv and an internal compressive stress of about
70-100MN/m2.
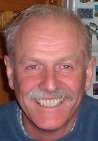
Trevor Crichton
R&D practical scientist
Chesham, Bucks, UK
Q, A, or Comment on THIS thread -or- Start a NEW Thread