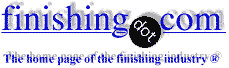
-----
Problem of rust occurring at weld points of mild steel panels
I am the supplier of mild steel panels (fencing) for the swimming pool industry in France. My panels are produced using 8 mm mild steel. These are spot welded. After this, surfaces well cleaned, a zinc primer applied and then powder coated.
Problem that I have is that rust starting to appear at all the weld points. On the regular surface, I have no problem....it is only on the welds
Thought that to get round this I could first galvanise and then powder coat. Have been advised that because I am using a 8 mm round bar, powder coating does not have enough surface area to adhere to after galvanising and as a result will flake.
Would welcome ideas/suggestions/thoughts
Perhaps use a plastifier after powder coating?
Industrialist - Le Lavandou, Var, France
September 4, 2008
September 6, 2008
Someone has given you poor information.
It is perfectly possible to powdercoat over galvanized steel, even at diameters much lower than 8 mm (like 1 mm) and get good adhesion.
But to do so you will require a competent pretreatment, such as zinc phosphate, chromate or one of the newer silane based systems.
Without pretreatment, it will not adhere to the galvanizing.
Doing this correctly should give you 20-30 years life expectancy for the powder, and rust free for over 50 years.
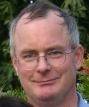
Geoff Crowley
Crithwood Ltd.
Westfield, Scotland, UK
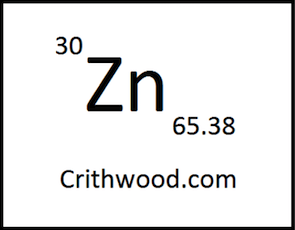
Geoff is correct in that it is possible to powder coat galvanized substrates (click on our image). However, can you improve the corrosion resistance of your current process? I think the answer is yes. Geoff suggested several pretreatment options for galvanised substrates - one being sol-technology. We are currently evaluating a waterborne material that offers 500 - 3000 hours ASTM B117 resistance, depending upon the film weight applied, i.e. 1 - 8 microns. This is dependent upon the working solids at the application stage. Unfortunately, the higher the solids, then the cost becomes inhibiting for most situations (40-50 Euros per litre) but there are those situations where prevention of rust out-weighs the cost. Maybe, in this particular case, only the welded areas require treatment?
Terry HicklingBirmingham, United Kingdom
September 8, 2008
Q, A, or Comment on THIS thread -or- Start a NEW Thread