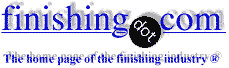
-----
Hot dip galvanising for S G iron products
Dear Sir,
We are facing very high problems in hot dip galvanising of S.G iron products.
When we try to dip it into the acid bath zinc doesn't adhere to the surface uniformly. It means that zinc gets deposited on the surface as patches. There are many bare parts.
What could be be the reason for this and the appropriate solution?
Please guide
Thanks in advance.
plating shop employee - India
August 23, 2008
Sir,
I had to "look-up" S G steel on the internet and it seems to be a type of cast iron. About 30 years ago I tried to clean castings using HCl and H2SO4 with little success. Then I tried with HF (hydrofluoric acid) and immediately the sand was removed and deposited on the bottom of the beaker. HF is extremely dangerous and I knew a guy who died from inhaling HF fumes. The glass "face" of his wristwatch was etched.
Some galvanizers use sand or grit blasting to clean castings, however too much blasting can break through the "shell" of the castings into graphite (carbon) rich areas and then the castings will not galvanize.
It is also possible that your flux solution is bad. You did not mention if you are using "wet" or "dry" galvanizing.
Regards,
Galvanizing Consultant - Hot Springs, South Dakota, USA
August 29, 2008
I don't know about wet or dry hot dip galvanising. It is being done in a zinc bath at a temp of 550 deg c.
Can you explain on this point.
The problem we are facing is that after taking out the product from the bath on some regions of the product sand comes over and no zinc is deposited on the surface. So a part of the product if left bare.
What can be done?
Regards,
- India
September 2, 2008
First of two simultaneous responses -- September 2, 2008
Sir:
"Wet" kettle galvanizing uses a top flux which is molten ammonium chloride/zinc chloride floating on the molten zinc. The usual color of this molten floating flux is black and it is smoking continuously. The items being galvanized pass through this molten flux, held in the zinc until "cooked out," and then withdrawn through molten zinc after the molten flux is skimmed to one side.
In "dry" kettle galvanizing the items being galvanized are put into a water solution of ammonium chloride/zinc chloride (best if this solution is hot at 70 deg C) and then immersed directly into the bare molten zinc, cooked out, skimmed, and withdrawn from the zinc.
550 °C is much too hot for normal galvanizing. The usual temperature is around 450 C.
The presence of sand (from the sand casting process) seems to be the problem. You must sand or grit blast off this sand (from casting) or use HF or sodium bifluoride in HCl or H2SO4. Remember HF or the bifluoride is extremely dangerous. HF vapor quickly destroys lung tissue causing death.
What is the density (baumé) of your flux solution (in water)? Or do you even use an ammonium chloride/zinc chloride flux solution?
In the USA most galvanizers are "dry" kettle. For your product a
"wet" kettle may be more appropriate, and likely would produce an acceptable product.
Regards,
Galvanizing Consultant - Hot Springs, South Dakota, USA
Second of two simultaneous responses -- September 2, 2008
Hello Manjeet,
I hope the temperature you quoted was an error - perhaps you meant to type 450 degrees C, not 550.
If you have sand on the surface of the SG castings, then you must have the foundry shot-blast or grit-blast them properly before you try to galvanize them. You must have a clean metal surface.
In reality, there should not be any moulding sand adhering to the castings. This alloy is cast at 1400-1450 degrees C which is a low temperature for ferrous alloys, and there is no problem having moulding sand which is quite resistant to the alloy at that temperature.
But it is a sad fact that some foundries do not control the quality of their moulding sand properly, in which case some sand may be fused onto the surface of the casting and have to be removed by grinding because shot- or grit-blasting is not strong enough to clean the surface.
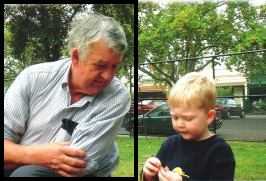
Bill Reynolds [deceased]
consultant metallurgist - Ballarat, Victoria, Australia
We sadly relate the news that Bill passed away on Jan. 29, 2010.
September 4, 2008
Dear Sir,
Thank you for your responses. If HF is that dangerous we can't use it as it could cause a great problem if some one dies of that.
We have got a sample ready after reading your suggestions. My customer is demanding 700 hours salt spray on that s.g iron product.
I think I have three options
1. Hot - Dip galvanising
2. Zn-Ni plating with passivation
3. Spraying with magni coatings.
Which one do you suggest to be most economical?
Regards,
- India
Hi, Manjeet. Electroplating is usually more economical than galvanizing or dip-spin coating, but 700 hours salt spray is a lot! Further, it can be very difficult to electroplate castings; you must try an acid-based zinc-nickel rather than an alkaline one.
Regards,
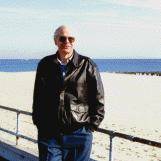
Ted Mooney, P.E.
Striving to live Aloha
(Ted can offer longterm or instant help)
finishing.com - Pine Beach, New Jersey
September 4, 2008

Q, A, or Comment on THIS thread -or- Start a NEW Thread