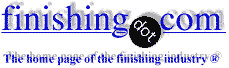
-----
Particles underneath the e-coat: Problems & Solutions
Q. We have been sending tubular mild steel that has been welded together for some time now and we have a constant problem of receiving it back with a number of the units having splotchy particle marks beneath the e-coat. They are very small little bumps that give the appearance of air bubbles. They can cover the entire unit, not just around welded joints where splatter may have occurred or oil dried from the metal. The coater says it is oxidation or rust formation and that anything beneath the surface of the e-coat indicates there was a problem with the incoming materials, not an e-coating problem. We have tried using a rust inhibitor and there was no improvement or maybe even worse.
Anybody got any answers ?
supplier - Warrenton, Georgia, USA
August 19, 2008
![]() |
A. Howard: Mohali, Punjab, India A. Particles in an e-coat are usually due to poor filtration of the e-coat liquid. However, if you have gas bubbles trapped under the coating, this could be due to using to higher voltage and inadequate solution movement in the coating process. Blistering can also occur when the part is baked too quickly or at too higher temperature. I would suggest you talk with your supplier about it. ![]() Trevor Crichton R&D practical scientist Chesham, Bucks, UK |
Q. I am facing burrs / particles been sticking on the surface after CED coating.
How to solve this problem? I keep the environment clean, but have this problem happen.
engineering - Malaysia
Q. Dear sir,
Recently I face an "edges" problem after CED coating.
The edge appears somewhat uneven surface / scaling / burr .
Already nearly 1 month I try to solve it but no success.
I really feel down and really have no idea to solve it.
I hope sir that can do me a favor help me how to fix it. Thanks
plating shop employee - Penang, Malaysia
October 2, 2012
Q. Dear Sir,
I had face edges problem after CED coating.
The edges appear some kind like scaling/burr/uneven surface.
This problem already make me struggling one and half month.
And I no have an idea to solve it.
Hopefully can get the answer or feedback from all CED coating professionals.
Thanks.
plating shop employee - Penang, Malaysia
October 14, 2012
Q. How to solve the edges problem after CED coating?
I had faced the edge problem during CED coating.
The edge of frame coating appears uneven, or small burr/scaling appear on the edge.
Kindly the CED expert can help me settle this problem. Thanks.
engineering & supplies - Penang, Malaysia
November 29, 2012
A. Dear Alfred,
Maybe your operating voltage is too high or phosphating is too thick. Try working with both these parameters one at a time and see which works.
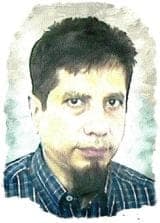
Khozem Vahaanwala
Saify Ind

Bengaluru, Karnataka, India
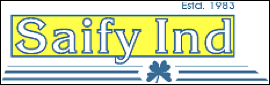
December 28, 2012
Q. My existing voltage is 85 volts and 2 minutes for coating...
so I need to reduce to how many volts?
- Penang, Malaysia
January 1, 2013
A. 85 volts is not high in my experience; however you might want to increase time up to 3 minutes with the same voltage and check for results.
Are you sure your phosphating is done really well, no rough grains, no sludge sticking to the edges, phosphating solution filtered crystal clean, fresh activation bath every second or third day?
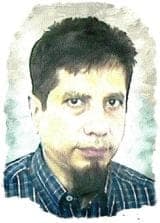
Khozem Vahaanwala
Saify Ind

Bengaluru, Karnataka, India
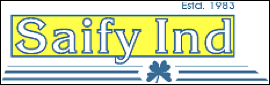
January 4, 2013
Q. Sir, may I know what you mean phosphating high?
Does CED coating have phosphate?
- Penang, Malaysia
January 4, 2013
A. Hi Alfred. Sorry that there is perhaps a bit of a language problem, but nobody said the "phosphating high". Someone did suggest that the phosphating might be too thick or heavy, as well as suggesting that the voltage might be too high -- but the suggestion of the voltage possibly being too high was before you told us what it was :-)
What are you doing for pretreatment, i.e., what do you do to the parts before they enter the CED tank? I think you need to spend some time describing what you are doing, perhaps send photographs, because 3-1/2 months later we're still not quite understanding your questions :-(
Regards,
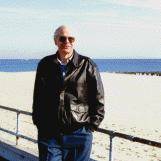
Ted Mooney, P.E.
Striving to live Aloha
(Ted can offer longterm or instant help)
finishing.com - Pine Beach, New Jersey
Q. Sir, see the arrow pointed area.
- Penang, Malaysia
January 4, 2013
A. Hi Alfred. I think you're repeating the question without giving us additional data to try to help you.
Maybe you feel that this problem has just one possible cause and that by describing one incidence of it we should lead you to that single cause, but it usually doesn't work that way. Every cough isn't lung cancer, nor every belly ache appendicitis ... there is more than one possible cause for roughness along an edge.
We don't know whether the article is made of steel or aluminum (or something else).
We don't know whether you chromate it or phosphate it, or something else.
We don't know if it happens on every part, or just on one part out of a hundred.
We don't know if it's a new problem and you used to successfully e-coat, or whether you've never yet achieved success.
We don't know if it happens on top edges, bottom edges, or vertical edges, or everywhere on the part; we don't know if it happens on the topmost row of parts on the rack or the bottommost, or everywhere.
Are you sure that there are no burrs before the parts enters the e-coat tank? Thanks!
Good luck.
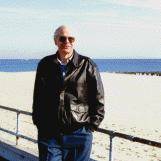
Ted Mooney, P.E.
Striving to live Aloha
(Ted can offer longterm or instant help)
finishing.com - Pine Beach, New Jersey
January 28, 2013
Q. Sorry if my language is poor.
Our part material is stainless steel; we have several models of stainless steel parts. Thickness is between 0.1 mm to 0.15 mm. 1 strip has 4 pieces. This edge problem appears since August 2012; before that there was no such edges problem. Usually we're hanging the part vertically, one time hanging about 42 strips, 2 strips in 1 row. And normally, the edges problem occurs at upper and lower sides, and it happened edge problem all jigs or 80% of the jig. They confirmed is not a burr.
Last, not all model have this happen, but existing 2 models have this problem.
- Penang, Malaysia
January 30, 2013
A. Hi again, Alfred. If some models come out fine, it sounds very unlikely that there is a chemistry problem in your CED tank, assuming those other parts are stainless steel as well. I suspect that the other models which coat properly do not have quite the same sharp edge. Even the vertical edge of this part may be different if it doesn't have the problem. Unfortunately, we're not helping you much.
What process do you do immediately before electrocoating? Is it zinc phosphatization? Phosphating of stainless steel is problematic. I would suggest you try blasting a couple of samples before CED coating and tell us what happens at the edge in this case. Good luck.
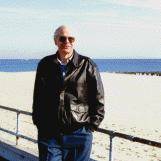
Ted Mooney, P.E.
Striving to live Aloha
(Ted can offer longterm or instant help)
finishing.com - Pine Beach, New Jersey
Q, A, or Comment on THIS thread -or- Start a NEW Thread