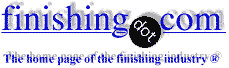
-----
Durability of Bright Dip anodizing vs Chrome Plating
Q. I am starting a new company that will manufacture motorcycle grips. These are made of 6061 aluminum. I am looking for a bright and durable finish.
How durable is Bright Dip Anodizing versus Chrome Plating in an environment where they are handled on a daily basis? Are there any other options available?
Cost is not a concern.
Thank You.
Product Desinger/Manufacturer - Lincolnton, North Carolina
August 10, 2008
A. Hi, Dave. If cost is not a concern, make them out of brass and chrome plate them :-)
Top quality chrome plating is a fabulous finish. Bright dip and anodize is a nice finish but it will be "white" whereas chrome is warmer and bluer. To my eye, aluminum, no matter how well done, looks cheaper. You might have some samples of each made and ask a few potential customers if they agree or disagree with my prejudice.
Since fingers are going to be on them, consider knurling them in some fashion so fingerprints will be less obvious than on flat expanses.
Regards,
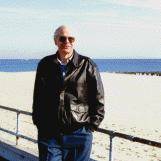
Ted Mooney, P.E.
Striving to live Aloha
(Ted can offer longterm or instant help)
finishing.com - Pine Beach, New Jersey
August 12, 2008
A. Never a truer word! Nothing beats Chrome, I'd like to suggest Glass Bead Blasting as another option to knurling, it looks awesome after plating.
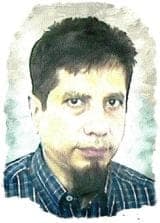
Khozem Vahaanwala
Saify Ind

Bengaluru, Karnataka, India
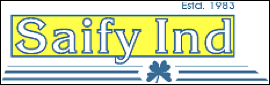
October 7, 2008
Anodizing or Chrome Plating? Need expert help
September 12, 2018Q. Hi there,
I am a bit of an amateur/hobbyist and I have tried to search to the end of the internet, but haven't been able to find an answer to this question.
I am making an Aluminium 6061 body that needs to be "coated" with a non-stick/friction-free (as much as possible), corrosive resistant process, that can handle isopropyl alcohol and getting banged up a little.
Being able to be resistant to being dropped from a table on wood floor or concrete and keep its appearance over time, even though it has taken some "hits".
I am either looking into Chrome Plating or Type 3 Anodising. I would prefer to use the Chrome Plating purely because of aesthetics, but I am worried about the plating would get chipped over time and leave the aluminum underneath exposed to corrosion.
What do you guys think?
I do apologize if my terminology isn't on point and if I have left any factors out; I am not expert (yet) :-)
/Klaus
Hobbyist - Hamburg, Germany
A. Hi Klaus. If knocking it onto a concrete floor is going to be a reasonable expectation, it probably should be made of hardened steel, which won't dent, or of brass, which still looks classic even with scratches and scrapes in the plating :-)
But if it's to be made of aluminum, I'd suggest anodized aluminum, possibly infused with teflon for low friction. Chrome is a beautiful finish but it's cathodic to aluminum, so galvanic action will cause the aluminum to corrode if the chrome is scratched through and any aluminum is exposed. Plus, although we should always expect and demand quality, robust chrome plating of aluminum isn't easy and doesn't look much different from poor chrome plating early on.
Regards,
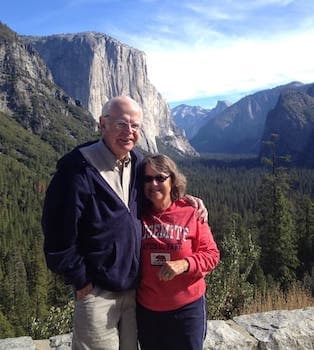
Ted Mooney, P.E. RET
Striving to live Aloha
(Ted can offer longterm or instant help)
finishing.com - Pine Beach, New Jersey
September 2018
A. Hi Klaus
For the case described, I would prefer Type 3 anodization (hard anodization). Chrome plating is not ideal for adhesion. And if damaged, the anodization behaves better.
Would recommend hard anodisation with PTFE (better gliding properties), layer thickness about 45 µm.
Base material EN AW-6061 or EN AW-6082 is equivalent (6082 is more available in Europe).
AluSolutions - Hallau, SH, Switzerland
September 21, 2018
Q. Thank you so much Ted and Jeorg for your answers.
I think a Teflon infused anodizing is the way to go.
My second question is: if I want to go all the way with this product and die cast it with Aluminium, will the silica prevent me to anodize in after processing?
Looking forward to your answers.
- Hamburg, Germany
September 24, 2018
(to help readers better understand the Q&A's)
Please see our Intro to Anodizing for an introduction to "Type".
A. Hi. Diecast aluminum will invariably somewhat spoil the aesthetic appearance; it will be greyish, and probably mottled. But if that issue isn't overwhelming, most diecast can be anodized (if not Type III, at least "Type 2-1/2"). I am not sure, however, about Teflon infused type 2-1/2. A shop which offers that should probably be consulted before considering diecast.
Regards,
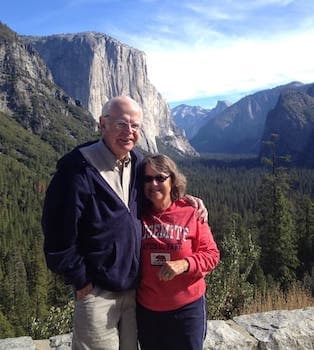
Ted Mooney, P.E. RET
Striving to live Aloha
(Ted can offer longterm or instant help)
finishing.com - Pine Beach, New Jersey
A. Hi Klaus
A good quality for type 3 hard anodization are not suitable in the typical casting alloys. There is no uniform thickness. The layer is also rougher. Standard anodization (Eloxal) does not have the same quality in terms of hardness and friction / gliding. The best results are with rolled or extrusion material 6061/6082.
AluSolutions - Hallau, SH, Switzerland
September 26, 2018
Q, A, or Comment on THIS thread -or- Start a NEW Thread