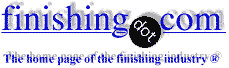
-----
EN plating on lead-free solder
Does anyone have experience or information about electroless nickel plating on tin-silver-copper lead-free solder? We're having adhesions problems after thermal excursion to about 250 C. This process is being done by a vendor for our China facility so I'm afraid I'm short on details---I'm assuming the vendor is doing double zincate and the EN is mid-range phosphorous. The plating substrate surrounding the solder is 110 copper and adhesion is fine on the copper; blisters are only seen on the SAC solder. Is there a different activation chemistry our vendor should use instead of zincate? Is this mix of substrate materials a non-starter? I'd appreciate any comments or suggestions.
Vern RieckProcess engineer for manufacturer - Concord, NH, USA
August 11, 2008
Hi, Vern. I'm confused where double zincating enters the picture. You believe this is the activation process the vendor uses for the solder?
Regards,
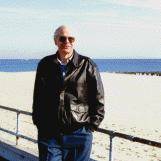
Ted Mooney, P.E.
Striving to live Aloha
(Ted can offer longterm or instant help)
finishing.com - Pine Beach, New Jersey
August 12, 2008
August 15, 2008
Hi Ted,
I'm not certain of their activation chemistry; I'm probably only displaying my lack of expertise. Our China facility says they have now solved the adhesion problem and describe the new vendor process like this:
1. Wiped the surface using cloth and ethanol
2. set the sample on a special equipment
3. double rinse
4. soap
5. double rinse
6. soap(high temperature
7. double rinse
8. Activation
9. double rinse
10. Activation
11. double rinse
12. alkali copper plated
13. triple rinse
14. soap
15. double rinse
16. washed by acid
17. rinse
18. nickel plated
19 final rinses and dry
This is a translation from the Chinese. I suspect the key element here is the copper strike; does that make sense?
On a practical level, I think the issue was that the first vendor didn't have any expertise with adhesion to the tin-silver-copper solder and they solved the problem by finding a vendor who knew what chemistry was needed.
thanks and regards,
manufacturer - Concord, NH, USA

Q, A, or Comment on THIS thread -or- Start a NEW Thread