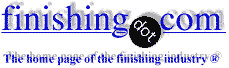
-----
Pitting on AL 6061 T6 die (tool)
We are seeing abnormal pitting on aluminum 6061 T6 (also 7075) dies (fixture). Our application is in mobile phone industry: using aluminum fixtures (CNC machined) to apply heat (190C) and pressure (15 to 20 psi) for about 8-10 seconds (two cycles per minute) to stainless steel parts (304 and electropolished). After about 2 weeks of operation (~ 8hours per day), pits develop on AL fixture creating cosmetic marks (defects) on SS 304. We tried alternate aluminum supplier and the problem is the same. We tried electroless Ni plating, but the same problem. After CNC, we polish the aluminum fixture using several grades of polishing brush to a mirror-like shine. The purpose is to smooth out the tiny circular marks created during CNC operation. Under microscope, the there is a crater around the pit.
Has anyone seen such issues? Material problem? Galvanic corrosion?
Thank you. Michael
Buyer - WBL, Minnesota, USA
July 31, 2008
I freely admit that this is not my area of expertise, but why are you using aluminum. It is so much softer than the metal that you are working with that it has to fail (as you saw with the EN coat).
James Watts- Navarre, Florida
August 1, 2008
August 12, 2008
Thank you for your comment, James. We have been using Al 6061/7075 for almost 7+ years for this application. The main reasons for using Al are easier to CNC and temperature control during the heat bonding operation.
We are also testing steel (same as the ones used in injection mold making).
We have not seen this much inclusion on Al made heating tools before.
- WBL, Minnesota, USA
A huge difference between 6061 and 7075 Al.
If you have not had a problem for ~7 years with Al, I would have to guess that the difference is the heat treat status when you initially machined the block. The daily heat cycle should be doing basically the same as an artificial aging.
Another thought, Some of the metals that come from offshore are not of the same quality as that made in the USA. Unfortunately, some companies in the USA import material and sell it as their own.
I would get a guaranteed made in the USA block and try again.
Also, how thick was the EN. I would have specked 0.0015" with a 4 hour bake at 400 °F.
Another thought, has your polish step changed in any way? Material used, people doing it or ?
- Navarre, Florida
August 13, 2008
Q, A, or Comment on THIS thread -or- Start a NEW Thread