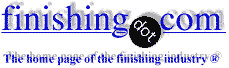
-----
Optimal corrosion resistance for powdercoat on outdoor application
We manufacture a mailbox which is sold nationwide, and roughly a year ago we transitioned from a local business to selling nationwide, both online and through several retail outlets. As a result our sales have drastically increased, and as a result we have been presented with several problems in our product which our previously limited marked did not show us.
The issue which on which I am seeking advice is corrosion. The units are constructed of 14 ga CRS steel with a sealed galvanneal treatment. The unit is primarily welded construction, and as a result there are portions of the box where the galvanneal protection is either burned away by the welding or ground off during subsequent cleanup. This is unfortunately unavoidable considering our fabrication methods. In the past we have used a single step spray clean/phosphatize solution, spray rinse, and then apply the finish coat directly to the galvanneal/bare steel surface of the part. I have since learned that this process is far from optimal, and I have been tasked with finding a cost-effective method of pretreat and/or coating the material to achieve a minimum 5 year corrosion protection. I know that there are many phosphating methods, 2,3,5,7/8 step processes are all commonly discussed, but I am looking for more details on these methods; primarily the effect of each step on the substrate, so that I can better judge how far we need to go in order to achieve our intended goal.
The second part of this question is about primers. We are going to begin using an epoxy primer on the part, and would like to use a powder primer rather than a wet primer, but our concern there is the flow characteristics of the primer. Our unit has several welded overlaps and T and butt joints which are not fully welded, resulting in minor gaps between sections. We are concerned that the powder primer will not be as effective in penetrating those areas, resulting in more material which is uncoated.
An additional question I have regards the process of Parkerizing. I have done some research into this process and it seems that it is chemically similar to standard phosphating, but with an electric component added. We currently do several electro-chemical finishing processes for aluminum, such as anodize, so we generally understand electro-chemical processes, but I would be interested to know more on the specifics of Parkerizing, and whether it would be an effective pre-treat for powder coating.
I apologize for the length of this post, but I have attempted to be as specific as possible without jeopardizing our company and product, also considering my limited knowledge of finishing. Any books, forums or other resources on these topics would be greatly appreciated, in addition to any information that the editors/moderators of this site or its readers would be willing to respond with.
Thank you.
sheet metal manufacturing manager/product developer - Vista, California, USA
July 17, 2008
How about trying a zinc rich powder primer then a polyester powder top coat.
Epoxy has good chemical resistance, but why would you think it'd make a good primer especially where you want corrosion protection.
There are two main ways to prevent corrosion. Barrier (e.g., powder), and electrolytic (e.g., zinc).
Your galvanneal is a very thin zinc coating which gives electrolytic corrosion protection (except where you burn it off by welding). A zinc rich powder primer would contribute some electrolytic protection along with the barrier of it and the top coat.
Hot dip galvanizing after fabrication is a possibility, but beware possible distortion in sheet metal. (You could try a couple to test that). HDG would be the ultimate in corrosion protection followed by powdercoating for colour.
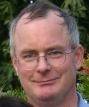
Geoff Crowley
Crithwood Ltd.
Westfield, Scotland, UK
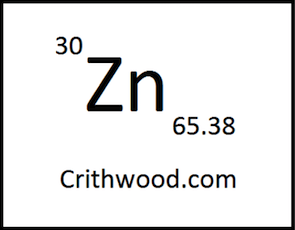
Dear Cody,
I am situated in the UK and have requested your contact information from finishing.com to enable me to contact you direct to offer visual supporting evidence.
Galvanneal is a name given to CRS steel sealed with a zinc/iron coating. There are numerous processing and performance considerations to be taken into account before choosing which grade/film weight of galvanneal would be ideal for your requirements. A good start to understanding the requirements of powder coated galvanneal could be to type "galvinfonote" into Google. However, two very good articles from that source worthy of your evaluation are:
http://www.galvinfo.com/ginotes/GalvInfoNote_1_3.pdf
http://www.metalmax.com/documents/FAQ%20PDf/18%20Surface%20trtmnts%20CTD%20LO.pdf
Another article that may be of interest may be this one I found on the web. Unfortunately, to download the full text the article will cost you $7.00.
It reads:
Metal fabricator succeeds at powder coating galvanneal panels after years of trial and error.
In an attempt to keep a major customer satisfied, a metal fabricator searches for a method to apply powder to galvannealed air-conditioner panels. The quest exacts a toll in reject costs and compels the company to educate itself in the art of powder coating.
http://www.pcoating.com/Content/getArticle.aspx?ItemID=9be14936-10ec-447c-a7df-62c1f63df274&Subject=Markets-specific
My understanding is that galvanneal requires over-coating as soon as possible due to some colour change (browning)and is due to atmospheric attack on the iron portion of the galvanneal coating. This is only a cosmetic failure and does not affect the substrate metals weathering performance in anyway. dependent upon the grade of galvanneal used, cracking of the Zn/Fe can take place when bending the galvannealed metal and choosing the correct grade of galvanneal can control this.
Your second question re primers -- the so called "zinc rich powder primers" are offered as a material that will protect mild steel substrates resulting in outstanding weathering performance. I am unsure how they perform on welded overlaps (bridging) and possibly a liquid primer may result in better performance.
Regarding the process of Parkerizing, I have some reserves concerning the use of such a process due to the zinc and iron content of the galvanneal coating. Not being an expert in this field, I would first investigate the possible cross contamination of the tank solution due to the electro-chemical chemistry of the process.
I hope that you may find this helpful in your evaluation of powder coated galvaneal.
Regards,
Birmingham, United Kingdom
![]() |
There is no major problem with powdercoating galvanneal. ![]() Geoff Crowley Crithwood Ltd. Westfield, Scotland, UK ![]() Regarding zinc-rich primers, our environmental restrictions are very tight, and we would like to avoid a zinc-rich primer if possible so as to avoid the fees which it would incur. If this proves to be the only solution then we will of course adopt it, but we are hoping for an alternative. - Vista, California, USA |
A. Think I didn't make it clear that the zinc rich primer I was suggesting is a powder.
This means 2 coats of powdercoating, the first the zinc rich one, and a second polyester top coat.
Can't see why a zinc rich powder primer could be considered an environmental issue. There's no VOC's, little waste, some energy consumed, but less than with solvent base paints.
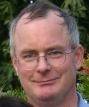
Geoff Crowley
Crithwood Ltd.
Westfield, Scotland, UK
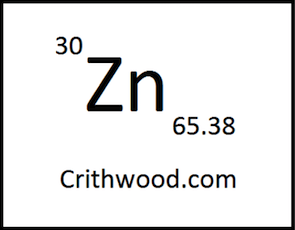
July 22, 2008
Q, A, or Comment on THIS thread -or- Start a NEW Thread