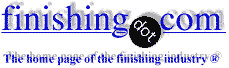
-----
Aluminum parts impossible to separate after service
I have a situation where two tight fitting aluminum parts (one is A356 cast aluminum, and the other is 6061), held together by a 304 stainless steel lock ring, are corroded together, and are extremely difficult, if not impossible to separate. The parts are used on transit busses, so there is severe exposure to the elements, road grime and debris, salt, etc. I am sure there is galvanic corrosion as well, since the two parts are held together by the stainless steel retaining ring (hence the two dissimilar materials). I have tried numerous penetrants, lubricants, processes with no real success. The only success we've had (but only about 20% success rate) is using steam, which seems to heat up and loosen up the parts and soften the grime and debris. In addition to steam, does anyone have any suggestions on what (relatively safe!) chemical or cleaning agents would help dissolve and loosen the dirt, debris and corrosion? Thanks in advance!
Don HughesManufacturing Engineer - Salem, VA, USA
July 8, 2008
Hi, Don. I once had an aluminum key I called "Excalibur". We had had a new garage door installed, and some genius designer had decided that money could be saved by making some internal parts of the lock out of aluminum instead of brass. My wife immediately had a spare key made, and she tested it before reading the note that only brass keys should be used. The door wasn't 20 minutes old before it was damned to spend its lifetime with that key eternally in the lock; no corrosion was needed to bind it there.
Get the designers to fix this mis-design. You simply can't put uncoated tight fitting aluminum parts together because they never come apart. Your 20 percent success rate is something to be proud of :-)
Regards,
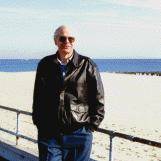
Ted Mooney, P.E.
Striving to live Aloha
(Ted can offer longterm or instant help)
finishing.com - Pine Beach, New Jersey
July 10, 2008
Unfortunately, aluminum conducts heat very well, but you might try the reverse of shrink fit. IE, heat the outer member with a heat lamp or steam or? and then cool the inner member with dry ice. Then try to get it apart. Possibly, heat on the outside at the same time as the dry ice for maximum expansion/shrinkage. It might take two or three tries. You could hod the dry ice with a rag that is wet with any kind of alcohol, methanol [affil link] is cheap, for even greater level of cold. You will need the cloth gloves with the rubber on the outside to not injure your hands.
James Watts- Navarre, Florida
July 11, 2008
July 14, 2008
Thanks Ted,
The two components are actually anodized, but apparently this treatment does not help ward off any corrosion. I have been in contact with a few labs and it appears Nitric Acid is my best bet to dissolve the aluminum corrosion without dmaging the parent metals
(both alum & st.st.). Only thing is I will have to re-anodize after separating, which may not be a bad idea. I am also looking at two alternatives for new assemblies:
1) Use an addtional hand-applied metal sealer to be applied to the aluminum before assembly, to prohibit corrosion further.
2) Try to convince engineering to completely change the design to eliminate the st.st. retainer and seal off the joint thus pohibiting the ingress of moisture and contamination.
Any experience out there with hand applied metal sealer? (Loctite Maxi-Coat, Coricone 1700, etc.)
- Salem, VA, USA
Aluminium can cold weld.
Try this. Clean two pieces of Al bar with a wire brush. Put the clean surfaces together (quickly before the oxide film re-forms)and hit the assembly hard with a heave hammer.
Your parts were probably unusually clean before they were assembled. I doubt if you will shift them now. Heating will probably improve the bond.
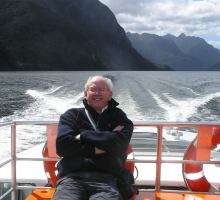
Geoff Smith
Hampshire, England
July 15, 2008
Q, A, or Comment on THIS thread -or- Start a NEW Thread