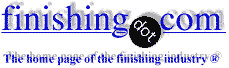
-----
Concentrators vs Tower Systems vs Rotary Style valve systems vs Catalyst systems: Which is best?
July 6, 2008
Hi, my name is Russ Friend. As an experienced controls guy I've had the pleasure of working on all of these systems. Many of you will be facing a daunting task of abating voc laden air, and are curious as to which system would be ideal. Here's a brief summary on the different types. Pros/Cons.
Catalyst: Because of platinum coated media they are able to run at a lower temperature. However they have lousy thermal efficiency and the media is extremely expensive to replace. Media can be baked out, however it is difficult. New media costs is prohibitive. In my opinion I would advice staying away from these systems. Their thermal efficiency is quite poor, and unless the heat can be recycled it is wasted.
Rotary Valve Systems: These systems can obtain 99%+ destruction rate efficiency. However they are prone to catastrophic failures/maintenance every few years. They were originally designed to be disposable units. As such they are a cost effective short term solution, but have a lot of hidden long term costs. Their biggest plus is that they can achieve self sustain easier than the tower systems, however this can also be difficult to control if a dilution damper routine isn't a part of the original installation. Power outages can result in the stack effect occurring. If it occurs for more than a few hours catastrophic damage is likely to occur unless the valve is manually rotated. Unfortunately I've seen this many times. These issues can be addressed with some minor system modifications. However the wearing of the rotor is inevitable.
The media is easy to clean via wash downs and bake outs. However due to the valve design bake outs are not as effective on this unit as they are on a tower system. Plus many of the systems include pneumatic cylinders which are a hidden long term cost. They require yearly replacement (ideally), and consume a large amount of hidden utilities due to the nature of compressed air.
Tower Systems: The most robust units out there. I'm currently working on systems that are almost 20 years old and they're still achieving
99% destruction rate efficiency. These units do have a large footprint, and a fairly high up front cost. However they are the most durable systems in the long run. Systems larger than 2 towers can achieve 99% destruction rate efficiency. Some two tower systems, with poppet valves, can also achieve this, but the long term energy costs of poppet valves is much higher than a comparable hydraulic valve
(compressed air is 8X more expensive than electric). On top of which poppet valves are inferior. Typically 2 tower hydraulic valve systems can easily obtain 96-97%DRE.
Understanding these systems does take time. I just made some modifications on some systems that are 13 and 19 years old. They were never 'tweaked out.' This tweaking has saved the client over $363,000 a year in utility costs, while simultaneously allowing them to add sources to a system that had been 'maxed out.' The client had been happy with their performance (both obtained a 99% dre in their most recent tests), and is even more pleased with them today.
The media is easy to maintain via wash downs and bake outs. Bake outs are most effective on these systems and can yield gains of over 7"WC differential across the bed. I've seen block that is eight years old that looks brand new because of a bake out.
For the rotary valve and tower system the two typical types of media used are structured block and ceramic saddle. Structured block has a lower differential pressure which means you'll get more from your fan. It's also much easier to maintain, as a bake out can bring it back to like new condition. However it does require some considerations in regards to warming up the chamber. The system must initially, from a cold start, be brought gradually to operating set point. However once the block has been soaked this can be modified with good programming.
Ceramic saddle is a cheaper alternative the structured block. However the differential pressure is higher, which means that more of the fan will be used to overcome the media rather than remove air from the plant. It is more difficult to maintain and if the plugging is extensive bake outs and wash downs will not be able to clean the media. It is common to replace the media. It does not require a ramp rate like the structured block. But due to its decreased thermal efficiency it does consume more natural gas.
For SLA containing metals and silicon ceramic saddle would be the best way to go, as it is much cheaper to replace than structured block. For most other application structured block is a great long term solution.
Concentrators: While it is true that they use much less gas than a rotary or tower system, they still require one of these units in order to work. They typically also require heat exchangers, and their push through design ensures that the fan does need regular servicing. Instead of ceramic media they typically use carbon or zeolite. Some have carbon filters before the main wheel to act as a filter. They are capable of consistently achieving 95% destruction rate efficiency. The media is difficult to clean, and while they do save utility consumption themselves the require some type of oxidizer as well. Are capable of catching on fire, and are difficult to maintain because they require maintenance personnel to enter into a confined space only when the unit is out of production (most of the working parts are internal). They also require a minimum of one full rotation before they can go online, which can greatly extend the effects of a power sag by costing the company production time.
consultant - Alliance, Ohio, U.S.A.
Q, A, or Comment on THIS thread -or- Start a NEW Thread