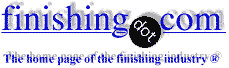
-----
Nickel tarnishing in LCD area of brass metal sheet bucket
We have been shipping this product to one of our clients who complained about the tarnishing of nickel inside the bucket LCD area. We have done 5 micron direct nickel on the brass sheet.
Please advise how this problem can be rectified.
Product Designer - Delhi
June 11, 2008
A thicker coat of nickel is required as the zinc is migrating thru the nickel in that area and forming an intermetallic alloy. Your nickel layer is thin there because it is a LCD. You can try a heavier plate which at the price of nickel now is not a great idea if this is a long term project. The only other way is to use aux anodes to get a better throw in that area. This is expensive in the short term.
James Watts- Navarre, Florida
June 12, 2008
I do agree with James Watts on his comments. As you may know, the higher the current density, the higher the variance in thickness distribution. The same goes for temperature, ph, metal and Ni chloride concentrations. You could drop your current density by 25% and keep the ph on the low side. The lower current density will help you throw more metal in the LCD areas. It will take you more time to get your thickness, but it will take more time to re-work a rejected part. Good Luck!
Mark Bakerprocess engineer - Malone, New York
July 6, 2008
If practical, try conforming anodes to re-focus deposition onto the LCD areas
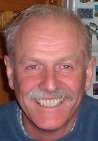
Trevor Crichton
R&D practical scientist
Chesham, Bucks, UK
July 8, 2008
try to do flash of electroless ni falowed by duplex ni this will reduce zinc migration and maintain ni bath purity to avoid zinc and cu deposition at LCD suresh
suresh reddy- Bangalore India
July 17, 2008
Q, A, or Comment on THIS thread -or- Start a NEW Thread