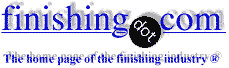
-----
Stripping Hardcoat or Anodized Coating on Aluminium
Q. I am Hardcoat Anodizing 6061-T6 Aluminium as per MIL-A-8625 / MIL-PRF-8625
[⇦ this spec on DLA], Type III, Class 1. Thickness range 80 to 100 microns.
Whenever I have to 'rework' my jobs, I have to strip the coating and machine the parts to clean up the surface and anodize again. My problem is that when I strip the coating, the job is getting undersize as there is no proper data with me on the solution concentration.
I am presently using a proprietary Alu-Deoxidiser 40% strength (which is apparently a combination of Phosphoric and other acids) -- immersion for about 10 minutes to get the coating off.
hard anodizing facility owner - Belgaum, Karnataka, India
June 10, 2008
A. Hi, Ravi. Sorry, but I don't think you have quite identified the problem. Anodizing is not a coating that is put on top of the aluminum; rather it is a coating that is composed partially of the aluminum in your component. To build an anodized coating of 80 to 100 microns of aluminum oxide consumes about 40 to 50 microns of aluminum. Even if your stripping solution is operating perfectly and does not remove any raw aluminum, the part will be 40 to 50 microns smaller after anodizing and stripping stripping than it was at the start.
Regards,
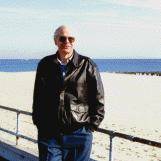
Ted Mooney, P.E.
Striving to live Aloha
(Ted can offer longterm or instant help)
finishing.com - Pine Beach, New Jersey
June 10, 2008
June 12, 2008
Dear Ted,
Sorry, for referring to anodic layer as coating. Let me redefine the problem.
My drawing gives me tolerances only for machined dimensions of the aluminium plate. After that it is Hard Anodised as per MIL-A-8625,Type III, Class 1 -- customer requests about 80 microns. If I get any defects like patches or small dents on job, I have to rework, which entails having to strip the layer until it exposes the Aluminium (Our CNC machine inserts cannot cut through the anodic layer -- too expensive) and then rework the jobs on the CNC Lathe to the Lower Limit of the tolerances allowed and then Re-Anodise.
Thanks in advance for Kind Response.
In the last 12 hours have developed a workmanlike procedure which seems to be working, but would like a more qualified opinion.
I have made a 20% strength solution of my proprietary Alu-DeOxidiser Chemical in DM Water and a 5% NaOH solution in DM Water.I immerse the job for about 30 minutes in the De-Ox solution, take out, rinse and then use utensil scrub pad to scrub off the balance layer with caustic soda ⇦liquid caustic soda in bulk on
Amazon [affil link]
solution dip (only the pad not the job)! It seems to be bringing my dimensions back to the machined component stage. After that let us hope for the best!
Ravi
- Belgaum, Karnataka, India
Ravi, Hello.
Mil-A-8625 does mention about stripping anodize coating to check coating weight. If you are worried about the aluminium being attacked after the anodize coating has been stripped, you can use the phosphoric / chromic acid as recommended when stripping anodize coating to check coating weight.
Phosphoric acid - 35 ml/l
Chromic acid - 20 g/l
Temperature - 100 °C ± 6
Good Luck,
- Penang, Malaysia
June 16, 2008
July 11, 2014
Q. Hello,
I have seen this old post on this forum and I hope that you will be able to help me with my problem. What is the best possible option for removing anodized layer 5-15 microns bright finish from Al 99,9 MgSi EN AW-6401 T4 (F13).
We are currently using H2SO4 and we are removing a lot of base material.
Waiting for your support.
Thank you
Regards
Pawel
quality engineer - Mullingar, Westmeath, Ireland
Treatment &
Finishing of
Aluminium and
Its Alloys"
by Wernick, Pinner
& Sheasby
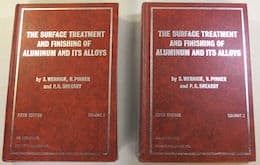
on eBay or Amazon
or AbeBooks
(affil link)
A. Hi Pawel. Actually, SK Cheah's posting is not outdated and remains, to the best of my knowledge, the best general way to strip any anodized coating from aluminum with no attack to the substrate. But Pinner & Sheasby proposes the possibility that for high copper, magnesium, or zinc alloys, replacing part of the phosphoric acid with boric acid might be an improvement. Best of luck.
Regards,
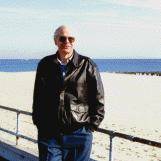
Ted Mooney, P.E.
Striving to live Aloha
(Ted can offer longterm or instant help)
finishing.com - Pine Beach, New Jersey
Q. How to rework the Anodized and dyed Aluminium parts? As of now I'm using caustic soda ⇦liquid caustic soda in bulk on Amazon [affil link] which can harm the hand of operator, kindly suggest any water based chemical which is ecofriendly as well.
Kapil BhardwajSurface Treatment - Delhi, India
September 14, 2017
A. Hi Kapil. An "ecofriendly" chemical which is capable of dissolving aluminum oxide strikes me as an oxymoron, although maybe someone disagrees.
But stripping with caustic soda is, in my experience, an "immersion" process rather than a scrubbing process, and operators exposed to chemicals should be wearing personnel protection equipment including rubber_gloves ... I'm not understanding how this chemical is reaching the hands of your operators -- please explain. Thanks!
Regards,
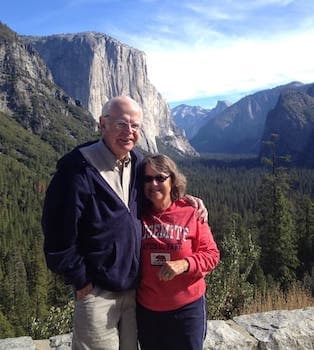
Ted Mooney, P.E. RET
Striving to live Aloha
(Ted can offer longterm or instant help)
finishing.com - Pine Beach, New Jersey
September 2017
Q. Yes, your are right, Sir, that it is a dipping process -- but still operators can make mistake of not wearing PPE's. I would request you to share a chemical which is water based and eco-friendly thus it is good for both operator, environment.
Thanks
- Delhi, India
September 21, 2017
Removing HardCoat Anodizing from a large part
Q. I have a project that we are doing that requires the removal of existing worn Hardcoat class III Anodizing that is coated on M1 Mold Aluminum ( class 5000 ). We have a large amount of these to do over the next 14 months and the timeline does not allow us to ship out for stripping. Is it possible to put together an effective tank and chemical bath solution to do this in-house. These parts are 12 feet long, so between freight, handling at the plating shop and timeline, it is not cost effective to do outside. Any help as to required equipment and the chemical solutions would be helpful.
Rich Przytarski- Winona, Minnesota
October 13, 2017
Q, A, or Comment on THIS thread -or- Start a NEW Thread
