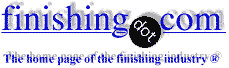
-----
Electroless nickel and dull nickel fail salt spray test
Q. WE are connector manufacturing company. WE REQUIRE 48 HRS SALT SPRAY TEST BUT FAILING AT 32 HRS. PEEL OFF & RED RUST DEPOSIT IN SOME AREAS. WE ARE USING MED PHOSPHOROUS FOR ELECTROLESS. & DULL NICKEL BATH OF NICKEL SULPHATE, SODIUM SULPHATE, BORIC AMMONIUM CHLORIDE. WE ARE PLATING ALUMINIUM AND CASTING PARTS FROM THESE TWO BATHS, CAN You THROW SOME LIGHT ON THIS TOPIC OR ANY PASSIVATION TO REACH FOR 48 HRS SALT SPRAY TEST.
THANKS,
K.M.BHATT
Dy. Manager - PUNE, MAHARASTRA, INDIA
May 25, 2008
A. Put a thicker coat of nickel on the parts.
James Watts- Navarre, Florida
May 28, 2008
Q. SIR,
We have done electroless nickel of 18 micron thickness on steel, but it's not withstanding salt spray even for 24 hours .
Kindly is there any method to improve corrosion resistance so as to withstand for 72 hours?
- Pondicherry, India
September 13, 2013
A. Hi M. S. Guru,
18 microns is not sufficient thickness for corrosion resistance, even for a high phosphorus solution. A minimum thickness of 25 microns of a greater than 10% phosphorus solution might just about do the job, but you should be looking at 50 microns realistically.
Aerospace - Yeovil, Somerset, UK
September 17, 2013
A. 25 microns is OK even for mid phosphorous. It has to give 96 hours in NSST. BUT, it has to be on a perfectly polished bright substrate. Otherwise you need a thicker deposit.
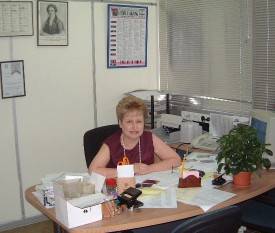

Sara Michaeli
Tel-Aviv-Yafo, Israel
October 31, 2013
Q, A, or Comment on THIS thread -or- Start a NEW Thread