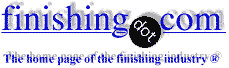
-----
Porosity of Silver Plating on Nickel/Brass
August 30, 2021
Q. I am a retired engineer with a life hobby as an amateur musician (euphonium).
I recently treated myself to an expensive new silver plated instrument which to my horror began to change colour almost
immediately.
I informed the supplier that silver plate is known to be porous and silver plate directly on brass was not a good idea. A base of copper or nickel should be considered.
Could you advise me which direction to take with this.
The instrument is still under warranty!
The supplier's first response was "Try cleaning it"
Regards
Ret. Mechanical Engineer. - altrincham, England
A. Hi David. I think you're right that brass ideally should have copper plating or nickel plating before the silver plating, but it's also true that silver tarnishes -- so it's difficult to say exactly what the cause of the change of color is. I think I'd ask the supplier for pretty specific cleaning instructions so they can't say that your cleaning was the problem ... then if it isn't restored to a silver color you can see what he warranty says.
I'm a bit surprised the supplier applied no anti-tarnish technology because there are several, but I don't think that I would lacquer the plating at least until the finish was no longer warrantied.
Luck & Regards,
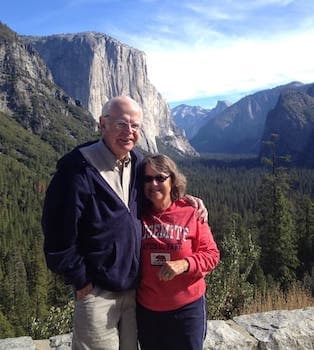
Ted Mooney, P.E. RET
Striving to live Aloha
(Ted can offer longterm or instant help)
finishing.com - Pine Beach, New Jersey
August 2021
⇩ Related postings, oldest first ⇩
May 16, 2008
Our company has historically used a silver-plated brass "pin"
(nominal diameter of 1.5 mm) as part of an electrochemical sensor. The base metal of 360 brass is coated with a barrier layer of nickel prior to a 0.001" electroplate of silver, conforming to the
QQ-S-365
[from DLA]
Type II, Grade B std.
The silver pin is chloridized with ferric chloride
⇦ on
eBay or
Amazon [affil link] to form a this layer of AgCl on the top of the pin to act as a chemical sensor (a silver/silver chloride electrode.)
We have been experiencing problems with our normally brown silver chloride coat turning white or off white with a concomitant formation of a wet film. Surface analysis by EDS and FTIR microscopy reveal zinc chloride and moisture on failed pins. We believe that either or both of the silver or nickel plated layers are porous, permitting the galvanic reduction of the AgCl by the zinc in the brass (and indeed we often, but not always, see a pit forming at the site of the defect.) This has been an ongoing problem which tends to rise and fall without much correlation to time or process conditions.
Brass was chosen as the base metal both for its hardness/machinability and its low conductivity, but we are not are not married to the notion of sticking with brass.
Can anyone provide any advice on mitigating this problem?
-Choice of base metal?
-Choice of barrier layer?
-tricks to getting a high density, low porosity plate?
(nickel or copper strike on brass prior to nickel plating? Silver strike prior
to silver plating?)
Many Thanks,
Don Cameron
end-user of plated part - Austin, Texas
Hey Don,
Cu and Ni strike baths are mainly used for adhesion values, not so much for improving porosity. As you probably know, strike or flash plating thicknesses are very low. The plater may have to put down more nickel on these parts. It sounds as if the barrier plate is insufficient. Have you also considered an acid copper plate under the nickel? That should help you as well. Good Luck!
Process Engineer - Syracuse, New York
May 22, 2008
To reduce porosity in silver it is very important to use a silver cyanide strike. The voltage of the strike is important. You want the silver to plate electrolytically and not immersion plate.
The brass base metal is OK but I would use at least a 2.5 micron thick copper strike on top of the brass followed by the silver strike and then the silver plate.
This process has been used successfully in the electronic industry where the parts are subjected to a 400 deg C bake and then looked at for blisters and discoloration. The parts had to be totally free of blisters and discoloration.
Be sure to use live entry for both the strike and the silver plate.
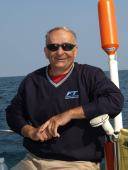
Pat Mentone
St Paul, Minnesota
May 30, 2008
June 3, 2008
Don, it sounds to me like you've got porous brass that is inadequately cleaned. That doesn't mean you've got a poor process, just a poor substrate. Brass can be very problematic to plate, depending on how it has been worked - casting is a big problem!
I think you are right in thinking the silver and nickel are porous, as this will account for the presence of zinc on the surface of the silver coating. The most common reason for porous coatings is a porous substrate that allows cleaner to be trapped in its surface and thereby prevents metal form being deposited into the pores. This is a common problem and one that can be relatively easily solved.
I would suggest either changing to a copper pin, or using a high throwing power cyanide copper bath on the brass to coat the small holes in the brass. Copper is much cheaper than silver to electrodeposit. I would suggest no less than 5 microns of copper and preferably a bit more (10-15 microns). You can then plate the workpiece with nickel and this will act as a barrier layer that will prevent any other coatings migrating into the brass or copper. This is especially important if you want to use the electrode at high temperatures.
An alternative could be to use aluminium as the substrate, but you will then have to alter your plating process to accommodate a zincate pretreatment and this may be problematic for you.
Finally, ferric chloride
⇦ on
eBay or
Amazon [affil link] is a pretty aggressive metal etchant - have you tried dipping the silver plated part in something les potent, such as hydrochloric acid? It may be beneficial to make the pin slightly anodic in the HCl to promote the chloride formation.
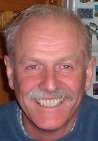
Trevor Crichton
R&D practical scientist
Chesham, Bucks, UK
Q, A, or Comment on THIS thread -or- Start a NEW Thread