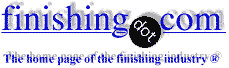
-----
Nickel plate, blistering when chromed
Dear sir Ted, greetings,I have problems chroming over watts nickel. substrate is steel and aluminum.it seems that whenever I plate chrome over nickel the nickel blisters and peel off along with the chrome. I observed proper pretreatments, I buff the nickel to shine before I chrome it for 3 to 4 minutes, 1 amp/sq.inch. I have a 2 phase rectifier. I also wonder if it is possible that my rectifier is contributing to the problem. thanks in advance.
Chris Sianstudent - Bacolod City, Philippines
May 14, 2008
May 15, 2008
Based on the small amount of information given, the chrome has a high internal stress, which is pulling the nickel under plate off of the parent metal because it has poor adhesion to the metal.
Your steel either has not been cleaned adequately, or is not properly activated.
On aluminum, you have to use a zincate before the nickel, and then it helps to use a proprietary alkaline electroless nickel as a strike before the regular nickel.
Polished nickel is not easy to get clean and activate, so I would have thought that the chrome was separating from the nickel.
- Navarre, Florida
Sir Watts, thank you for the information, though your answer is limited it helped a lot. my other problem is the misplating of chrome, 2min. of chroming plating seems short and cannot cover entirely. I really need your suggestion thanks
Chris Sian- Philippines
May 27, 2008
![]() |
May 27, 2008 Hi Chris, - Navarre, Florida hi , - Essex, UK May 28, 2008 |
dear sirs,
thank you for your helpful responses, your information was right, I started using HCl 30% concentrate, some steel doesn't react as fast as others so I leave it submerged for an hour until it darkens. then I dip it in deionized h20. then I dip it in watts nickel for an hour.( since I haven't made up a bright nickel solution yet). talking about bright nickel I tried saccharin and Thiourea
⇦ on
eBay
or
Amazon [affil link] mixed with watts nickel and in very high temperatures, around 60 °C the nickel plate seems to turn real bright but peels off by hand. but anyways I am still researching on how to make bright nickel and if you have any information that you can share, that would be a big help. this is a great site I have learned a lot from experts like you. Thank you and I am very grateful for your help.
- Philippines
June 30, 2008
A. Chris,
Clean your part in a caustic solution first, then rinse well then into the acid for about 5 minutes. 1 hour is mega too long and causes other problems.
Sacharin will brighten and harden nickel, but it takes an extremely tiny amount and then it causes such a huge internal stress that the nickel will actually flake off.
- Navarre, Florida
July 1, 2008
Q, A, or Comment on THIS thread -or- Start a NEW Thread