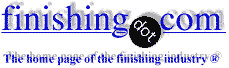
-----
Ni Plating thickness on Aluminum for solderability?
I'm interested in a recommendation for a min, max and nominal thickness requirement of Ni Phos. plating on Al. The plating is purely for solderability using Sn/Pb (63/37). Abrasion resistance is not an issue. The part being soldered to the Al is a piece of BeO metallized with thick film MoMn Ni Au. Also can you comment on the consequences of a too thin or too thick plating? Thank you in advance for your feedback.
Patrick ReichertLaser Development Engineer - Pleasanton CA USA
April 24, 2008
Hi, Patrick. If it's only for solderability I think you might want to consider tin plating instead :-)
Regards,
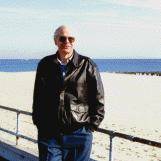
Ted Mooney, P.E.
Striving to live Aloha
(Ted can offer longterm or instant help)
finishing.com - Pine Beach, New Jersey
April 25, 2008
April 29, 2008
TED,
I JUST READ YOUR ANSWER AND WANT TO KNOW THE FOLLOWING REQRMNTS:
1. MY CUSTOMER WANTS ME TO DO PLATING ON MS - FIRSTLY COPPER, THEN NICKEL, AND THEN DULL TIN - WHICH I SUPPOSE IS SATIN TIN AS THE REQUIREMENT FOR THEM IS SOLDERABILITY.
2. PARTS ARE TO BE BARREL PLATED.
3. WE CONDUCTED FEW TRAILS USING GRWOEL SATIN TIN PROCESS BUT THEY FAILED IN SOLDERABILITY AND THE APPEARANCE TURNED SLIGHT BLACK AS WELL.
4. CAN YOU TELL ME THE BEST SOLUTION FOR THE SAME.
REGARDS.
- INDORE, MP, India
Thank you for the suggestion Ted. If Sn is not an option, can anyone provide any comment on my original question?
Pat
- Pleasanton, California, USA
May 1, 2008
.0001" Electroless nickel is sufficient for solderability. Greater thickness is fine but offers no advantage for soldering.
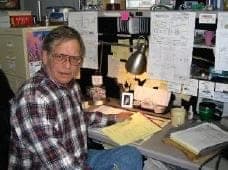
Jeffrey Holmes, CEF
Spartanburg, South Carolina
May 2, 2008
Thanks Jeff. We have recently conducted some in house testing on heatsinks with 0.0001"-0.00015" thick electroless Ni plating. These tests consisted of a bake at 400F for 1hr. followed by 40x inspection for blisters and a tape test using .004" thick Kapton tape. No blisters or peeling were observed. A solder wetting test was also performed with good results based on examination of the wetting angle. Thanks again for your input.
Patrick Reichert- Pleasanton, California, USA
May 14, 2008
You refer to "electroless nickel" as a single coating and this can be dangerous. In fact, there are dozens of "electroless nickels" available and the clearer this is for designers, the better it will for the industry. You should refer to ASTM B733 for clarification of which phosphorus level composition is best suited for solderability and if you've tested it, you should know which TYPE (i.e. phos level) you've tested and found acceptable. High phos is poorest for solderability but best for corrosion resistance. While low phos or electroless nickel-boron might be best suited for solderability application, they are very limited in availability compared to mid phos or high phos EN. If you want to ensure difficulty down the road, just specify "electroless nickel 0.0001-0.00015" thick", however, if you want to ensure consistent plating with repeatable solderability, at very least include a phosphorus level or callout out the appropriate ASTM designation. I'm sure your EN plater can assist you with this (or you've got the wrong plater!).

Milt Stevenson, Jr.
Plating shop technical manager - Syracuse, New York
May 18, 2008
3 to 5 microns of medium phosphorous is a good trial but if you can finish with a 2 microns of nickel sulfamate the solderability will be better
Ricardo BursteinBnei Berak, Israel
May 31, 2008
Q, A, or Comment on THIS thread -or- Start a NEW Thread