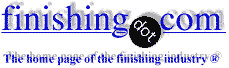
-----
HELP! Satin nickel finish doesn't match what we did last year
We're a custom architectural metal fabrication shop working on a satin finish nickel plated stair stringer, railing, and wall panels. In the beginning of this project, when we were discussing the finish with the architect, we showed them several samples we've got in our shop and they chose our "brushed nickel" sample. This sample was a piece of nickel plated cold-rolled steel that we'd then orbitally sanded with 220 to 320 grit paper, followed by an abrasive wool pad. So it was more like a "satin" in that to me "brushed" nickel has a grain to it.
We're now in the process of putting this finish on some of the parts for the stringer cladding and are having issues recreating this same finish. We think part of the problem is that the sample we had approved has naturally aged over the course of this project (we got this sample approved nearly a year ago). In addition to that, I believe the nickel plating on the sample happened several years ago, so that aged before we did the sanding last year. Now we're faced with trying to recreate this finish and are having problems making it "dull" or "satin" enough.
Our current process has been, in summary, as follows. Use P&O (pickled & oiled) steel panels that we've sanded to a fine satin orbital finish to remove any scratches, pits, and surface imperfections. We then have these panels nickel plated by our usual plating vendor. Then we run over the plating lightly with sandpaper (220, then 320) followed by the abrasive pad. Anybody have any suggestions on how to make this finish appear less reflective and shiny? We've tried applying wax to no avail. I've read several of your threads regarding the possibility of sand or bead blasting prior to plating, or using an additive in the nickel bath. I'm wondering though if there are any other suggestions?
One other thing, our plater has a dull matte nickel tank and a bright nickel tank. We'd have preferred to use the dull matte nickel tank. Unfortunately, we've had to use the bright nickel tank on all of our parts because a few of the rail sections are too big for the dull matte nickel tank (a bad case of catering to the lowest common denominator!).
Any suggestions are appreciated!
designer and project manager in custom architectural metal fabrication shop - Seattle, Washington, USA
April 15, 2008
June 9, 2008
Hello Carrie,
You have consider 3 parameters to produce the same final brushed effect :
- the mechanical satin : I believe it is right, you have a process with fixed parameters. But I think it is dangerous to brush with grain 240 or 320, it is very aggressive. I prefer to use scotch brite.
- The basic matte nickel and the bright nickel have not the same hardness : the bright nickel is harder so it more difficult to brush deeply and consequently have a matte effect
- The bright nickel thickness : the bright nickel has often a leveling effect : it clears the first brush realized onto the base material. So, more thickness gives more bright and less satin effect onto plated parts.
Some ideas to try:
- if you work with bright nickel, during the plating, try to reduce the thickness to reduce the leveling effect
- try to brush with orbital tool and scotch brite disk, it is less aggressive than sandpaper and it is right to matte surface without remove the complete thickness of the nickel plating
- expensive : re-plate the steel with matte nickel and re-brush
Hope it could help to you,
- Bordeaux, France
Q, A, or Comment on THIS thread -or- Start a NEW Thread