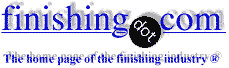
-----
Designing & Bracing Rectangular FRP Tanks
Q. We are manufacturing FRP tanks used for STP plants. Now I want to test the tank wall for deflection and maximum load it can withstand.How I can calculate the maximum load/force it can withstand. My tank capacity of 6000 ltrs of water.
Raja Munibathiran- Chennai, Tamilnadu, India
April 11, 2008
A. Hi, Raja. Sorry, I don't know what STP stands for in this case. Also, you haven't mentioned if this is a vertical round tank or horizontal round tank, or rectangular open-top tank. Bracing of rectangular plastic tanks is not a dirt-easy subject, but fortunately your tank doesn't sound too big. Please tell us the shape and dimensions of the tank, and the temperature and specific gravity of the STP and then someone can hopefully give you a starting point.
Regards,
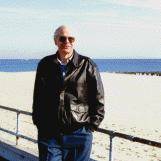
Ted Mooney, P.E.
Striving to live Aloha
(Ted can offer longterm or instant help)
finishing.com - Pine Beach, New Jersey
April 11, 2008
Q. Hi we are manufacturing FRP tanks of Rectangular open at top .The size of Tank is 2 x 1 x 2 meters. The capacity (water) of tank is 6000 ltrs. How to calculate the maximum load that the side wall of the tanks should withstand before damage, i.e., the maximum flexural load on tank walls?
Raja Munibathiran [returning]Product Designer - Chennai, Tamilnadu, India
April 14, 2008
(Many decades later the editor fondly remembers the 1st book I consulted after graduation from engineering school ... the book that took me from theory to real-world practice :-)
A. Hello again Raja. Although several strength of materials books address the issue of design of plates with "triangular" or "trapezoidal" loading like you get on an open top tank (because the pressure increases proportional to solution depth), the only book I've ever come across that addresses the question of design of rectangular tanks in an integrated manner is a terrific old book "Design of Weldments" by the Lincoln Arc Welding Foundation. I used it throughout my career, including as the basis for computer programs I sold to two manufacturers of plastic tanks for calculating required bracing. It's well worth hunting for!
For a tank this size, which is very "ordinary" for jobshop metal finishing, I doubt that you would want toe braces, but rather a rim and a couple of belly bands. You can roughly estimate tank loads, making approximations per that Blodgett book, or you can get it significantly closer with the method of two moments applied at each belly band, or you can do a finite element analysis although that didn't exist in my school days and I can't instruct about it. Some vendors have prepared "design books" or computer programs for modest sized tanks like this so each tank needn't be recalculated individually.
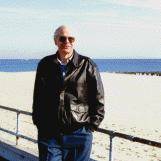
Ted Mooney, P.E.
Striving to live Aloha
(Ted can offer longterm or instant help)
finishing.com - Pine Beach, New Jersey
April 22, 2008
April 22, 2008
A. Hi Raja,
For these size of tanks, then, as Ted suggested, use a 'rim' or a top flange.
We used to use a belly band flange or an inverted 'V' reinforcer at 1/3 of the (full) tank height plus, of course, a top flange. For your given tank size, min. 2" if not more.
Where did we get the idea of that belly band height, I dinna ken.
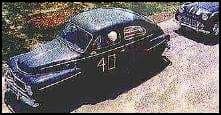
Freeman Newton [deceased]
(It is our sad duty to advise that Freeman passed away
April 21, 2012. R.I.P. old friend).
Remember that we're speaking of a fiberglass tank here, Freeman. Although its tensile strength is perhaps half the strength of steel, that's not the whole story. With steel tanks you can go with a small factor of safety because the plate is made (uniformly) by a mill, and we have more than a century of incredibly broad experience proving steel to be as strong and reliable as we think. But for fiberglass, laid up by craftspeople unknown to us, of unknown skill, who may wet the cloth not enough or too much, or may let air bubbles in, or may think it okay to have joints in the roving, you need a much larger factor of safety. I'd probably expect three belly bands; maybe only two if I knew and trusted the company and its craftspeople.
Raja, if you are an engineer, try the book I referenced. If not, remember that tanks must be designed by engineers. Good luck.
Regards,
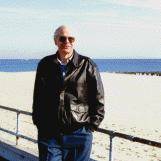
Ted Mooney, P.E.
Striving to live Aloha
(Ted can offer longterm or instant help)
finishing.com - Pine Beach, New Jersey
April 22, 2008
April 23, 2008
A. Hi again,
Well, Ted, we NEVER had an 'engineer' design our products ... JUST good, hard experience.
But you do raise one point I forgot ... that is the experience of the (unknown) fibreglass fabricators.
We'd use initially a matte then a woven roving or cloth, then mat again (always between reinforcing layers) and so on and finish with a 90% resin so-called finish matte layer.
I recall vividly that we, then a still existing Richmond Hill, Ontario plant had to face a Vancouver B.C. unionized workers who claimed that they, too, could weld plastics.
This was either Hooker Chemicals or Albright & Wilson.
We had made rigid PVC, no FRP, tanks with slots for the electrodes to high tolerances and made the welding in a controlled atmosphere.
I was given the task of checking out all welding which was done by an outside Company ... all weld pieces being made of 1/2" thick PVC, duly mitered.
Our best guy, a Swiss, hit the miraculous figure of l00%. Even German text books on welding said that this was rare but possible & had been done. Most guys hit over 90% of tensile -- then the union tests came in ... the best was 30%! Yes, thirty percent! YUCKS !
I know that this isn't FRP but it sure shows how well-trained thermoplastic welders can perform.
For those FRP tanks I'd assume a wall thickness of 3/l6" to 1/4" with the top flange @ 1/2" thick BUT properly laid up in accordance with Hoyle! Then we'd run a test with a tank being filled up to the brim ... and if undue deflection was noticed, ah, we'd add some more FRP.
FRP suffers, as you might well know, from permeation. Hence the PVC approach, often FRP'd ... and that Company is Alcore Fabricating who very successfully made the world's first dual laminate tanks ... and was commissioned to make Chlorate Tanks for Hooker down in Mississippi in around 1963 .... and I held the first paper on that design which is now called Dual Laminates.
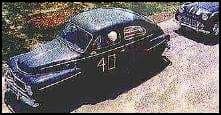
Freeman Newton [deceased]
(It is our sad duty to advise that Freeman passed away
April 21, 2012. R.I.P. old friend).
Q. Dear Raja,
would you please give me your FRP material type and composition such as the type of resin that you used and etc. Have you got some mechanical testing on your material? If yes please give us the mechanical strength of your produced FRP, then please let me know your tank design thickness. Thanks
Cheers
- Jakarta, Indonesia
September 16, 2010
A. Hi Yuli. For plating shop applications, corrosion resistance is important, and vinyl ester is probably the most universal resin for this purpose. Good luck.
Luck & Regards,
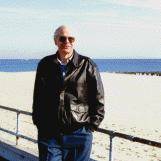
Ted Mooney, P.E.
Striving to live Aloha
(Ted can offer longterm or instant help)
finishing.com - Pine Beach, New Jersey
Q, A, or Comment on THIS thread -or- Start a NEW Thread