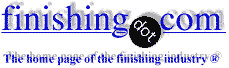
-----
Fuzzy Copper Electroforming
April 2, 2008
I'm a grad student at the Missouri University, I'm using an acid copper electroplating bath in an attempt to electro-form micro channels. I've been using my bath for about 3 weeks now and it had a very sudden unexplainable change in performance.
|
but that, I think, has more to do with the fact that I'm trying to electro-form without using a pulse power supply. I'm getting what appears to be dendritic growth (roundish lumps about 2 mm or smaller in diameter, after plating parts at about 20 ASF for ~15-20 hrs. Is that due to the long plating times? any other suggestion on how to get a thick layer (at least 250 um) that is smooth and uniform?
|
This figure shows the dendritic growth, and the channel structure that I
later coated with conductive ink one to which the fuzzy copper formed.
Anyways, on to my bigger question. I'll just explain what happened and see if anyone has any ideas. |
Attached to this I have a heating and filtering system. The heater is a stainless steel heater (in a PCV housing, I'm going to remove the heater as I don't use it). |
When I returned to examine the work piece it was covered with a very fine but sharp 'copper fuzz'. The fuzz was completely uniform and very attached to the work piece |
Next I plated a flat piece of copper to see if it too would turn fuzzy, the following pictures show, the results | |
|
|
So my questions are:
1. Is this common? has it been seen before?
2. If it is common what is causing it, and how can I purposefully make a bath chemistry that will produce similar results?
3. Also if anyone has time if you could comment on how to prevent the dendritic growth, describe in the first section and as seen in the first figure.
I would be VERY grateful of any help that anyone can provide.
Student / Research Engineer - Columbia, Missouri, USA
![]() |
Christopher, you may be better off shortening your submission - this is too long to take in at one go and not made any easier by having to go outside the website to see the pictures. I know I always ask for process and material details, so perhaps I have met my come-uppance! ![]() Trevor Crichton R&D practical scientist Chesham, Bucks, UK April 11, 2008 April 16, 2008
![]() Ted Mooney, P.E. Striving to live Aloha (Ted can offer longterm or instant help) finishing.com - Pine Beach, New Jersey |
A. Have you analyzed the bath to be certain copper and sulfuric concentration have not changed? Have you added additional addition agent to replace what has been consumed?
Sounds like low addition agent to me.
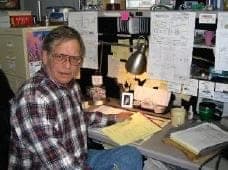
Jeffrey Holmes, CEF
Spartanburg, South Carolina
April 16, 2008
April 23, 2008
A. I will have to agree with Jeffrey Holmes. If you are going to plate for 18 - 24 hours at a time addition agents have to be added per so many ampere hours. See if the addition rate is being met. You are experiencing severe burning. Other possibilities to examine after the first recommendation is satisfied is as follows:
You will want to make sure the anode to cathode spacing is at least 4-6 inches consistently, and have ample solution agitation.
I don't quite understand your anode system, I assume you are maintaining electrical contact throughout the anode(s). I also don't know why the opening of the anode is facing away from the part. Is this some type of shielding technique? Cu Electroformers I have worked with keep the H2SO4 on the high end and the CuSO4 on the low end, drop the current density accordingly (otherwise known as the low and slow approach). It sounds like you are using a proprietary system (equipment and chemistry). You will want to contact your supplier to see if they agree with my suggestions. Other than low brightener concentration, here are some other causes of burning.
Current density too high
Metal concentration too low
Inadequate agitation
Bath temperature too high
Anode polarization
Low chloride concentration
Let us know how you make out!
Process Engineer - Syracuse, New York USA
Q. Hello everyone. My name is Mike Campbell and I am taking over Chris's electroforming project here at Mizzou since he has moved on to greener pastures (lucky guy got a job).
The project's aim shifted a bit after Chris's little "fuzzy copper" incident. Instead of trying to PREVENT the dendritic structure, we now want to ENCOURAGE it.
Here's the interesting part. Chris left two weeks ago, and since then, I've run several tests using the same bath that he had. Unfortunately for me, the bath now plates very smooth. In any other situation, this would be very nice, but for this particular project, it is very bad.
This may be a strange request, but is there a tweak to the system that might ENCOURAGE this dendritic (fuzzy) growth?
Thanks in advance,
Mike
- Missouri, United States
June 7, 2008
Q. Hello, I'm fabricating some pieces for an artist by electroplating copper growths onto a plastic part with copper spots. (The attached image shows one such spot under magnification.) I'm using a bright acid solution with high sulfuric acid content, low copper ion content, and no levelers. The artist wants branching dendrites, and operating the solution without agitation has yielded decently course growths but little branching. I want to maximize branching. I understand that the common additives attach to high current density sites and block deposition. Are there any additives that attach to low current density sites?
Thanks!
Printmaker - New York, New York
November 13, 2019
Q, A, or Comment on THIS thread -or- Start a NEW Thread