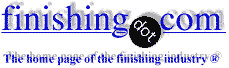
-----
Rust in Threaded Holes Caused By Zinc Plating Process
We send a metal block with threaded holes to an outside shop for zinc plating. They use bolts in the holes during the plating process, but rust forms in the voids. After the zinc plating process, the shop covers the threaded holes with oil and ships back to us.
The threads are difficult to get in deep enough to clean off the rust. And, my supplier is claiming there is nothing more they can do. Are there any possible pre-plate solutions or process changes that can help eliminate rust in no-plate areas during a zinc plating process?
Quality Engineer/SDE - Peoria, Illinois, USA
March 20, 2008
First of two simultaneous responses --
What size are the holes?
Is he making electrical contact thru one or more of the holes?
Two wraps of teflon tape prior to inserting bolts wouls reduce the liquid that gets into the holes. Going into an alkaline rinse tank before going into the alkaline tank would partially fill the holes with a less corrosive material.
Some holes could use rubber plugs. Some silicon plug Mfg's make an insert able sleeve that expands out to fill gaps, He could cast threaded RTV plugs, he could grease the threads in the block before putting the bolts in and he could flush the threaded holes out with a jet of water to remove the traces of chemicals that did not flush out in the rinses. In short, there are lots of things that could be tried-some will cost you a little bit more.
- Navarre, Florida
March 21, 2008
Second of two simultaneous responses --
Jim,
Instead of using bolts in the holes why not use soft rubber hole plugs? If they are using metal bolts, how about polypro or teflon bolts? The seal is obviously inadequate, there has to be a better way. Good Luck.
process Engineer - Syracuse, New York
March 22, 2008
Thank you for the feedback and suggestions. That was exactly what I was hoping for. I will try to update and let you know how it goes.
Thanks again.
- Morton, Illinois, USA
March 26, 2008
Put a five on it.
Jeremy Shaw- Compton, California
March 28, 2008
Try rinsing well between processes especially acid and passivation making sure last swill is clear water then blow out holes with air hose before drying
Bernard Jackson- Redditch, Worcs, United Kingdom
April 23, 2008
Q, A, or Comment on THIS thread -or- Start a NEW Thread