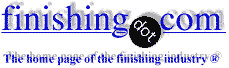
-----
Dyeing/Coloring Hardcoat Anodize Q&A
Current question and answers:
July 27, 2021Q. I have a customer part which is requesting for Type 3 Class 2 Anodizing, we are able to meet the thickness of the coat which is 40-60 microns. However, after black dyeing I can't seem to match the color of a sample piece given to me by the customer. Details of my process is below.
Part Material : Alu 5083
Dye: Sanodal Deep Black MlW
Dye Concentration: 10 g/l
Temp : 55-60
Immersion time 10-20 mins
Please advise.
- Singapore
A. Tommy
Are your parts receiving either a hydrofluoric or nitric acid dip prior to black dye? This is a critical step to achieving a good black color.
supervisor - Cicero, Il USA
August 7, 2021
⇩ Related postings, oldest first ⇩
1998
Q. Having a problem color matching hardcoat. Very tight range for color: must be a medium grey, and thickness of .0015"-.0017". Current density is used, and we control the time. Are there many factors in the process: time, current density, bath makeup, racking? Parts are approx. 1 sq. ft. in area. Thank you, stan
stanley vilakisA. Stan,
It is a tough job.
What kind of material are the parts you want to anodize? Hard coatings on aluminum alloys usually have intrinsic colors, so they are generally dyed in black color. If you want a medium grey color, you need a clear hard coating using special process with proprietary additives. Although raising temperature might help a little bit, it will reduce hardness and could cause burning problem, especially for 2000 series and 7000 series.
Ling
Ling Hao- Grand Rapids, Michigan
1998
A. The factors you mention are important and along with tank temperature, part temperature, and agitation are all inter-dependent. Note the term "part temperature". Agitation must be uniform throughout the tank to maintain the parts at the same temperature. This is especially true if you are using high current density, e.g., 36 asf. Hopefully your ramp up is automatic.
You didn't mention the alloy but there is one factor you may or may not have any control over: alloying elements affect color, and the content of the alloying elements of a particular alloy can vary quite a bit. For example, the silicon content of 6061 is listed as 0.4-0.8%. Silicon is one element responsible for turning hardcoat grey. We could also talk about the importance of consistent temper, but you get the idea.
Those of us who have been involved in color anodizing for many years learned very early to establish not one color standard, but two- an acceptable light and an acceptable dark standard. AAMA has established this as standard practice in their specifications. Considering all the variables you need to control, and the likelihood for color variation, you may need to establish this practice.
Phil Johnson
- Madison Heights, Michigan
1998
Multiple threads merged: please forgive chronology errors and repetition 🙂
Getting our hard anodising black
Can we put an additive or dye in our hard anodizing bath to make the components come out black? If so what do we use? We find the green / olive colour varies too much with the different grades of aluminium.
Martin McElweeNew Zealand
1999
![]() |
A. We often dye our hardcoat anodize black. It is not done in the hardcoat anodize bath. The dyeing is done as a post treatment just like in normal Type II anodize. David A. Kraft- Long Island City, New York 1999 A. A full thickness (50um or 2 mil) low temperature (0C or 32F) hardcoat should be consistently dark. Hot tanks and/or thinner coatings will produce lighter and more variable anodized coatings. They can be dyed black, however, these coatings may not meet your customer's wear and corrosion requirements if they expect a conventional hardcoat. Chris Jurey, Past-President IHAALuke Engineering & Mfg. Co. Inc. ![]() Wadsworth, Ohio ![]() 1999 A. Greetings Martin, There is of course a way to do this, but it doesn't involve addition of anything to your hardcoat anodizing bath, its just a standard black dye that can be purchased (from here in the states at least) from 3 manufacturers that I know of. Matthew Stiltnerplating company - Toledo, Ohio 1999 |
Want hard coating tto be light not dark
Treatment &
Finishing of
Aluminium and
Its Alloys"
by Wernick, Pinner
& Sheasby
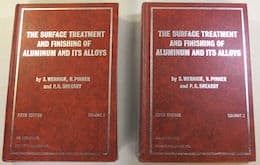
on eBay or Amazon
or AbeBooks
(affil link)
Q. I am working on a project that incorporates both Teflon impregnated hard coated components as well as regular clear coat anodized. Aesthetics are very important for this project and we are hoping to find a way to get the hard coated piece to have a color as similar as possible to the clear anodized parts. All the parts are 6061-T6. What can we do to affect the color of, specifically to lighten, the hard coat.
When we had samples of the hard coat done they were, unbeknownst to us, a 50 series aluminum and it was very similar in appearance to the clear coat. We were shocked when we got our initial order in and the hard coat pieces were dark grey; 6061-T6. Was the alloy the only reason? How light can we get the color on 6061 if we do a very thin hard coat?
Thanks,
Dugan O'Keene- Melrose Park, Illinois, USA
2002
A. One of the hardcoat anodize processes we do here produces only a slight, if any, color change on 6061. The thinner the coating, the less the color change.
David A. Kraft- Long Island City, New York
2002
Q. We have a continuing job that requires 7075 Aluminum rod to be centerless ground then clear hardcoat anodize and then centerless ground again removing some of the hardcoat. The color of the finished parts continue to vary from navy green to gray to grayish brown, some with stains. We use the same ISO vendors and order the stock from the same company each time. All processes have been verified to be done the same each time. Why does the color continue to vary?
Lucy Hatchjob shop - Beverly, Massachusetts
2004
? Why does a clear coating have any color at all?
Chris Jurey, Past-President IHAALuke Engineering & Mfg. Co. Inc.

Wadsworth, Ohio
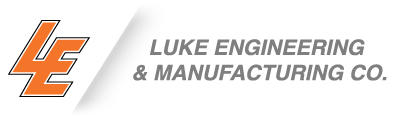
2004
A. Lucy,
One possible problem is that not all 7075 is created equal. Each lot probably has some variances (allowable) in the alloying constituents (I've griped about the inconsistency of American-made AL in this forum before). Unless all of your 7075 came from the same LOT (not vendor), some variances will probably continue to occur. Have you thought about having these parts dyed black? That way, at least all of your parts will be consistent. Other possibilities include varying current densities, anodizing bath temperatures, or different methods of sealing. All of these have a bearing on the final appearance of the coating.
If you did a search on type 7075 on this site, you will note that its not the easiest of alloys to anodize, it can be quite tricky.
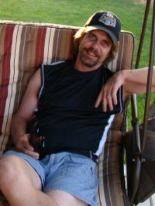
Marc Green
anodizer - Boise, Idaho
2004
A. Hard coat color will vary with very minor differences in alloy, temperature, current density (How accurate is the anodizers surface area measurement? I have a 1956 paper which has the very best gimmick for always getting the same current density), dissolved aluminum, rack contacts, time, thickness, and on and on. Tighten up all parameters.
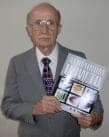
Robert H Probert
Robert H Probert Technical Services

Garner, North Carolina
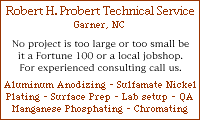
2004
Multiple threads merged: please forgive chronology errors and repetition 🙂
What is the natural colour of 7075 Aluminium Hardcoat
Q. Hi
Can any one tell me What is the natural colour of 7075 Aluminium Hardcoat HAIII
... also ...
Does anyone know which Al-Alloy would produce a Dark Grey-With Slightly Green Hue HAIII if it is not 7075?
Thanks,
flashlights - Bath, Somerset, UK
2006
A. 7075 after hardcoating is a gold to a milky gold green.
All color after hardcoating is 100% dependent on alloying materials.
6061-T6 will give you gray color.
plater - Charlotte, North Carolina
2006
March 12, 2008
Q. We use Hardcoat Anodize on many of our commercial products for its wear and hardness characteristics. We often substitute hard coated aluminum for steel as bearing surfaces. Typically these are pneumatic grippers. We coat typically .010 - .012" ^.0010 -.0012" and often use teflon.
Our problem is the color is difficult to control. We use several different flavors of aluminum for a base material. The different alloys and the fact some parts like piston caps are very thin and very little surface area, etc. etc. means that one part may come out green and another gold. We also have issues with the same part from two batches not quite matching. The result is when all the parts are put together you get several shades ranging from almost gray up to gold. The product looks like junk.
We considered adding dye to the hardcoat but our hardcoater said it would reduce the life of our product by 30%. Not sure how he'd know that without testing our parts is there any issues with adding color to hardcoat?
Can I still use teflon?
Will it reduce wear resistance?
Any suggestions would be greatly appreciated.
Thanks,
design engineer for OEM - Monroe, Connecticut, USA
A. Your anodizer is giving you worst case, but it is well established that dye and seal will reduce the hardness and the wear resistance of hard coat. I question your stated thickness of the hardcoat. Anything over 0.003 per side is questionable or requires extremely high voltage. Do a search of this site for hard anodizing and hardcoat. It will be educational.
Teflon will reduce the wear on other parts, but it will wear over time when compared to the hardcoat.
- Navarre, Florida
March 14, 2008
A. Scott
If you hard anodize parts from different heat lots of material, different 'colors' will be a possibility. Dyeing the parts black should ensure you get uniform color.
To determine if the dyeing steps will degrade the quality of your product, runs tests on both dyed and non-dyed parts, that simulates the conditions for which the hard anodize is required, be it wear resistance, hardness, or adhesion for your coatings.
Your hardcoater may be sealing the dyed hard anodize, which will soften the coating but help prevent fading of the color/dye.
- Colorado Springs, Colorado
March 15, 2008
Thanks. You're right to question my thickness. Typo on my part. Need to shift the decimal point. It was 0.0010 - .0012" thickness.
- Monroe, Connecticut, USA
March 17, 2008
Multiple threads merged: please forgive chronology errors and repetition 🙂
How many colors are available for hard-coat anodizing of 6061-T6 alum?
August 22, 2008Coating specialists,
We are currently getting some 6061-T6 alum parts hard-coat anodized with .0010" per side build up. Our parts have been black in color, but we have been asked if there are any options when it comes to color. The parts (cams for a hunting bow) are about 4" dia. and about
5/8" thick. We are now tumbling these parts to get a uniform surface finish before anodize (thanks to information from hot letter #49679 to finishing.com). Are there any color options for us? We are also interested in any different type of finishing that will make the parts as scratch proof as hard-coat, but maybe more possibility in colors..... The parts will obviously see some outside weather, but appearance is very important to us since these parts are publicly sold. Any help would be greatly appreciated......
Thank you,
cnc coordinator/assistant foreman - Andersonn, IN, USA
![]() |
We did cams with type II anodize, modified, and a good dye job in many colors with black being the most common. We used the max strength of sulfuric acid allowed by the mil spec, 65 °F temp and the max allowable thickness with very good results. Not hard coat by any means, but it was adequate for the use and took dye very well. - Navarre, Florida August 26, 2008 August 26, 2008 The color choices are UNLIMITED. Any of the competent dye companies will match any color you want. ![]() Robert H Probert Robert H Probert Technical Services ![]() Garner, North Carolina ![]() Different hardcoat processes produce different background colors naturally - some very dark & thus it is hard to then dye decorative colors. The hardcoat process my shop runs produces very little background color thus we are able to offer our hardcoat dyed in any decorative color. David A. Kraft- Long Island City, New York August 27, 2008 |
Color of 50 micron thick anodising
Q. Hi,
I'm looking for some help on a 50 micron thick anodise. We have carried this out but our customer has commented that the anodise color seems too light and therefore can not be at the 50 micron thickness. This is on aluminium by the way
They have said "If the hard anodising is done to 50 micron depth, it will be black or near black without any colouring. You can tell easily because the finish tends to be slightly glossier than if black dye is used. I understand it is often a cryogenic process".
Is this true that, regardless of the anodise coloring, if you use a 50 micron thickness anodise it will be close to black in color?
Appreciate the help in advance
Thanks
- UK
June 29, 2014
A. The color of 50 micron (0.002 inch) thick hard coat anodizing can vary in color as functions of alloy, anodizing temperature, free acid, dissolved aluminum, current density, additive, heat treatment, work hardening, and other causes. 6061 would be dark gray, 2000's would be darker almost black at 180 gm/L, 32 °F, 24 ASF. Both alloys would be lighter in shade with higher free acid, higher temp, and other causes. Change any variable and the color shade changes but the generally accepted industry definition of "hard coat" does not require a color requirement. If he wants a color, then charge extra and be sure his alloy and heat treatment does not change and your parameters do not change.
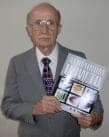
Robert H Probert
Robert H Probert Technical Services

Garner, North Carolina
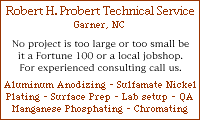
June 30, 2014
Q. Dear Team,
here we did hard anodizing for Cookwares, finish colour is dark grey. Actually issue was we faced colour variation in same piece. Some places are whitish grey and some places are Dark grey? We analyze it but we can't find out the reasons. Thickness of whitish grey area is higher than Dark grey? Is it possible? The Base material is 3003 O temper. I want to know that colour variation of same piece (Whitish grey to Dark grey) is possible? Kindly give me the clear information and ideas!
Plant Incharge-Hard Anodizing - Bangalore, India
June 14, 2017
Jul 31, 2018
Q. Hi,
I am running hard anodizing process (-2 to -7 °C & 165-186 g/l H2SO4) on 6064 aluminium parts and lately facing several problems. Note that all parts undergo degreasing, alkaline etching, and followed by desmutting before anodizing.
Problem 1 - Lighter colour at undercut area
Undercut area occasionally turns out lighter than other surfaces of the same part (as highlighted in red boxes).
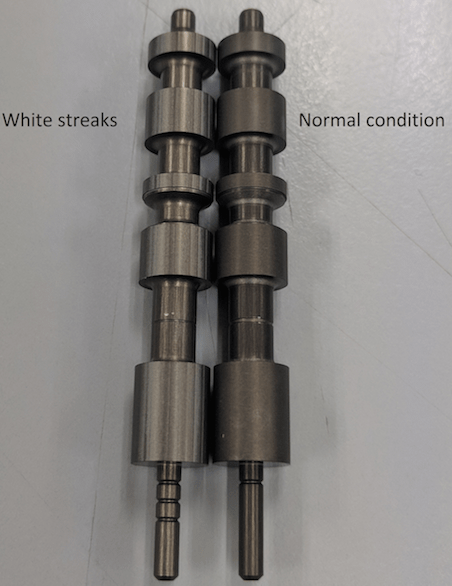
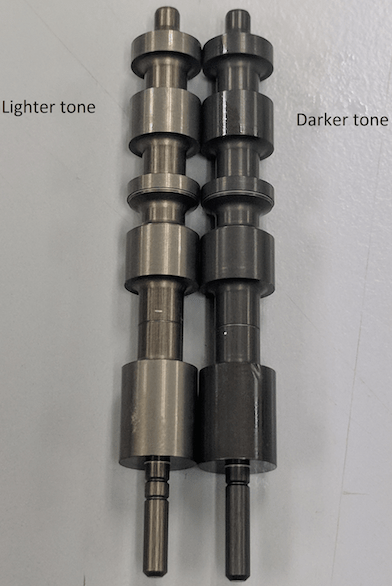
Problem 2 - Big colour variance of parts within the same jig
Is there any default/preferred colour for hard anodizing parts? The thickness requirement for this parts is >10 µ and usually we anodize to 20-25 µ. A jig consist of 210 pieces and we anodize using constant ampere. Lighter parts may have thickness at the lower range but still within the specification.
Problem 3 - White streaks/line across the parts
Although the streaks mentioned has been around for quite a while, lately the colour of the streak became lighter and more obvious. I am wondering if this has any relation to Problem 1. The streak occurs about 3-6% to the total parts processed. It has also been confirmed that any streaks found before anodizing does not effect the visual after anodizing.
Please do inform if any information is needed to guide me. Thanks in advance
Best regards,
Kevin LeeOctober 4, 2018
A. Hi, in my job I look at many similar cases. These chromatic aberrations are often caused by material problems, e.g., material inhomogeneities or use of different batches. 6064 is a free cutting alloy with Bi and Pb, inhomogeneities or different compositions can affect the color. But anodization errors are not excluded. For a clear clarification, additional investigations are often necessary. Also important are the material certificates and measurements. According to the pictures, only an initial assessment is possible.
1) Probably no error from the material or surface treatment.
An influence of the machining is possible.
e.g., insufficient tools can solidify the surface easily. As a result, the layer thickness is thinner in these areas and the color brighter.
A investigation (metallography) could help further.
2) Possible is a different composition. Either different batches or inhomogeneity within the batch.
Analysis and microstructure could be investigated for further clarification.
3. Maybe are inhomogeneities of the chipbreaker (Bi, Pb)
Also, an investigation for the clarification is necessary (metallography).
Differences can often be detected by measuring the electrical conductivity.
I would measure the conductance and layer thicknesses at the different positions and check the material certificate (different batches?) so a better analysis is possible.
AluSolutions - Hallau, SH, Switzerland
A. The color variation could be due to contact UNreliability where some parts get more current thru the sharp contact points. Send us digital pictures of the racking and pay attention to the area of the sharp contacts.
With so many parts in the tank, is there a pattern related to the distance from the cathodes, if so, increase time 30 minutes and see if the color is more uniform.
If I understand your coating thickness, if it as low as you state, then contact resistance is even more probable.
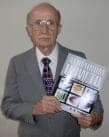
Robert H Probert
Robert H Probert Technical Services

Garner, North Carolina
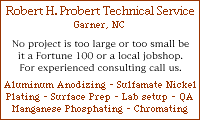
October 4, 2018
Q. We are facing quality issue as shade variation (streak marks) after Hard Anodising of Aluminium HE 30 parts we make.
We could think of two contributing factors for shade variations.
1. Basic Raw material.
2. Anodizing Process at supplier.
We discussed this shade variation issues with supplier of HE30 Aluminium and he said this is because of Magnesium streak in Aluminium.
Can anyone think or know if any other factors Contributing for shade variations apart from Basic Raw material and Anodising process as mentioned above. How can the shade variation in hard anodised aluminium be reduced? Please comment.
- Mumbai, Maharashtra, India
October 15, 2018
Q. We regularly machine 6061-T6 parts and have them anodized. We have 6061-T6 aluminum parts returned from hard coat that are dark on all surfaces except one. 4 sides of the 2-12 square bar are all extruded and have not been machined. One of the 4 sides turned out gray with all the other sides dark. What would cause this?
Scott Washburn- Mansfield Ohio
February 16, 2021
A. If the bad side was away from the cathode, then, the time in the tank at current was not long enough for the current to "wrap" around to the back side, not very common with Type II at 72 °F, but because of the lower conductivity of hard coat at 32 °F, the current did not wrap, need about 20 to 30 more minutes. OR, there was an agitation or gassing problem in the tank.
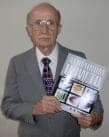
Robert H Probert
Robert H Probert Technical Services

Garner, North Carolina
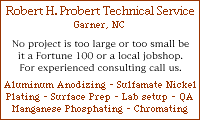
February 23, 2021
Q. Would be great to get this solved as I think I'm going mad...
Customer order for 5251 brackets with a Hard Anodise finish - MIL-A-8625F Type II Class 1. Finish was a dull light grey. Customer has rejected them under the basis that they did not appear to have the same finish as their other products -- Couldn't trust it even with the MIL Cert. We had them picked up and returned to us. They were inspected when they returned and did indeed seem 'too light' but were anodised to this specification.
They sat in quarantine for just over a week when I took them out again to sort a scrap report. To my shock; I genuinely thought they were a different batch to the ones I inspected the week prior: They were a much darker 'classic' Hard Anodise look.
My question is: Is there some sort of curing time with Hard Anodising? What could possibly make them go darker over time? They are 100% the same batch so no cross-over here. Class 1, so no dye.
Would be great to find out.
Thank you
- East Sussex
February 22, 2021
A. In the first paragraph about Type II, I thought about a sealing problem, then when I got down to the last paragraph about "hardcoat" I begin to wonder whether his "other products" were also from the 5000s alloy which, with high Mag, gets a different shade. Come back and clear up whether Type II or hard coat and whether his customer expects us to match shades with different alloys..
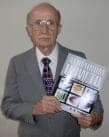
Robert H Probert
Robert H Probert Technical Services

Garner, North Carolina
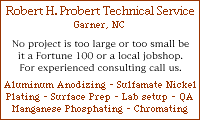
February 23, 2021
Q, A, or Comment on THIS thread -or- Start a NEW Thread