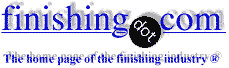
-----
Passivation Test for Stainless Steel series 400
Q. Can anyone suggest a simple and quick test which can distinguish between a piece of nitric acid passivated 420 stainless steel and a non-passivated one?
Could anyone give some comment on my question? Many thanks.
Kwok-wai Chook- Hong Kong, China
2000
Q. Hi Surface Finishing Professionals, After my 2nd inquiry without any feedback, I need to conclude that there is no known simple method to distinguish between a piece of nitric acid passivated 420 stainless steel and a non-passivated one. Regards.
Kwok-wai Chook [returning]- Hong Kong, China
A. Hi, Mr. Chook. Sometimes people are away or busy, or fail to reply for other reasons. Lack of response doesn't imply anything about the answer to your question. Patience please :-)
Good luck.
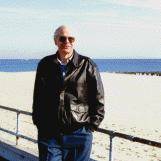
Ted Mooney, P.E.
Striving to live Aloha
(Ted can offer longterm or instant help)
finishing.com - Pine Beach, New Jersey
A. Because of the way nitric acid passivation works there is no easy way to test whether it's been done or not. Nitric acid simply dissolves the oxides from the surface and forms a near complete layer of oxide, which protects the underlying metal from further oxidation. Since no chemical is deposited, and it's a relatively weak method of passivation, it would be very hard to test.
You can compare panels before and after in a corrosion chamber to see the results, but I'm not sure you could test individual panels and determine whether they had been passivated conclusively.
Sorry no-one replied, there's not much of an answer to your question...
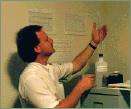
Jeff Watson
- Pearland, Texas
2000
Q. Dear Mr. Jeff Watson, Thank you very much for your comment. I appreciate your sincere reply.
From what you've told me, I understand that there may not be a simple test. When you mentioned a test in corrosion chamber, I would like to have your suggestion on what type of corrosion test (humidity, salt spray or sulfur dioxide) could be done and how?
I am looking forward to hearing from you very soon. Regards.
Kwok-wai Chook [returning]- Hong Kong, China
A. It was my understanding that you could easily check the passivation status of a part using a solution of copper sulphate ⇦ on eBay or Amazon [affil link] and dilute sulfuric acid. An unpassivated part will show copper immersion.
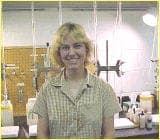
Megan Pellenz
- Syracuse, New York
A. Hi Megan,
the copper sulphate test is still rather subjective on 420 steel because it has so darn much iron vs the 300 series. Temperature of the part is enough to cause it to pass or fail from one day to another.
A friend of mine switched from nitric acid to Stellar Solutions [a finishing.com supporting advertiser] citric acid passivation for 400 series and swears that he has not had a failed passivation or a damaged part since the switch. I would surely recommend a lab test by anyone that does 400 series SS. You only have to have one lot damaged in 30 seconds to hate 400 SS.
James Watts- Navarre, Florida
A. The simple tests for passivation are the acidified copper sulphate test (referred to above) and a ferric cyanide test - both specified inASTM A380 . These tests are primarily checking for free iron on the surface and cannot confirm that nitric acid passivation has specifically been performed. There is a commercial passivation test available from Koslow Scientific Testing Instruments [a finishing.com supporting advertiser] that works on some type of electrochemical basis. This might be more effective, but I don't know for sure.
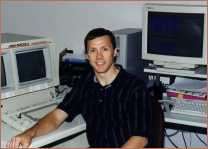
Larry Hanke
Minneapolis, Minnesota
A. You may want to refer to page 552 of the ASM Metals Handbook Vol. 13 'CORROSION' ⇦[this on Amazon affil links]. The only approved test for the 400 series passivation test is 100% humidity for 24 hours and no rust or corrosion shall be observed. I am working on 444 SS passivation check up.
Dianatkhah- Dallas, Texas
Q. I need to know the mixture formula for copper sulphate immersion test on stainless steel.
Tony SantosEngineer - East Hanover, New Jersey
2007
A. I work in a stainless steel company. Since I need to check the passivation layer of sanitary grade pipe, I purchased some equipment from Japan. It cost around USD $1000 for 350 times testing.
The way it works is you drop diluted acid on a filter paper, stick it to the sample and use voltmeter reading (one probe touching the filter paper, another is to the metal sample). This test will basically determine how fast the diluted acid attacks the Chromium-oxide layer. The initial reading will jump to 0.6V in 2 seconds. Then you observe how fast it decays to 0.1 V. This equipment has two kind of probes: one is for 300 series, and another for 400 series stainless.
Luckily I have not found defective passivation layer in all my Chinese goods. But these Chinese goods perform badly compared to Japanese. Japanese stainless steel jumps to 0.6 V initially and decays to 0.4 after 50 seconds. I did not continue reading until 0.1 as this Japanese stainless has definitely a good passivation layer.
Chinese product: jumps to 0.4 V and decays to 0.1 V only within 20 seconds. But according to the passivation kit seller, this is still not considered as defective, although they said it is not a good passivation layer.
- Surabaya, East Java, Indonesia
December 12, 2011
Q. We are using a ferritic stainless steel product that is exhibiting a high degree of corrosion. This happens in the raw material stage, sub-component stage, and final assembly which includes grinding and welding.
The material is a high chromium, ferritic stainless steel that goes by the trademark 3CR12 or UNS41003. We'd like to be able to test for iron contamination at various stages of our manufacturing processes.
1. Does anyone know of the best passivity test for this material?
2. Any recommendations for cleaning or passivation chemicals for ferritic stainless?
- Rainier, Oregon, USA
February 2, 2012
A. Copper sulphate and ferroxyl spot testing are accepted methods. Good luck - you'll need it to get ferritic stainless to pass.
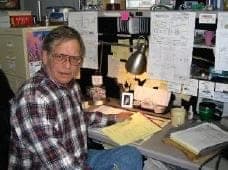
Jeffrey Holmes, CEF
Spartanburg, South Carolina
A. Oh, indeed, those iron-indicator solution tests aren't recommended for use with stainless grades containing less than 16% Cr, like the alloy Jack is using. They are prone to false failures.
For stuff that copper sulphate doesn't do well with, I generally fall back on water immersion testing. There are many variations depending on what document you look at, but I tend to do it heated to reduce the time needed to a few hours.
adv.
Please let me know if we can assist you with your passivation needs.
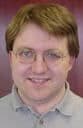
Ray Kremer
Stellar Solutions, Inc.

McHenry, Illinois
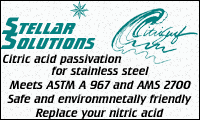
A. I recently bought some 316 S/S bolts to use as liquid level conductivity probes. I pickled them after hand polishing using a 5% hydrofluoric acid and a 22% nitric acid mixture, which is commercially available. I then passivated them with a passivating paste containing a 22% nitric acid solution.
I immersed the probes into a salt water solution and used a multimeter on the millivolt scale to test the voltage between the stainless piece and the multimeter probe. The voltage began rising and reached about 135 mV. This probe is well and truly pickled and passivated.
- Cape Town, Western Province, South Africa
A. Electronic Testers have also been found effective for the identification of passive layers on stainless steel. Far quicker then chemical methods of marking the stainless surface.
Wolf KoslowKoslow Scientific Company

Englewood, New Jersey
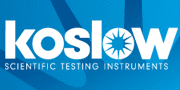
XRF Passivation Test?
Q. I've recently heard references to using XRF for passivation testing. While I've never heard of it, and have no idea how it would work, there are other things I've not heard of so I want to check with the community of experts ... any of you ever heard of using XRF to verify acceptable passivation?
Bob Denney- Loudon, Tennessee
December 9, 2013
A. Bob,
It's not overly common, and certainly not listed in the industry passivation standards, but years ago some customers we had in the semiconductor industry did indeed use techniques such as ESCA and AES to evaluate the passive layer of stainless steel in terms of the depth of the layer and the chromium to iron ratio. (If anybody would like to see this data, let me know.) If you cut a cross section of a piece of stainless and can get good enough resolution from your instrument, I could see getting data via EDS or WDS as well, though the passive layer is only 20-30 angstroms deep at best, so that's probably unlikely.
These are of course rather expensive tests, which is why you'll generally only see the semiconductor industry using them for this, and even then only for process evaluation, not as day-to-day production tests. The common test methods, as seen in the industry standards, are along the lines of iron-indicator test solutions and accelerated corrosion tests. These methods generally give a pass/fail only, or at best a number of hours before corrosion appears. The spectroscopy methods give hard numbers in terms of how much iron has been removed from the surface and how far down that removal extends, which is expected to correlate to corrosion resistance.
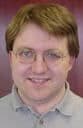
Ray Kremer
Stellar Solutions, Inc.

McHenry, Illinois
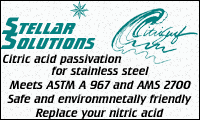
December 12, 2013
420SS Surface rust cleaning
Q. Hi, I have small cylinders made from 420SS that are showing surface rust. The parts are 420SS, vacuum heat treated to 40 HRc then polished in a mild vinegar
⇦in bulk on
eBay
or
Amazon [affil link] /soap mixture to shine them. The parts are then processed with a soy based grinding oil, fixtured in aluminum trays and degreased with NPB (N-Propyl Bromide) in a vapor degreaser. A few hours/days later, spot surface rust develops. 2 questions:
1. Is there any way to clean the rust once it has formed and prevent it from coming back?
2. Is there something about the process that stands out as a major issue that would be causing this?
Any help or ideas is greatly appreciated!
Thanks,
Mike
Engineer - Lakewood, New Jersey USA
October 22, 2015
A. Good day Mike.
This seems very unusual, given that there is 12% chromium in the alloy. I have seen anomolies in salt spray with SS, as dark spots, but after proceeding with the copper sulphate spot test (as per passivation) there was no indication of iron as a red deposit.
Are you certain it is rust?
Personally, I would use SS for degreasing.
Just a thought.
Regards,
Aerotek Mfg. Ltd. - Whitby, Ont. Canada.
![]() |
Q. Hi Eric, - Lakewood, New Jersey USA A. 420 Will rust, but it is normally caused by ultra thin smudges of steel from fixturing as in your grinding operation and possibly the attachment to the aluminum part. - Navarre, Florida A. Mike, adv. ![]() Ray Kremer Stellar Solutions, Inc. ![]() McHenry, Illinois ![]() October 23, 2015 |
![]() |
Q. James: Yes, we check acid weekly in the degreaser, it has been steady with minimal need for booster. - Lakewood, New Jersey USA A. Mike, adv. ![]() Anna Berkovich Russamer Lab ![]() Pittsburgh, Pennsylvania ![]() |
A. Mike,
Okay, that makes some sense. Our recommendation with 400 series stainless is to heat treat to full hardness prior to passivation. Parts that are not heat treated become severely etched by the acid, clearly the microstructure that contributes to hardness also is a factor in holding up to corrosive exposure. All of which means you should to run some passivation trials here and see how things hold up.
What we recommend for 420 is an alkaline pretreatment, a rinse, citric acid product passivation acid bath, two or three rinses, and immediate drying.
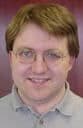
Ray Kremer
Stellar Solutions, Inc.

McHenry, Illinois
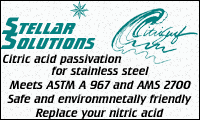
and Chemical Polishing
of Metals in
Research and Industry"
by W.J. Tegart
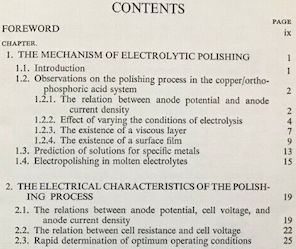
on eBay or Amazon
or AbeBooks
(affil link)
Anna, Thanks for the advise. Are you aware of a good method of bulk electropolish? Our typical batches are 3,000 pieces and racking is not really feasible. Or is there some other method that could be better with a bulk process?
Ray, Thank you, we will look into some passivation trials.
- Lakewood, New Jersey USA
November 2, 2015
Hi Mike,
Universal electrolyte allows to electropolish in a wheel (if parts are not flat, do not stick to each other and move during wheeling. Bulk electropolishing is one of the advantages of UE. We can run some tests for you.
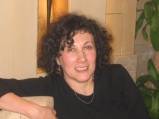
Anna Berkovich
Russamer Lab

Pittsburgh, Pennsylvania
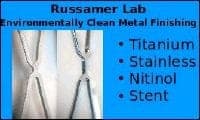
Q, A, or Comment on THIS thread -or- Start a NEW Thread