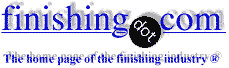
-----
Type III Hardcoat Coating Density Measurements
We are currently in the process of running a series of tests to optimize our type III hardcoat process and would like some help with how to calculate coating density measurements. We have been using Taber wear test panels to check thickness, abrasive wear, and coating density. Thickness and abrasive wear results have all been within specifications but our coating density results were below the minimum 4320 mg/ft2 per .001 as specified in the MIL-A-8625 / MIL-PRF-8625 [⇦ this spec on DLA]F standard. One of the variables in question is what thickness measurement is to be used for the coating thickness. Do we take the average thickness from each side of the panel (~2 mils) or the TOTAL thickness (~4 mils)? Use of the 2 mil average thickness will get us above the 4320 mg/ft2 per .001 specification. Thank you!
Dori KimMfg. Engineer - Rockford
February 18, 2008
First of two simultaneous responses --
Dori
The calculation should be straight forward. Your coupon is of a known surface area. Weigh the coupon, strip the anodize, and reweigh. Calculate the weight/sq.ft and divide by your thickness expressed in mils (.001")to get your per mil weight.
If the majority of your work is 2-mil thick, use a 2-mil thick coating on your coupons. As long as you are on a fact finding mission, test coupons at 1-mil and 1.5-mil thickness while your at it.
If your per mil weight IS low, look at lowering your operating temperature (30 F) or acid concentration (165 - 200 g/l free), and raising your current density (30 ASF).
While we do not test coating weight, we are typically at .6 -.7 mg weight loss on the Taber test running at 225 g/l free acid, at 30 F and 30 ASF.
- Colorado Springs, Colorado
February 22, 2008
Second of two simultaneous responses --
Just note that the aluminum oxide pore is small at the bottom and large at the top, therefore, the coating is more dense close to the original surface and less dense close to the top (where eventually it goes into 100% dissolution).
This is the conceptual reason that you never hear of people measuring
"hardness".
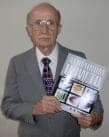
Robert H Probert
Robert H Probert Technical Services

Garner, North Carolina
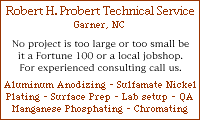
February 23, 2008
Willie is spot on in his advice, the one thing I would add would be to strip the anodic coating in something that will not attack the base metal, ie, a heated chromic acid/nitric acid/DI water solution. Don't use sodium hydroxide, as this will attack the base metal, and effect your coupon weight.
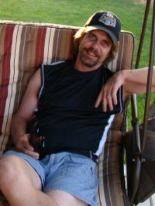
Marc Green
anodizer - Boise, Idaho
February 25, 2008
I assume from the replies above that we should be using 2 mils for the coating weight calculations since using eddy current shows 2 mils per side on a Taber panel. We had been using 4 mils (the total coating thickness). Thanks everyone!
Dori Kim- Rockford, Illinois
February 28, 2008
----
Ed. note: In proofreading postings here, we see the spelling "Tabor" as well as "Taber". An interesting fact is that Dr. David Tabor developed hardness & indentation tests and wrote books on the subject, but Ralph Taber founded the Taber Abraser company. I guess we'll go with "Taber" on this site :-)

Q, A, or Comment on THIS thread -or- Start a NEW Thread