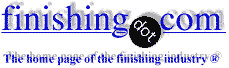
-----
BLISTERING OF LEAD/TIN PLATING ON COPPER BUSBAR
Dear Sirs:
I will have to provide you with much detail to understand this problem. Please bare with me.
We are a job shop, fabricating copper busbar and plating most of it ourselves.
For one of our customers, we plate 97/3% lead/tin, with a requirement of 3 mil [.003"] thick. This customer uses this copper bar in a battery pack. They preheat the bar to 300', then solder/tin dip the part in a pot for 10 seconds [at around 600'], then place it in a heated lead mold.In the past 5 years, without any kind of time pattern, they have had instances of our plating blistering, in one of these 3 processes. About 7 instances in the past 5 yrs. Of course, we do a sample test of parts going out {500' at 20 mins per their test spec] but seem to never find the problem in house.
When the parts return, one common find in testing the lead/tin composition {using a x-ray unit} is that they are high in tin content. Typically 7% tin or more. Since we do use a 93/7 bath for other products, we do understand that mistakenly plating parts in an incorrect bath may be a cause.
So the running theory is, if the part has a high tin content, it will blister when heated.
This is the most commonly agreed on theory.
My contention is, though this partially correct, to say cut and dry this is the only reason for blistering is wrong. Other factors may be involved, such as the typicals: tank contamination or insufficient cleaning of the part.
The plating bath has peptein added to it to keep the plating smooth. Since it is an organic substance, I know it has a possibility of breaking down over time.
If tank contamination is to blame, do you think this could skew the x-ray readings of tin content, via the contamination {carbon most likely...I am not a chemist} and the tin molecules attaching themselves to it and coming to the surface? it is also important to know that these tanks are being used all the time to plate other copper bus that are not heated.{could the contamination be plated out during the non heated parts process}?
Can anyone give any thought, opinions on this issue?
plating shop employee - Decatur, Tennessee, USA
February 1, 2008
Have you considered copper contamination of the plating solution which would plate copper out with the lead and tin, and would vary from time to time as the copper dummies out on some parts in the low current density areas? It is for this reason that when I spec a buss bar job I call for a "strike" tank to act as a sewer and catch the copper to prevent it from plating out in the finish tank. The two suppliers I used to work for did not like this becasue it made the finish bath last too long and use too little proprietary additives.
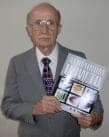
Robert H Probert
Robert H Probert Technical Services

Garner, North Carolina
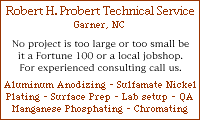
David,
I doubt very much that the problem lies in a slightly higher tin content in the alloy. I've solder dipped a lot of 93/7, 90/10, 60/40 without any problems. The tin content of course being the higher percentage. If I understand you correctly, we are talking 93% lead - 7% tin. I think you were on the right track when you mentioned a possible problem in the cleaning of the copper. Blistering usually occurs when the substrate is not cleaned properly. When the subsequent plating layer is exposed to heat, adhesion values are at great risk, especially an unclean substrate. It is also important that the fluoboric acid dip prior to Pb/Sn plate is changed frequently, and kept clean. Another factor contributing to blistering is the amount of time your plated part is stored at your customer's facility, and for that matter, how is it stored. Before the part is solder dipped, migration of the copper (with any contaminants) can come through the plated layer over time. Hope this helps you!
Process Engineer - Syracuse, New York
Q, A, or Comment on THIS thread -or- Start a NEW Thread