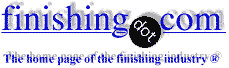
-----
Copper strike solutions for barrel plating
January 4, 2008
Greetings:
I run a captive barrel plating line putting nickel and gold on brass and beryllium copper components. We are looking at our copper strike chemistry, and have begun to wonder whether we are using a formulation that makes sense.
Factory conditions preclude the use of cyanide copper, unfortunately, leaving us with a choice between acid copper and pyrophosphate. Within those limitations, what would the best choice be?
I appreciate any advice anyone can offer.
Plating Shop Employee - New Hanover, Pennsylvania, USA
First of three simultaneous responses -- January 4, 2008
Dear Raymond,
I agree, it doesn't make any sense to use a copper strike in that case. No advantage and serious rinsing problem. If your pre-treatment is well designed for copper alloys, there's no need to add any process before nickel plating. If you are not sure or you have reason to hesitate, the right solution will be always nickel strike
(pre-nickel) before bright nickel plating.
Greetings
- Warsaw, Poland
Second of three simultaneous responses --
I think you should look at proprietary alkaline non cyanide chemistry from several manufacturers. They have available non cyanide strikes that offer improved performance to pyrophosphates. Some of the European developed products do not use propietary anodes and do not complicate waste treatment (a consideration to look at with alkaline non cyanide processes)
Gene Packmanprocess supplier - Great Neck, New York
January 5, 2008
Third of three simultaneous responses --
Hello Raymond,
Acid copper would be the choice for plating over the strike. Pyrophosphate solutions are more difficult to control, and have a much shorter bath life than cyanide Cu strike baths. Orthophosphoric acid ion concentration increases because of pyrophosphate ion hydrolysis. Also the deposition rate is slower because you are plating divalent copper as opposed to monovalent (cyanide copper). Have you considered a non cyanide alkaline copper strike? This website has good suppliers that support it through advertising, and can help you with the proper strike for barrel plating. Looking for products and services link will help you. I am not supposed to give supplier or proprietary bath info. Good luck to you.
Process Engineer - Syracuse, New York
January 6, 2008
Q, A, or Comment on THIS thread -or- Start a NEW Thread