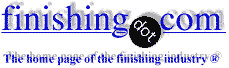
-----
Electroforming with electroless nickel EN
Is there any fundamental limitation regarding the thickness of an EN deposit? It seems that if the phosphorus range is selected for a zero or very low stress deposit, and you have plenty of time (days) there shouldn't be a reason you couldn't form a 2mm deposit of EN. Is this logic reasonable?
Sam ElliotShop employee - Los Angeles, California, USA
2007
First of two simultaneous responses --
Logically, it would work, but in real life you run into problems above 0.0015 inches. Some people have no problem with 0.0020 inches, but very few can do better than that without pits or dimples forming.
James Watts- Navarre, Florida
January 4, 2008
Second of two simultaneous responses --
Yes. We have sometimes run our electric titanium heaters until the were covered with 1mm or more of EN before striping them (specially when working one or two days non-stop). So, EN will achieve the thickness you mention. Only problem is that those shells will be extremely brittle (like thin glass) and tend to adhere more to conventionally passivated surfaces due to the low efficiency of EN, so you will have to test your mandrel process and separation technique to avoid breaking the EN-form before attempting to produce a real part.
Guillermo MarrufoMonterrey, NL, Mexico
January 5, 2008
Heaters do not count as they are hotter than the parts, so will plate very heavy. I used double derated heaters in EN when I could not afford Teflon, to avoid that problem and to avoid the high cost of lost nickel.
James Watts- Navarre, Florida
January 10, 2008
Here's my point, Jim. The man is wanting to form a shape via EN deposition. So, I assumed he would have a mandrel. So, unless the mandrel is made of a heat sensitive material, there's no reason why he couldn't heat it up and make it plate heavy, just like an immersion heater.
Guillermo MarrufoMonterrey, NL, Mexico
January 12, 2008
Whilst I do not profess to be an expert in electroless nickel, I was under the impression that most electroless nickel deposits are quite highly stressed. This could cause significant problems in an electroform. Furthermore, I have always thought that electroless nickel deposits at about 15-20 microns/hr, which is equivalent to an electrolytic rate obtained with a current density of about 12-17 ASF. To deposit 2mm will take over 100 hours, based on the bath working at high efficiency. Depending on what the electroform is to be used for, it is quite possible that the electroless nickel will need a very careful heat treatment to wrap up the phosphorus in the deposit. Has anyone else any comments on this?
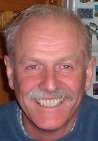
Trevor Crichton
R&D practical scientist
Chesham, Bucks, UK
January 14, 2008

Q, A, or Comment on THIS thread -or- Start a NEW Thread