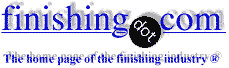
-----
How to accelerate pitting of cold rolled 1 1/4" hexagon
I have a huge problem, but than don't we all. I have 160' of 1 1/4" hexagon stock that has been sitting outside for about 4 years, and over those 4 years the steel has pitted pretty deep, with some pits as deep as .0625, that is not the problem though. I'm a blacksmith and I made a rail sample using the old material, and of course the customer loves the way that it looks. The problem is that I'm 200' short of material, so how can I pit new stock to look years older than it is. I plan on mixing the old with the new, but the new still has to have some deep pitting. Any help that you can give would greatly appreciated.
Roger Bowieblacksmith / fabricator - Groton, Connecticut, USA
2007
2007
Think safety and use appropriate cautions before trying this.
Buy some 4 inch pvc pipe, cap the ends and cut it in half, the long way very carefully. Use
muriatic acid
⇦ on
eBay or
Amazon [affil link] that you pre treat with about 1/4 of a 0000 or 00000
#0000 steel wool
⇦ on
eBay or
Amazon [affil link] to a gal of acid to get some iron chloride into the acid. I would use a solution of 1 part pool acid to about 1/2 part water. Face mask,
apron
⇦ on
eBay or
Amazon [affil link]
and plastic/rubber
rubber gloves
⇦ on
eBay or
Amazon [affil link] , put one rod in each half for probably a day--possibly shorter and possibly longer Turn the rod every couple of hours to get a more uniform etch on all
6 sides. The amount of mill scale will affect how fast each rod reacts. Rinse very well with lots of water and or bicarbonate of soda solution. It will flash rust very very rapidly. There are some other ways to speed it up, but this should work.
- Navarre, Florida
Thanks for you help, it seems to work but kind of slow. So of course I got the idea of why not speed up the process with hooking a dc power source up, hooked up the ground to the hexagon stock thinking that with the postive hooked up to the copper rod that the steel would migrate to the copper but the hex got copper plated in like 5 mins. So I reversed the leads and the copper sizzled like bacon in a pan, and after 6 hours was able to get the results that I need. Was this what you had in mind when you said " There are some other ways to speed it up," Again thanks for your help.
Roger Bowieblacksmith - Old Saybrook, Connecticut, USA
January 7, 2008
That is what I had in mind, and the copper chloride that you formed with it hooked up the first way also formed a very good catalyst for the etching.
James Watts- Navarre, Florida
January 9, 2008
Q, A, or Comment on THIS thread -or- Start a NEW Thread